Optoelectronic Epoxy Mold Compounds
Optoelectronic Mold compounds can replace a lot of existing technology in Ambient light sensors, lens filters and proximity sensors. They have a lower cost compared to traditional glass, since standard optical filters can often run into the hundreds of dollars. This is mainly because they require fewer process steps since no adhesive is needed, as the filter is incorporated into the encapsulant. Additionaly, they can have custom cut-off and bandpass with formulations tailored to your wavelength requirements.
White, highly reflective epoxy molding compounds, also abreviated as WMC, are epoxy molding compounds that are filled with a highly reflective filler that stays reflective even after exposure to heat and UV for long periods of time. We offer a range of highly reflective, white, non-yellowing epoxy mold compounds for led packages and lighting applications that require a high-performance non-yellowing compound with high brightness and reflectivity.
Clear epoxy Mold compounds have different filler and chemistry than most common EMCs. Optically clear compounds are also used for LED devices, and to encapsulate optical or optoelectronic devices that require both a high level of light transmittance as well as a good level of mechanical protection. In a similar process to Glob Top encapsulation, a literal glob of clear encapsulant is dropped directly into place on top of the LED. In other production processes, optically clear compounds are used to cast the LED’s final body. Phosphor, colored dyes, and diffusant concentrates can be added to this liquid encapsulant to fine tune it to your needs and alter its optical properties.
OPTOLINQ GT-W170MG | White Epoxy Mold Compound
- High light reflectance and excellent light shielding
- Low yellowing at high temperature
- High MSL performance
- 6 - 8 weeks
OPTOLINQ TMC-3282 | Transparent Mold Compound
- Exceptional moldability with long spiral flow
- Excellent performance at high temperature and high humidity conditions
- Excellent adhesion and low stress
- 8 - 12 weeks
OPTOLINQ TMC-3282SF | Transparent Mold Compound
- Exceptional moldability with long spiral flow
- Excellent performance at high temperature and high humidity conditions
- Excellent adhesion and low stress
- 8 - 12 weeks
OPTOLINQ BMC-4200| Opaque Mold Compound
- Opaque
- Suitable spiral flow for molding conditions
- Superior reliability
- 8 - 12 weeks
OPTOLINQ GT-W170 | White Epoxy Mold Compound
- Reflective compound
- Replaces Kyocera KE-96/95
- Oxidation resistance
- No longer available
OPTOLINQ TMC-2100| Transparent Mold Compound
- Exceptional moldability with long spiral flow
- Low moisture absorption
- Excellent reliability
- 8 - 12 weeks
Hysol GR17 | White Epoxy Mold Compound
- Reflective compound
- For Optocouplers
- High moldability
- 8 - 12 weeks
TMC-9000T | Clear Optical Molding Compound
- Transparent Filler Technology
- Anti-blue Decay
- Low CTE & Low Moisture Absorption
- 8 - 12 weeks
Hysol GR300S | Black Epoxy Mold Compound
- Low CTE (15 ppm/°C)
- Low stress
- High productivity
- 8 - 12 weeks
BMC-7600H-BDF | Black Optical Molding Compound
- High performance
- Fine pitch RGB
- Black with wet method
- In stock
TMC-8020LS | Clear Optical Molding Compound
- LED Encapsulation
- Low stress
- Better reflow and Thermal shock
- 6 - 8 weeks
TMC-8020T | Optically Clear Molding Compound
- LED Encapsulation
- Optically clear
- Emitter and Detector encapsulation
- In stock
TMC-8040 | Optically clear Molding Compound
- High reliability
- 7 segment monochrome LED
- Medium blue ray decay
- In stock
OPTOLINQ TMC-8060 | Clear Optical Molding Compound
- LED Encapsulation
- Outdoor applications
- Low blue ray decay
- In stock
TMC-8090 | Clear Optical Molding Compound
- High reliability backlight LED
- Anti moisture
- Low blue ray decay
- In stock
Hysol GR180R | White Epoxy Mold Compound
- Reflective compound
- High reliability
- Great workability
- No longer available
Hysol GR180T | White Epoxy Mold Compound
- Transmitting compound
- High reliability
- Good workability
- No longer available
Product Selector Guide
Product Name | Key Properties | ||||||||
---|---|---|---|---|---|---|---|---|---|
Color | Specific Gravity | Glass Transition Temperature (Tg), °C | CTE, Alpha 1 ppm/°C | CTE, Alpha 2 ppm/°C | Moisture absorption | Gel time (s) | Refractive index | Spiral flow (cm) | |
BMC-1100 | Black | 2.1 | 150 | 20 | 50 | - | - | - | 70-160 |
BMC-4200 | Black | 1.22 | 115 | 8 | 21 | - | 20-50 | - | 80-240 |
Hysol GR17 | White | 1.75 | 182 | 26 | 66 | 0.46% | 25 | - | 50 |
Hysol GR180R | White | 2.02 | 203 | 15 | 46 | 0.45% | 19 | - | 68 |
Hysol GR180T | Clear | 1.85 | 195 | 26 | 67 | 0.67% | 15 | - | 73 |
Hysol GR300S | Black | 1.9 | 169 | 15 | 52 | 0.35% | - | - | 84 |
TC 7600H BDF | Black | 1.56 | 135 | 50 | 120 | - | 25-45 | 1.56 | 150-250 |
TC 8020LS | White | 1.2 | 95 | 70 | 220 | 0.17 | 20-40 | - | 150-250 |
TC 8020T | Clear | 1.23 | - | 70 | 170 | 0.45% | 20-40 | 1.56 | 150-250 |
TC 8040 | Clear | 1.22 | 135 | 81 | 175 | - | 20-45 | - | 150-250 |
TC 8060 | Clear | 1.3 | 160 | 85 | 180 | - | 20-40 | 1.56 | 150-250 |
TC 8090 | Clear | 1.28 | 140 | 74 | 200 | - | 20-40 | 1.53 | 150-250 |
TMC-2100 | Clear | 1.25 | 120 | 10 | 21 | - | - | - | 80-180 |
TMC-3282 | Clear | 1.24 | 125 | 70 | 185 | - | 35-60 | - | - |
TMC-3282SF | Clear | 1.24 | 165 | 62 | 183 | - | 47.5 | - | 100-240 |
WMC-1100 | White | 2.1 | 150 | 20 | 50 | - | 25-40 | - | 70-160 |
Product Name | Key Properties | ||||||||
---|---|---|---|---|---|---|---|---|---|
Color | Specific Gravity | Glass Transition Temperature (Tg), °C | CTE, Alpha 1 ppm/°C | CTE, Alpha 2 ppm/°C | Moisture absorption | Adhesion to Ag/Cu/ NiPdAu | Refractive index | Tensile Strength (MPa) | |
OG10-1 | Clear | - | 140 | 77 | 162 | - | - | 1.53 | 110 |
OP1000 | Clear | - | 139 | 80 | 161 | 0.48% | 25/5/50 | 1.53 | 110 |
OC10-1 | Clear | - | 142 | 75 | 163 | 0.44% | 41/20/39 | 1.53 | 121 |
OL10-1 | Clear | - | 147 | 70 | 167 | 0.25% | - | 1.52 | 136 |
OP7000 | Clear | 1.28 | 140 | 79 | 160 | 0.45% | 20/20/37 | 1.52 | 110 |
OP70-2 | Black | 1.28 | 137 | 81 | 161 | 0.49% | 46/27/56 | - | 94.5 |
2933-102A | Clear | - | 151 | 41 | 90 | 0.2% | - | - | 107 |
2912-58C | White | - | 132 | 42 | 110 | 0.22% | - | - | 100 |
OL88-8 | Clear | 1.28 | 139 | 80 | 161 | 0.25% | - | 1.51 | - |
Diameter (mm) | Weight | Height | Packing | |||
---|---|---|---|---|---|---|
13 | 0.15 | 1.90 - 3.90 | 0.20 | 12 - 25 | 1.5 | 7-10 kg/box (1kg bags) |
16 | 0.15 | 2.80 - 5.80 | 0.40 | 12 - 25 | 1.5 | 7-10 kg/box (1kg bags) |
35 | 0.40 | 13.5 - 45 | 1.5 | 12 - 41 | 2.5 | 8-10 kg/box (1kg bags) |
Powder | - | - | - | - | - | 5 kg/box (0.5kg bags) |
Please note that all bags are made from Aluminum foil and vacuum sealed to prevent moisture absorption
Frequently Asked Questions
How do the WMC get and stay white?
White epoxy molding compounds are filled with Titanium Dioxide (TiO2), a very white filler that gives the epoxy its very high brightness and reflectivity. Different grades of TiO2 give different degrees of reflectivity.
The choice and grades of resin and hardener base, on the other hand, are responsible for maintaining the WMCs whiteness and hence reflectivity after exposure to heat or UV radiance.
What is the difference between reflectivity and transmittance?
Typically, in LED and other lighting applications, we are looking for high light transmission that endures after heat and UV exposure. Transmission is the amount of light that is allowed to pass through the material.
However, to increase light efficiency and output, we are looking for materials that have a high reflectivity to get as much light as possible out of the device. Reflectivity is the amount of light rebounded off a surface that is neither absorbed nor transmitted.
Learn More
Epoxies vs Silicone for Clear Encapsulation
Molding compounds can act as silicone replacement since they exhibit superior mechanical properties and prevent common silicone issues from occurring. They have rigid, non tacky surfaces that minimize dust collection and do not limit the light output. Their increased adhesion to PPA/PCT guarantees consistent reflectivity and transmissivity.
Silicones on the other hand are more prone to pressure issues where the movement of soft silicone can potentially break the delicate wire bonds or collect dust that reduces the light output for optoelectronic applications. Additionally, silicones are known to delaminate at the PPA/PCT interface and create dark spots that reduce the reflectivity and light output. To add insult to injury, suphur compounds are allowed to evaporate through silicone and potentially corrode the silver pad and as a result destroy the electrical contact.
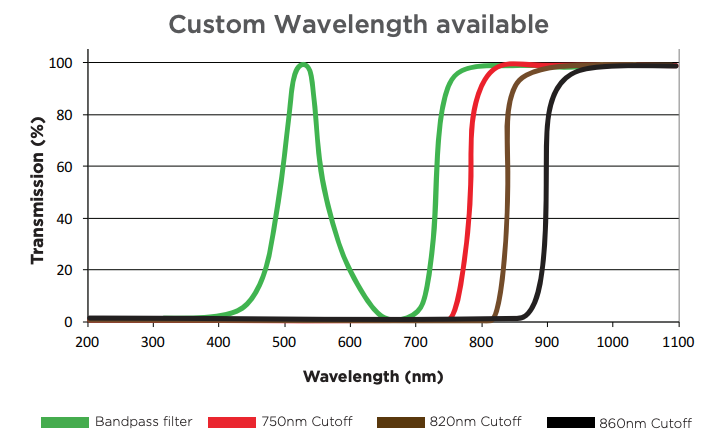
Epoxies are also great alternatives to silicones in regards to their refractive properties. They are cost effective solutions for mid power LED encapsulation that retain a >90% transmittance rate @400-1600nm while also staying clear (non yellow) after thousands of hours at 105°C. Their refractive index is pretty much similar to expensive phenyl silicones so they are more efficient and can accomodate a reduced cost per lumen as well as increased lumens per watt. An overall improvement.
Non yellowing
To stay on the non yellowing matter, the color of the bulb is very important for larger led lamps. It is important not to tell the "old" lamps from the new by their color. That\'s why our epoxies offer minimal transmission loss and minimal yellowing at demanding operating conditions.
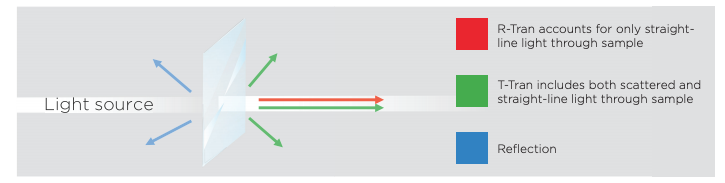
Sensor replacement
Old school glass optical sensors are expensive to manufacture and difficult to miniaturize. Their require an intricate process with multiple steps to create lens filters and sensors for light sensing electronics. Enter clear epoxies which can be used as a low cost glass replacement that is easy to handle and miniaturise while are also able to adjust to your wavelength requirements. Be it for automotive, biometric or consumer applications, our light filter technology allows for precise wavelength cut off values with excellent initial and long term transmittance.
And on the matter of transmittance, we offer low stress epoxies that preserve straight light transmission something extremely uncommon for low stress and high clarity epoxies that are usually compromised by their low stress additives. These low stress clear compounds have very low CTE as well as very low moisture absorption while also maintaining high optical transmittance in the range of 400 - 1600nm.
These compounds retain their R-Tran and consistently exhibit high UV transmittance even after multiple reflow passes. They are uniquely suited for SMT devices that typically require excellent transmission in the ultraviolet range.
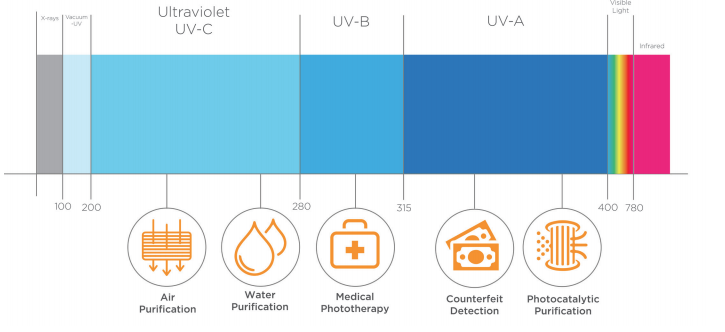
Transmission, absorption and reflection
Clear epoxies require the highest possible initial transmission and need to maintain this high transmission after aging. Mainly used in low power and high wavelength applications, clear molding compounds are widely popular in fields where early transmittance onset, high transmittance and no discolouration are strict requirements.
That\'s why we offer products with the earliest transmittance onset in the UV region (280 nm), the highest transmittance in visible & IR wavelengths that are also non-yellowing after continuous elevated temperature exposure. Products that are used to protects displays against degradation from humidity, dust, and UV exposure and are field-tested for use in outdoor displays
Optically clear epoxies are tailored for use on sensors and opto couplers with a revolutionary customized chemical filter technology that achieves the desired cut-off and bandpass transmission. So , if it wasn\'t "clear" enough yet, clear epoxies need, above all, to be transmissive.
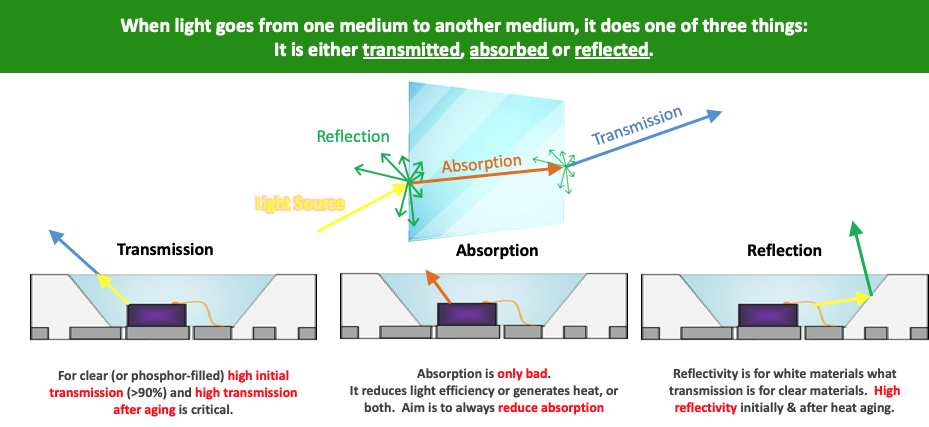
Absorption has no place in the Optoelectronics category. Since it reduces light efficiency and generates heat it can only have a negative impact for any optoelectronic device, making it a value that needs to be reduced as much as possible. Imagine a (non opto graded) Black epoxy. It wont reflect or transmit any light through it. That\'s absorption for you.
Reflectivity on the other hand is highly sought after for housing LED applications. 95% of the time this concerns White epoxy mold compounds that are surrounding the clear compounds. White compounds need to be highly reflective both initially and after ageing and assist into making ideal opto packages.
Combining White and Clear compounds into a package
White colored epoxy mold compounds with low CTE are designed for applications requiring high brightness and reflectivity, and are ideally combined with clear optoelectronic molding compounds with similar CTE resulting in amazingly CTE matched LED packages.
Matched CTEs minimize warpage and the associated failures.
As you can see in the following images it is very important for substrates and materials to be CTE matched. This means that the Coefficient of thermal expansion needs to be similar if not identical. This way when the adhesive/encapsulant/you name it shrinks, the substrate will shrink for the same %. And the same goes for expansion. So in practice you will have two (or more) materials that shrink and expand together and do not cause fractures or structural issues within their bond/package.
A higher CTE material will shrink more during cooling, or expand more during heating.
- This behavior causes warpage in the molded package.
- If adhesion between two materials of mismatched CTE is poor, delamination may occur.
- Even when adhesion is excellent, excessive thermal stress between materials with two different CTEs can lead to cracking or wire breakage.