Bismaleimides (BMI)
Bismaleimides or BMI resins are a class of thermosets that offer significant advantages over other thermoset materials such as epoxies, urethanes, polyester and phenolics. Bismaleimides can be used as additives or base resins in adhesives that are designed for high temperature resistance or even FCCL layered applications. When used as a base resin they can produce adhesives that are tough, flexible and demonstrate good peel strength.
Unlike other suppliers, CAPLINQ offers unique imide-extended BMI or X-BMI's which have polyimides, dianhydrides and diamines as their backbone. Even though they can be used on their own, Bismaleimides are more often blended with reactive co-monomers to produce unique material properties such as very low cure shrinkage, low stress, hydrophobic and very thermally stable thermosets.
Please continue to our Learn More section to learn more about what makes our BMI resins unique and how our imide-extended bismaleimides can allow you to formulate unique high-value formulations.
BMI-689 Low Viscosity Liquid Bismaleimide
- Hydrophobic
- High adhesion to various substrates
- Superior thermal stability
- 1 - 2 weeks
BMI-3000 CG Low Cost Bismaleimide (Imide Extended) in Powder Form
- Superior thermal stability
- High adhesion to various substrates
- Hydrophobic toughener
- 1 - 2 weeks
BMI-1400 Low Viscosity Bismaleimide Oligomer
- Soluble in many reactive diluents
- High adhesion to various substrates
- Superior thermal stability
- 1 - 2 weeks
BMI-1500 Low Molecular Weight Bismaleimide Oligomer
- Soluble in many reactive diluents
- High adhesion to various substrates
- Superior thermal stability
- 1 - 2 weeks
BMI-1700 Amorphous, Low Molecular Weight Bismaleimide Oligomer
- Soluble in many reactive diluents
- High adhesion to various substrates
- Superior thermal stability
- 1 - 2 weeks
BMI-5000 P Imide-extended Bismaleimide Oligomer
- Additive to enhance toughness in thermoset compositions
- Cures to a tough thermoset
- Low cross-link density
- 1 - 2 weeks
BMI-6000 Imide-extended Bismaleimide Oligomer
- Superior thermal stability
- Good dielectric properties
- Toughener
- 1 - 2 weeks
BMI-3000 Gel Bismaleimide (Imide Extended)
- Superior thermal stabilty
- Hydrophobic
- Toughener
- 1 - 2 weeks
BMI-3000 J Bismaleimide (Imide Extended) in Powder Form
- Superior thermal stability
- High adhesion to various substrates
- Hydrophobic toughener
- 1 - 2 weeks
BMI-2500 | Imide extended Bismaleimide powder
- Hydrophobic
- Toughener
- Increased modulus and Tg
- 1 - 2 weeks
BMI-689M Low Viscosity Liquid Bismaleimide
- Hydrophobic
- High adhesion to various substrates
- Superior thermal stability
- 4 - 6 weeks
Product Selector Guide
Product | CAS | Description | Key attributes | Appearance | Viscosity | Applications |
---|---|---|---|---|---|---|
BMI-689 | 682800-79-9 | A unique very low viscosity BMI resin |
| Yellow to Amber Liquid | 1,500 ± 500 (25°C) |
|
BMI-689M | 1911605-95-2 | A unique low viscosity liquid BMI resin |
| Dark Amber | 5,000 ± 2000 |
|
BMI-689C | - | A pre-catalyzed unique low viscosity liquid BMI resin |
| Yellow to brown Liquid | 1,500 ± 500 |
|
BMI-1400 | 1224691-98-8 | An amorphous, low molecular weight bismaleimide oligomer that exhibits good adhesion to a variety of substrates |
| Amber | 6,500 ± 1,000 (60°C) |
|
BMI-1500 | 1290041-56-3 | An amorphous, low molecular weight bismaleimide oligomer that exhibits good adhesion to a variety of substrates |
| Amber Viscous liquid | 20,000 ± 10,000 (60°C) |
|
BMI-1700 | 1224691-98-8 | An amorphous, low molecular weight bismaleimide oligomer that exhibits good adhesion to a variety of substrates |
| Amber High Viscous Liquid | 30,000 ± 10,000 (60°C) |
|
BMI-5000 Powder | 921213-77-6 | Imide-extended bismaleimide oligomer that exhibits excellent toughness in the cured state with intermediate cross-link density. |
| Light Yellow Powder | N/A |
|
BMI-6000 | - | A curable, low DK and Df alternative to replace both the Kapton and adhesive layers in the manufacture of FCCL materials. It can be processed in a resin system as a solid or dissolved in a solvent. |
| Light Yellow Powder | N/A |
|
Frequently Asked Questions
Are there new products under development?
We are developing a couple of R&D resins with some unique properties:
- FM46-100 is provided in a solvent solution (anisole) - after drying and "curing" it is a thermoplastic-appearing material with great elongation and the unique feature of returning to its original shape
- The second (unclassified) material has the unique feature that after being formed into a film and deformed (folded, rolled up, etc.), it will hold that shape until warmed where it will then return to its original shape.
Can I use BMI with Acrylates?
Absolutely. Acrylates and methacrylates are regularly used in combination with Bismaleimides to modify die attach properties.
Acrylates are preferred because of their rapid curing, high Glass transition temperature, good adhesion,variable viscosities and variable functional group contents (1,2,3... acrylate groups per molecule). Of course nothing comes without drawbacks that can appear as potential brittleness and reduced moisture and temperature resistance.
What mix ratio do I use when mixing BMI with epoxy resin or acrylic?
The good news and the bad news is that there is no easy answer. In our experience we have encountered very few compatibility issues so virtually all BMI/acrylate or BMI/epoxy ratios are available to the formulators - it\'s just a matter of what they want for the final properties of the adhesive. Successful formulations have been created using 9:1 ratios of BMI as well as 1:6 ratios.
The BMI strong points (low modulus, good temperature resistance, hydrophobicity and good dielectric properties) lend themselves to the adhesive when blended with epoxies or acrylates since they share a cure chemistry. Therefore you can make adhesives with less stress, better moisture and temperature resistance but not totally lose the good aspects of an epoxy or acrylic chemistry.
How do I cure BMI systems?
BMI resins cure free radically - whether thermally by the use of an organic peroxide catalyst or even by UV if using a free radical generating photoinitiator. DMI's preferred thermal catalyst is dicumyl peroxide (CAS # 80-43-3). We recommend using ~2% by weight of the resin content of the formulation and then curing at ~175ºC for an hour.
Of course, these values are just starting recommendations and your application and formulation may require other settings. There are a number organic peroxides that work well to thermally cure the BMI and BMI/acrylate resins.
test?
BMI resins cure free radically - whether thermally by the use of an organic peroxide catalyst or even by UV if using a free radical generating photoinitiator. DMI's preferred thermal catalyst is dicumyl peroxide (CAS # 80-43-3). We recommend using ~2% by weight of the resin content of the formulation and then curing at ~175ºC for an hour.
Of course, these values are just starting recommendations and your application and formulation may require other settings. There are a number organic peroxides that work well to thermally cure the BMI and BMI/acrylate resins.
Learn More
Comparison between BMI based die attach and Epoxy based die attach
BMI | Epoxy | BMI/Epoxy | |
Modulus | ●○○○○ | ●●●○○ | ●●○○○ |
Moisture absorption | ●○○○○ | ●●●○○ | ●●○○○ |
Thermal stability | ●●●●○ | ●●○○○ | ●●●○○ |
JEDEC level 1 / 260 °C | Yes | No | Yes |
Adhesion to substrate | ●●●○○ | ●●●●● | ●●●●○ |
100% solids | Yes | No | Yes |
Snapcure option | Yes | No | No |
Material cost | ●●●○○ | ●○○○○ | ●●○○○ |
Amorphous and liquid imide extended oligomers
BMI Curing Methods
DMI aliphatic BMI resins (689, 3000, 1500, 1400, 1700, 2500) can be cured in a number of ways:
1. Thermal Cure. The most preferred method that gives the most complete cure uses thermal free radical generating catalysts. These catalysts are mainly peroxides that decompose at given temperatures to initiate the polymerization. There are a number of available catalysts but our all-time favorite is Dicumyl Peroxide (DCP). When using about 2 wt% of the resin this material will cause the BMIs to start curing at about 140ºC, peak at about 155ºC. We suggest curing at 175ºC for an hour to insure a thorough cure. You can cure hotter/faster or slower/longer - it is important to experiment to determine the best setting for their application. Another favorite peroxide catalyst is Perkadox 16. This is a low temperature catalyst that starts to cure the resin below 100ºC. This is good for rapid curing adhesives (like die attach paste). The down side is the catalyzed material must be frozen, shipped in dry ice and the pot life will be much shorter than that of a DCP catalyzed system.
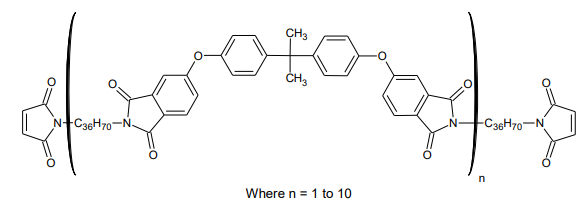

2. UV Cure. The BMI products cure via free radical initiated polymerization. One may use a photoinititator (UV catalyst) to prompt curing of these materials. Our favorite is Irgacure IR 819. This catalyst provides the free radical groups necessary to polymerize the resins upon exposure to 500 - 1,000 mJ/cm2 i-line (365 nm) UV radiation. This is beneficial as it occurs at room temperature and keeps the stress levels low. (Many) Other UV catalysts can also be used.
3. Homocure. You can cure the BMI-689 and BMI-1400 simply by heating them above 220ºC for an hour or two and they will self cure (homocure). This is the least preferred method of curing because 1) it\'s really, really hot and few applications can tolerate the heat and 2) it provides a less thorough cure than other methods.
BMI recommended storage conditions and shelf life
We recommend storage of our liquid BMI resins at 5ºC or colder and away from sunlight (UV sources). For the solid resins we suggest room temperature storage and away from light. DMI warrants the performance of the materials (shelf life) for 1 year from the date of shipment of the products (not the date of manufacture) if stored per recommendations. This insures a guaranteed full year of use of the materials after receipt.
