Thermal Grease
Thermal Silicone grease products provide superior thermal performance with ease of use across a multitude of applications. The low viscosity and inherent thixotropy make the technology a good fit for large-scale production with dispensing, screen printing and stencil printing.
Thermal Grease is a common silicone thermal interface material, usually used to increase thermal contact conductance across jointed solid surfaces. Thermal interface materials occupy the space of air (a very poor thermal conductor) and fill in the gaps between two solid surfaces. This establishes an effective thermal path between a heat-generating component and a heat sink attached to it, therefore greatly increasing thermal transfer efficiency.
Silicone thermal grease is a composite containing silicone and inorganic or metal nanomaterials with high thermal conductivity. It has been a great replacement for pyrolithic graphene sheets. Compared with thermal pads or liquid gap fillers, grease has the lower viscosity, and it can be used by dispense or screenprint, forming a thinner thermal conductivity layer with high thermal conductivity performance.
Thermal greases are designed to minimize thermal resistance at inter-faces, and maintain excellent performance through reliability testing. TG series products are offered with varying thermal impedance and thermal conductivity properties to complement different power densities in real applications. Products are also available in a range of bondline thicknesses (BLT) to meet variations in interface flatness.
Product Selector Guide
Product name | Color | Viscosity (cps@25˚C) | Specific Gravity | BLT (um) (35psi, 50°C) | Thermal Conductivity (W/m·K) | Thermal Impedance | Dielectric Constant @1MHz | Contains Solvent* | Volume Resistivity (ohm·cm) | Flammability Rating | Working Temperature (˚C) |
---|---|---|---|---|---|---|---|---|---|---|---|
TG1500I | White | 250,000 | 2.7 | 30 | 1.5 | 0.03 | >5 | No | 1.0 x 1013 | UL94 V-0 | -40~150 |
TG2000I | Blue | 90,000 | 3.0 | 30 | 2.0 | 0.020 | >6 | No | 1.0 x 1013 | UL94 V-0 | -40~150 |
TG2800I | Yellow | 100,000 | 4.2 | 25 | 2.8 | 0.009 | >14 | No | 1.3 x 1013 | UL94 V-0 | -40~150 |
TG3000 | Grey | 150,000 | 2.7 | 25 | 3.0 | 0.009 | >10 | No | 1.0 x 1012 | UL94 V-0 | -40~150 |
TG3000I | White | 200,000 | 3.4 | 10 | 3.0 | 0.003 | >10 | No | 2.0 x 1012 | UL94 V-0 | -40~150 |
TG4000 | Grey | 200,000 | 2.7 | 23 | 4.0 | 0.005 | >10 | No | 1.0 x 1012 | UL94 V-0 | -40~150 |
TG5500 | Grey | 300,000 | 2.5 | 23 | 5.5 | 0.010 | >10 | Yes | 1.0 x 1012 | UL94 V-0 | -40~150 |
*Note that solvent-containing greases require a drying step
Frequently Asked Questions
What are some typical Thermal Grease applications?
Typical Thermal Grease Applications include:
- CPU, GPU and chipsets
- LED assemblies
- Automotive electronics
- IGBT & power units
- Flipchip BGAs
What are the benefits of Thermal grease?
The low viscosity and excellent thixotropy of thermal grease makes it ideal for dispensing and screen printing. Its nature allows for a wide range of bond line thicknesses ranging from 50 down to 7 microns.
It comes in a variety of thermal resistance and thermal conductivity options for different power densities making it highly stable and reliable. Additionally thermal grease is stable and homogeneous at room temperature storage, making it a much more flexible material to work with.
How can I avoid tailing?
Tailing is happening as the stencil lifts at the end of the printing process. If the “tailing” is found only at the end edge, along the screening direction, our focus will be in the clearance between the stencil the substrate. Extra paste in the clearance can cause tailing when lifting the stencil after screening.
- The clearance may be a result of the unevenness at the end of stencil, rather than the substrate. You should change the direction of the stencil by 180o and try again to see if “tailing” position would change.
- The excessive blade pressure on the stencil, especially as the blade moves to the middle of stencil, may warp the stencil and then cause clearance at the end edge. In this situation, decreasing the blade pressure will work.
- Check and make sure the stencil is fixed firmly and will not move during screening;
Also, the stencil must be lifted vertically after the print, any movement can lead to tailing.
Do you offer printing recommendations?
Currently, we don’t have default recommendations on the screening speed, and blade pressure.
If you could share more information , picture or video of you screening process, it will help us to give parameter recommendations.
The information we would like to get is:
- The thickness of stencil
- Τhe opening size of the stencil
- Screening speed
- Blade pressure
Can I get Thermal Grease in a certain color?
Maybe. General rule of thumb is that lower Thermal conductivity greases are more flexible and can accept multiple dyes and pigments. On the other hand, the fillers that we use for higher thermal conductivity allow them only to be gray and dark-ish.
Can I blame the grease for the tailing effect?
If the viscosity of the grease was not suitable, the tailing would occur everywhere, not just on the edge or a certain part of the stencil.
If that\'s the case, we believe the grease is suitable and the tailing can be eliminated by proper parameter adjustment.
Learn More
Thermal Grease Characteristics
Bondline matters
Thermal Grease can achieve the thinnest bondline thickness (BLT) out of all Thermal interface materials with thickness that goes down to 7 microns and at the same time achieves a Thermal impedance of 0.002(℃∙in²/W).
This fluctuates per product but it is a telltale sign of the portfolio properties. Grease has the lowest viscosity of the entire thermal interface product category and can be used to dispense or screen print while also maintaining exquisite thermal conductivity capabilities.
As we mentioned before, we pride ourselves in our testing capabilities and our property precision. Another aspect of testing that we take really seriously is reliability. Thermal Grease products have increased thermal reliability and can perform great in HAST, TCB and baking tests.
Thermal grease products can last up to 1400 hours in 150°C baking test, up to 96 hours in HAST, Highly accelerated temperature and humidity tests and more than 1000 hours in TCB Temperature cycling tests.
Bondline matters
Thermal Grease can achieve the thinnest bondline thickness (BLT) out of all Thermal interface materials with thickness that goes down to 7 microns and at the same time achieves a Thermal impedance of 0.002(℃∙in²/W).
This fluctuates per product but it is a telltale sign of the portfolio properties. Grease has the lowest viscosity of the entire thermal interface product category and can be used to dispense or screen print while also maintaining exquisite thermal conductivity capabilities.
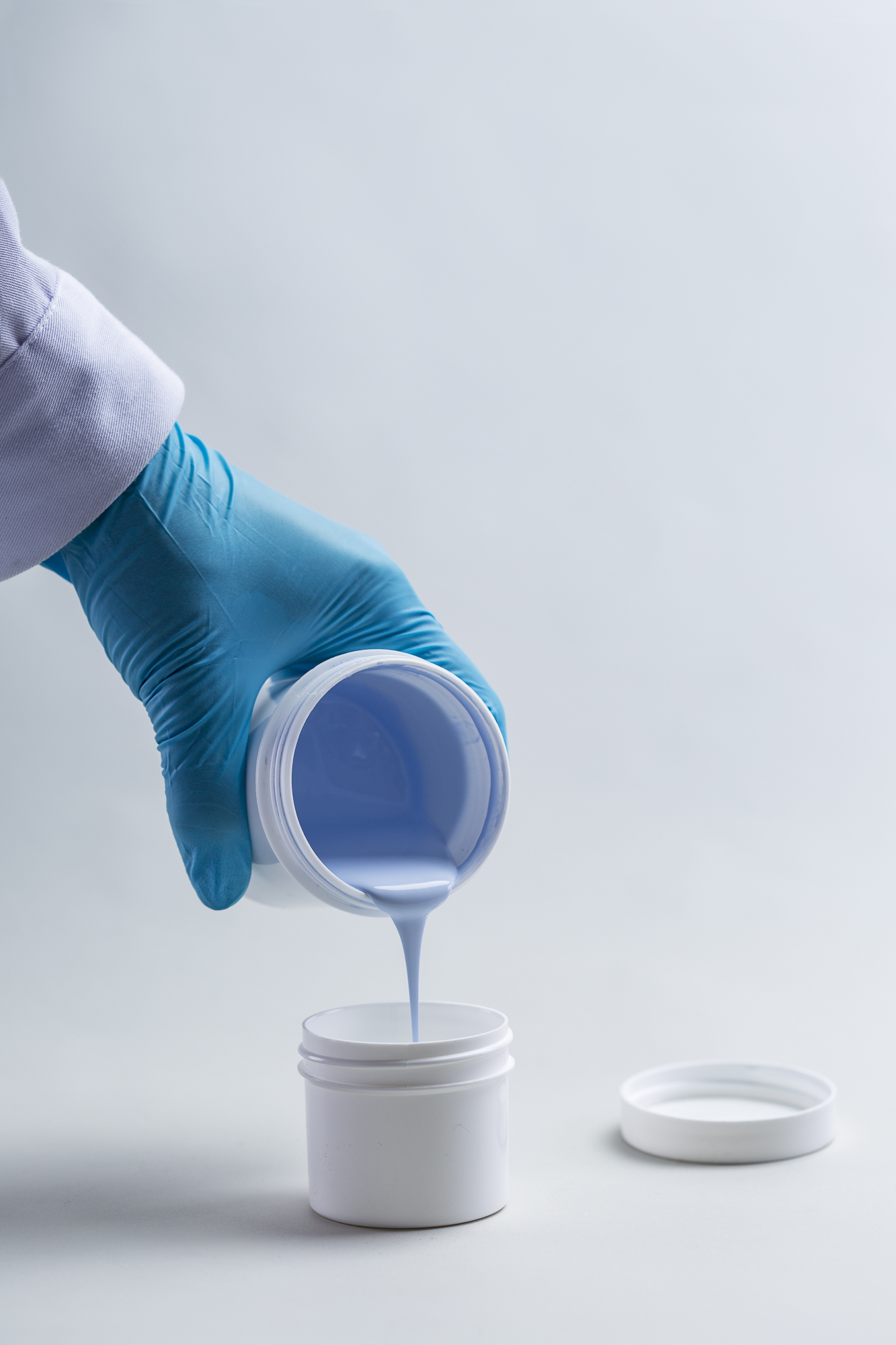