Non Conductive Adhesives
Non conductive adhesives can withstand high thermal loads and can potentially provide high shock and peel resistance. They demonstrate excellent chemical resistance, thermal shock and impact resistance while also maintaining a wide operating temperature range.
Our range of Non conductive adhesives (NCA) can achieve great bonding to a variety of substrates while also being thermally and chemically resistant.These Henkel adhesives are designed for us in temperature sensitive electronics such as CMOS image sensors and in high throughput assembly that requires low temperature cure. With an operating temperature range between -40ºC to 130ºC they are ideal for substrate attachment and can be used for lens holder, lens barrel and IR filter bonding.
NCA dual cure adhesives provide improved adhesion to LCP and aluminium for automotive applications and they can be used for automatic dispensing, screen printing and led applications. Their flexibility derives from the fact that they can be dual cured but can also be used either as a single component or two component epoxies with a resin and a catalyst.
LOCTITE ECCOBOND LUX AA50T
- Fast light cure
- White opaque
- LED mounting and optoelectronics
- 8 - 12 weeks
LOCTITE AA 3321
- Flexible bond
- Highly thixotropic
- Excellent adhesion to glass, plastics and metals
- 8 - 12 weeks
LOCTITE ABLESTIK NCA 2286AE
- Dual Cure
- High elongation strength
- Active alignment in lens holder attach
- 8 - 12 weeks
Product Selector Guide
Product | Specific Gravity | Hardness | Viscosity (mPA*s) | Glass transition temperature (°C) | CTE a1 | CTE a2 | Recommended cure | Attributes |
---|---|---|---|---|---|---|---|---|
LINQBOND NCA-3120 | - | 80 | 22,000 | 30 | 70 | 190 | Ramp to 180°C and hold for 10 minutes | Camera module assembly, LED light lens bonding, electronic components, etc. |
LINQBOND SMA3601 | 1.35 | 86 | ≥550,000 | 125 | 64 | 215 | - | Surface mount technology (SMT) applications, demanding electronic device encapsulation, and chip bonding |
LINQBOND SMA3602 | 1.35 | 86 | 70,000 –120,000 | 125 | 64 | 215 | 3min @120°C | Surface mount technology (SMT) applications, demanding electronic device encapsulation, and chip bonding |
LINQBOND SMA3603 | 1.35 | 87 | 150,000 | 98 | 55 | 206 | 150s @120°C | SMT (Surface-Mount Technology) applications, electronic device encapsulation, and chip bonding |
LINQBOND SMA3611 | 1.36 | 89 | 450,000 –750,000 | 121 | 54 | 160 | 120s @130°C | SMT (Surface-Mount Technology) applications, electronic device encapsulation, and chip bonding |
Loctite 3128 | 1.6 | 88 | 27,000 | 45 | 40 | 130 | 60min @60°C | Memory cards, CCD/CMOS Assemblies and Lid/Cap attach for optical sensors and 3d sensing modules. |
Loctite 3217 | 1.2 | 86 | 109,000 | 82 | 53 | 178 | 30min @60°C | Optical applications and the cavity fill of test IC\'s. |
Loctite 3616 | 1.33 | - | 25,000 | 140 | 86 | - | 90sec @150°C | Bonding of surface mounted devices to printed circuit boards prior to wave soldering. |
Loctite 3621 | 1.22 | - | 3,000 | 110 | 100 | 218 | 30min @150°C | Chipbonder. Suited for applications with very high dispense speeds and high dot profile. |
Loctite 3703 | 1.12 | - | 20,000 | - | - | - | 10sec @6 mW/cm2 | PVC to polycarbonate for large gap filling (0.25mm) and a flexible joint. |
Loctite AA 3106 | 1.08 | 53 | 5,000 | - | - | - | 15sec @6 mW/cm2 | Excellent adhesion to glass, many plastics and most metals. |
Loctite AA 3526 | 1.06 | 62 | 17,500 | 36 | - | - | 5sec @6 mW/cm2 | UV/visible light-cured, liquid modified acrylic adhesive. |
Loctite Ablestik 2332 | 1.17 | 75 | 70,000 | 105 | 100 | - | 60min @120°C | Universal adhesive that can be used, among others, for SMD components, caps and lids. |
Loctite Ablestik G500 | - | 86 | - | - | - | - | 60min @125°C | General purpose epoxy adhesive and sealant that cures to a high gloss finish. |
Loctite Ablestik NCA 2280 | 1.3 | 90 | 54,000 | 90 | 45 | 156 | 30 minutes @ 80°C | Dual cure adhesive is designed for use in the assembly of temperature sensitive electronic components. |
Loctite Ablestik NCA 2286 | - | 85 | 40,000 | 28 | 55 | 165 | 4sec @220nm | Use in active alignment applications in camera module assembly. |
Loctite Ablestik NCA 2390 | 1.2 | 87 | 62,000 | 94 | 68 | 170 | 30 minutes @ 80°C | Dual cure adhesive is designed for use in the assembly of temperature sensitive electronic components. |
Loctite Ablestik TE3530 | - | - | 60,000 | - | 36 | - | 30min at 100°C | Bonding heat dissipation components and applied by automatic syringe dispense (2.3 W/mK) |
Loctite DSP 190024 | 1.12 | - | 20,000 | - | - | - | 10sec at 365nm | UV curable sealant for displays. Cured by exposure to UV and/or visible light |
Loctite Eccobond 3707 | - | - | 9,595 | 53 | 52 | 151 | 30sec @100 mW/cm2 | UV + Heat Curable edgebond designed for bonding electronic components on a PCB. |
Loctite HHD 3607BK | - | 75 | 6,500 | - | - | - | Moisture | Moisture curable reactive polyurethane for glass surfaces |
Loctite SF 7360 | - | - | - | - | - | - | - | Cleaner for uncured adhesive and adhesive residues found following PCB assembly. Fully compatible with epoxy adhesives |
*UV Cure Values are indicative of the fixture step. Check the TDS for more information.
Frequently Asked Questions
Why would I want to Dual cure my product?
Dual cure products are formulated to temporarily cure when exposed to UV light, followed with a secondary thermal cure at low temperature. Temporarily curing the material allows for any necessary adjustments to the final device configuration.
What are the benefits of two component adhesives?
Two-component non conductive adhesives require no refrigeration or freezer storage and include products that provide high peel and tensile lap shear strength over a broad temperature range. Two component epoxies are not premixed so they eliminate pot life issues making them easier to use, transfer, store and preserve.
Learn More
Adhesives for CMOS & 3D Image sensors
Key requirements for adhesives that can be used in sensor bonding are:
- Adhesion to variety of substrates (PC, LCP, etc.)
- Low temperature cure - below 100°C
- Fast cure - below 60mins
- Operating temperature range -40ºC to 130ºC
- Low halogen content
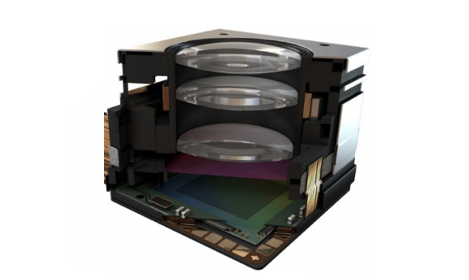
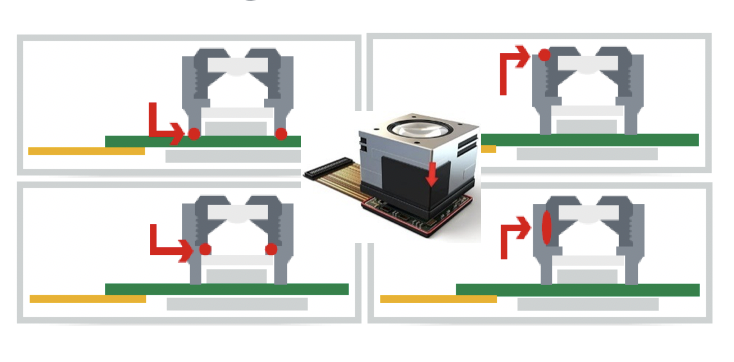
We offer a wide range of adhesives that are suitable as Lens Holder, Lens Barrel and IR Filter bonding. Depending on the process there are adhesives that are stencil printable or dispensable, UV, Heat or Dual cure and with a high range of viscosity and thixotropy ratings.
The usual process for such bonding starts with dispensing the adhesive and then positioning and aligning the component. Next steps usually consist of fixating the component with light cure that is then finalized with Heat curing.Hence the need for dual curing. It is not necessary but it is process dependent and can help with the precision alignment steps.
CMOS sensor bonding process
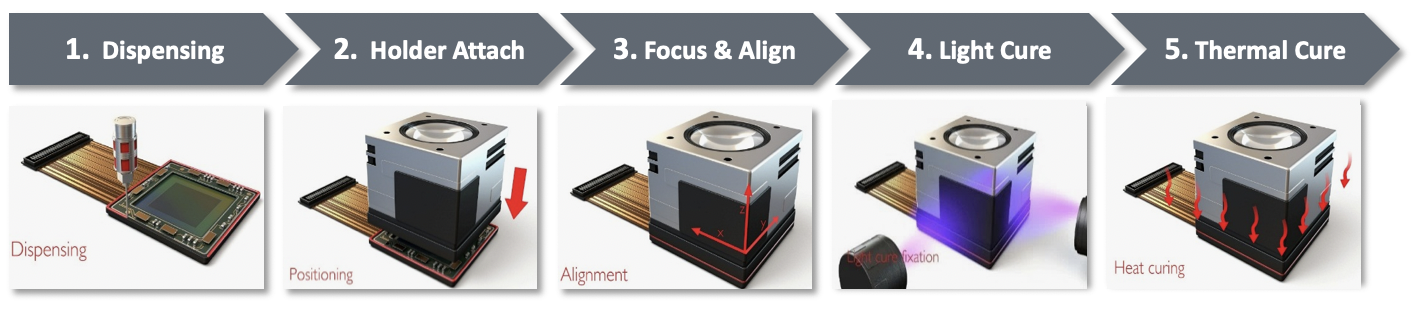