BMI-689 Low Viscosity Liquid Bismaleimide
- Hydrophobic
- High adhesion to various substrates
- Superior thermal stability
Product Description
BMI-689 is a unique low viscosity liquid bismaleimide based on a non-hydrogenated dimer diamine backbone. It can be homo-cured via UV or free radical initiators to form tough, hydrophobic, cross-linked polyimides. The material has excellent low pH hydrolytic resistance and thermal stability. The amorphous nature of this BMI allows it to be used in a variety of applications including mixed cure systems (e.g. epoxy and BMI), mixed BMI systems or where a low viscosity, free radical cured resin is required. It is soluble in most aromatic and aliphatic solvents such as toluene, xylene, NMP, etc.
BMI-689 is recommended for use as an additive or base resin in adhesives that are designed for high temperature resistance. It has excellent adhesion to a variety of substrates. When used as a base resin, it can produce films that are tough, flexible and demonstrate good peel strength.
BMI-689 cures free radically so it is subject to oxygen inhibition to some degree. Thermal curing with an abundance of catalyst will usually overcome the problem. Bmi resins do demonstrate self photoinitialization when exposed to UV but polymerization is more complete and requires much less energy when a UV photoinitiator is used in the formula. We would not suggest using UV without an initiator for our BMI resins. Our favorite initiator is Irgacure IR-819. It works well in broad band and i-line systems.
BMI-689 has a Tg value of around 45ºC by DMA. When measuring using a TMA the values are lower by 20 - 30ºC so you would be looking in the 10 - 25ºC range for a pure BMI formulation. Very low. This is why we suggest using acrylates to boost the Tg of formulations if your hydrophobicity concerns allow for their use.
It is unfortunate that the BMI resins, with all of their good properties, have such low Tg values. However, we have been successful in convincing several customers that a high Tg - in certain applications - may not be a requirement for BMI-based applications as they have been in epoxy and even acrylate formulations. If a high Tg was required strictly to maintain adhesion (eg. in an epoxy material) you might find that the BMI materials do not lose adhesion in a similar manner at higher temperatures.
Technical Specifications
General Properties | |
Appearance Appearance Appearance at room temperature. | Yellow to amber liquid |
Functionality | 2 |
Molecular weight | 689 g/mol |
Physical Properties | |
Viscosity Viscosity Viscosity is a measurement of a fluid’s resistance to flow. Viscosity is commonly measured in centiPoise (cP). One cP is defined as the viscosity of water and all other viscosities are derived from this base. MPa is another common unit with a 1:1 conversion to cP. A product like honey would have a much higher viscosity -around 10,000 cPs- compared to water. As a result, honey would flow much slower out of a tipped glass than water would. The viscosity of a material can be decreased with an increase in temperature in order to better suit an application | 1500 mPa.s |
Thermal Properties | |
Decomposition Temperature | >400 °C |
Other Properties | |
Storage Temperature | 5 °C |
Additional Information
The use of DMI BMI-BCI resins with epoxy can add a great deal of flexibility when optimizing a resin system to meet specific needs.
- The BMI-BCI/epoxy system can be cured in air for a tack-free surface.
- Data shows lower cure temperature than either resin cured alone.
- Increasing the BMI-BCI content decreases the moisture absorption of the system.
- Small quantities of epoxy can significantly increase adhesion of the mixture.
Almost linear adjustability is available for properties such as:
- Viscosity
- Glass Transition Temperature
- Coefficient of Thermal Expansion
- Dielectric Properties
Another BMI-BCI/epoxy system feature is that most combinations turn black upon curing without the use of colorants or carbon.
The hydrophobic nature of the DMI BMI-BCI resins helps limit the moisture absorption observed after exposure to 168 hours of 85°C/85% RH. Significant reduction in moisture absorption was obtained with samples containing a high fraction of BMI resin. The more BMI in the system the better the resistance against humidity.
The BMI-689/epoxy system exhibits thermal property changes in a manner similar to that of the viscosity.
The Tg, α1 CTE and modulus can all be controlled by formulation selection.
# | EW Epoxy:BMI | Tg (⁰C) | α1 (ppm/⁰C) | Modulus (GPa) |
1 | 1:9 | 50 | 161 | 0.46 |
2 | 1:4 | 60 | 146 | 0.65 |
3 | 1:3 | 69 | 143 | 0.54 |
4 | 1:2 | 55 | 150 | 0.68 |
5 | 1:1.5 | 44 | 131 | 0.93 |
6 | 1:1 | 43 | 119 | 1.24 |
7 | 2:1 | 58 | 120 | 1.30 |
8 | 3:1 | 83 | 104 | 1.50 |
9 | 6:1 | 100 | 85 | 1.68 |
10 | 1:0 | 119 | 65 | 1.75 |
DK/Df values of cured BMI/Epoxy mixtures were investigated and plotted below. The dielectric properties of the system can be controlled by varying the level of BMI to epoxy.
Blue= BMI-689/epoxy - Orange= BMI-1500/epoxy
It is important to point out the improved shear strength that formulations using BMI exhibit. As you can see, the amount of BMI enhances the compression shear strength on PC/PC substrates in the initial phase and on the long run at higher temperatures. As expected there is a drop in strength at medium temperatures since Bismaleimides are generally made to perform better at elevated temperature conditions.
Something interesting to note is that initial strength at Alu/Alu substrate testing is not performing well and drops from 25MPA to 5 MPa with 20% BMI content. It is possible that this will improve in different analogies and given enough time and temperature but this has not been tested.
Upgraded BMI 689
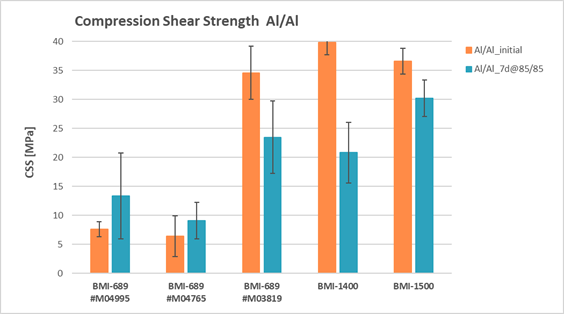
We will be first to admit that our BMI resins do not have great adhesion - especially to metals and extra especially to copper. For this reason we ALWAYS suggest that coupling agents are employed in any adhesive formulation where the main resin is a BMI. We believe the use of coupling agents can significantly increase adhesion to metals of BMI-based adhesives. We routinely suggest the use of coupling agents to all customers contemplating a BMI rich adhesive. The agents listed below have all been used successfully by DMI to increase adhesion.
Functionalization | CAS # |
Amine | 3068-76-6 |
Epoxy | 3388-04-3 |
Methacrylate | 2530-85-0 |
Epoxy | 2530-83-8 |
- We generally use a mixture of coupling agents in our formulas for the best overall performance.
- Coupling agents are normally functionalized silanes. The silane portion bonds to glass and wafers and we try to select the functionalized portion to bond into our resin matrix.
- The quantity to use is formulation dependent but generally less than 2 - 3 % of the resin weight. You must experiment to optimize the level(s).
- Amine coupling agents work great with BMI resins but they can react with the resin at low temperatures and cause pot life issues - use cautiously (we use them all the time so it is possible to add them to your formulas and survive)
- Epoxy coupling agents are effective even though the cure chemistry seemingly doesn't match (e.g. free radical vs epoxy).
You can see how some of the suggestions fare next to each other in the following chart. At the end of the day it seems like BMI 1400 and BMI 1500 are probably better alternatives for Glass and Aluminum substrates. It remains to be seen if the shear strength of 1400/1500 will continue rising once we add coupling agents and adhesions enhancing materials in these products.