Flat Gaskets
Flat gaskets are essential static sealing elements designed to prevent the exchange of materials between two stationary, flat contact surfaces, effectively blocking any potential leakage. These gaskets provide a complete physical barrier against fluids, ensuring the integrity of connected components. Flat gaskets find applications across different industries, such as chemical processing, food and beverage production, and pharmaceuticals. The demanding environments of these industries require gaskets that can endure aggressive media, high temperatures, and pressures, operating efficiently within a temperature range of –200 °C to +550 °C.
Selecting the appropriate material for flat gaskets is crucial, taking into account the specific medium, its concentration, the temperature, and the surfaces involved. By meeting these stringent requirements, flat gaskets ensure reliable performance and durability in diverse industrial applications, making them indispensable in maintaining safety and efficiency in complex processes.
LINQSEAL GS-EPDM
- Low cost sealing solution
- High hear resistance and tensile strength
- High water (steam) resistance
- 6 - 8 weeks
LINQSEAL GS-FKM
- Retains elasticity at high temperature
- Highest fluid resistance among commercial rubbers
- Outstanding resistance to heat, oxidation, and weathering
- 6 - 8 weeks
LINQSEAL GS-PTFE
- Outstanding chemical resistance
- Wide temperature stability (–180 °C to 260 °C)
- Excellent thermal and electrical resistance
- 6 - 8 weeks
LINQSEAL GS-VMQ
- High flexibility
- Wide temperature stability (–50 °C to 210 °C)
- Good ozone and weather resistance
- 6 - 8 weeks
Product Selector Guide
Flat Gasket Chemistry | Density [g/cm3] | Elongation at Break [%] | Tensile Strength [MPa] | Hardness [Shore A] | Operating Temperature [°C] |
EPDM | 1.45–1.50 | 200 | 2.5 | 80 | –57 to 150 |
FKM | 1.90–2.00 | 250 | – | 75 | –50 to 260 |
PTFE | 2.10–2.30 | 150 | 21–28 | – | –180 to 260 |
VMQ | 1.25–1.30 | 350 | 6 | 65–75 | –50 to 210 |
Frequently Asked Questions
Frequently Asked Questions about Flat Gaskets
What is the difference between a seal and a gasket?
A gasket is a specific type of seal designed to create a tight seal between two surfaces, preventing fluid or gas leakage. While all gaskets are seals, not all seals are gaskets. For instance, a plug acts as a seal but is not a gasket. The key distinction is that "seal" is a broad category encompassing various products, with gaskets being a subset specifically for sealing stationary, flat surfaces. Understanding this difference is essential for selecting the right sealing solution, ensuring optimal performance and reliability in various applications.
What materials are commonly used for flat gaskets?
Flat gaskets are made from various materials categorized into metallic, non-metallic, and semi-metallic types. For flat gaskets, the focus is on soft material seals, including rubber, rubber cork, fiber, PTFE, and graphite. Rubber and rubber cork provide flexibility and resilience, fiber materials offer excellent sealing under moderate conditions, PTFE is known for its chemical resistance, and graphite excels in high-temperature applications. The choice of material depends on the media, pressure, and temperature requirements.
Where are flat gaskets commonly used?
Flat gaskets are widely used across diverse industries, including chemical, food, and pharmaceuticals, as well as pipeline construction and apparatus engineering. They serve as flange gaskets between connected pipes and are integral components in fittings, pumps, and valves. Common household applications include plumbing, automotive engines, and electrical enclosures. In advanced technologies, flat gaskets play a vital role in hydrogen production through electrolysis and in manufacturing hydrogen fuel cells.
How to determine the correct gasket thickness?
Determining the right flat gasket thickness is critical for optimal sealing performance. Thicker gaskets generally have lower pressure-temperature ratings, suitable for low-pressure applications and rough surfaces. Conversely, thinner gaskets, like non-asbestos, semi-metallic, and metallic types, provide tight seals for high-pressure situations. Surface conditions, including irregularities like damage and warping, must be considered when selecting gasket thickness. Consulting pressure-temperature charts is essential for material selection. For customized solutions, CAPLINQ offers flat gaskets made to measure, available in various contours and dimensions to meet specific needs.
Learn More
Gaskets in Electrochemical Devices
Gaskets are indispensable parts of fuel cells, electrolysers, and flow batteries, often underestimated during the design process. Despite their small size, they fulfill a crucial role. Functioning as seals, gaskets create a barrier between various components, such as bipolar plates and separators. These meticulously crafted barriers ensure that gases, water, and cell components remain securely contained and separated as required. In water electrolyzers, gaskets ensure that hydrogen and oxygen are properly isolated during the process of splitting water into its components. Similarly, in fuel cells, they maintain the integrity of the system while converting fuel into electricity, preventing any leakage or mixing of substances. Gaskets may not receive much attention, but they are essential for the efficient and reliable operation of these electrochemical devices.
Gaskets also play a crucial role in accommodating the expansion of components within a fuel cell or electrolyzer stack. As these devices operate, various components, such as bipolar plates and membranes, may undergo thermal expansion or contraction due to changes in temperature and pressure. The gaskets provide a flexible yet secure seal that allows for this expansion without compromising the integrity of the stack. By accommodating these movements, gaskets help maintain the tight seals necessary to prevent gas leakage and ensure the efficient operation of the electrochemical device.
Gaskets Water Electrolyzer and Fuel Cell Stacks
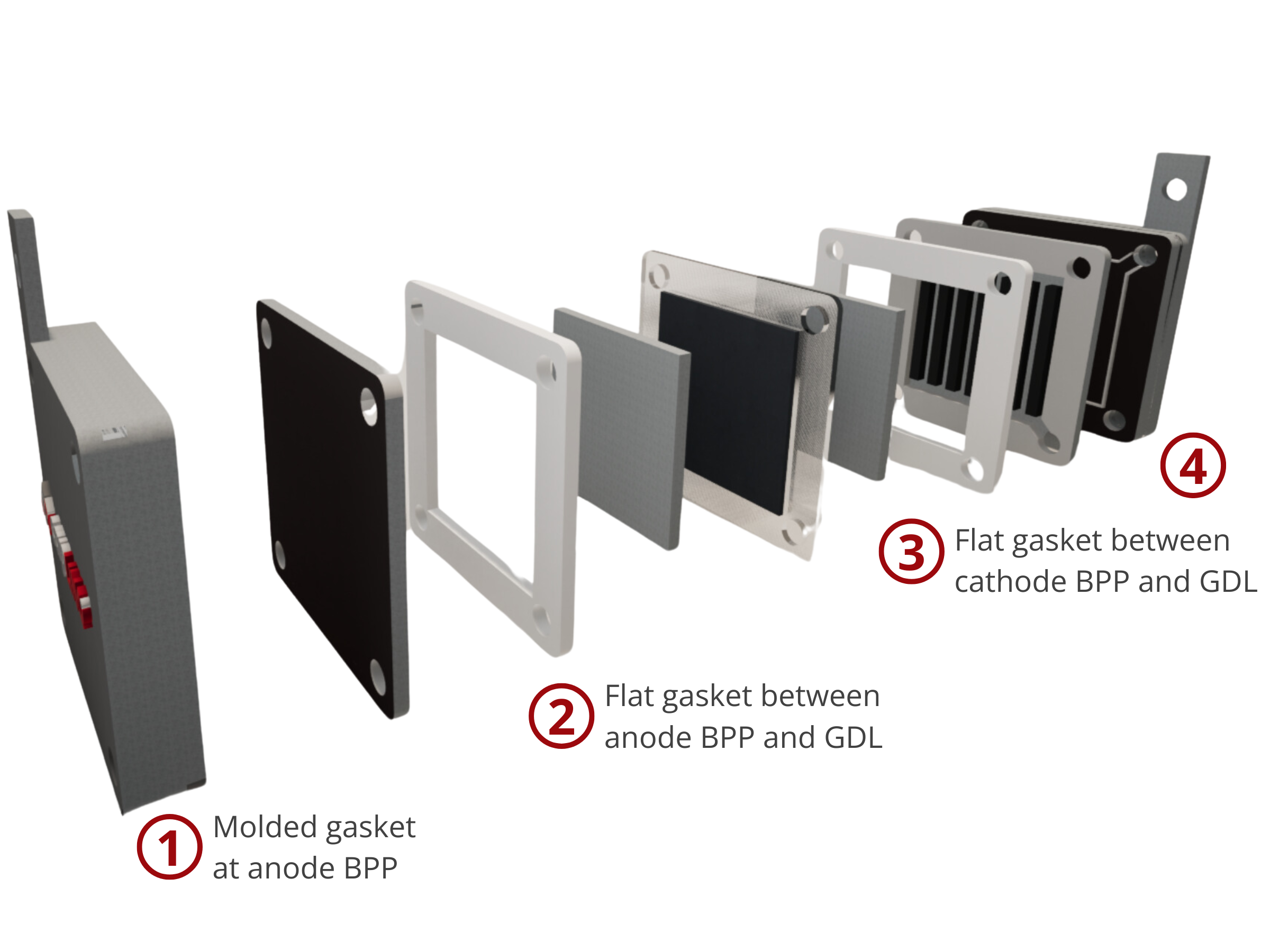
In water electrolyzers, gaskets are similarly essential. They seal the interface between the bipolar plates and the separator, ensuring that the hydrogen and oxygen gasses produced during electrolysis remain contained within their respective compartments, thus maintaining efficiency. Gaskets also play a role in sealing individual stacks, preventing cross-contamination between adjacent cells. Overall, in both fuel cells and water electrolyzers, gaskets are vital for maintaining compartmental integrity and preventing gas leakage or mixing, contributing to the efficient operation of these electrochemical devices.
Gaskets aid in Reducing Thermal Expansion and Deflection of Components within the Stack
In a fuel cell or electrolyzer stack, pressure differences occur from the tightly compressed clamp points towards the center, where pressure gradually decreases. This variation can cause components to deflect or bend, potentially compromising the stack's integrity and leading to gas leakage. Gaskets play a crucial role in managing these pressure differences by providing a flexible yet durable seal between the components, distributing pressure evenly across the stack and minimizing the risk of deformation or damage. Additionally, they act as a barrier to prevent gas leakage, ensuring proper gas flow through the stack.
Gaskets accommodate the expansion of components within the stack, such as bipolar plates and membranes, which may undergo thermal expansion or contraction during operation due to changes in temperature and pressure. The flexible yet secure seal provided by the gaskets allows for this expansion without compromising the stack's integrity. By effectively sealing the stack and accommodating pressure differences and component expansion, gaskets contribute to the overall stability and performance of the fuel cell or electrolyzer, ensuring efficient operation and prolonging the device's lifespan.
Most Common Materials Used as Gaskets for Electrochemical Devices
The most common materials used for gaskets in electrochemical devices like fuel cells and water electrolyzers include silicone rubber, fluoropolymer, and various types of elastomers. These materials are chosen for their compatibility with the electrolytes and gases involved, as well as their resilience to the operating conditions of the devices.
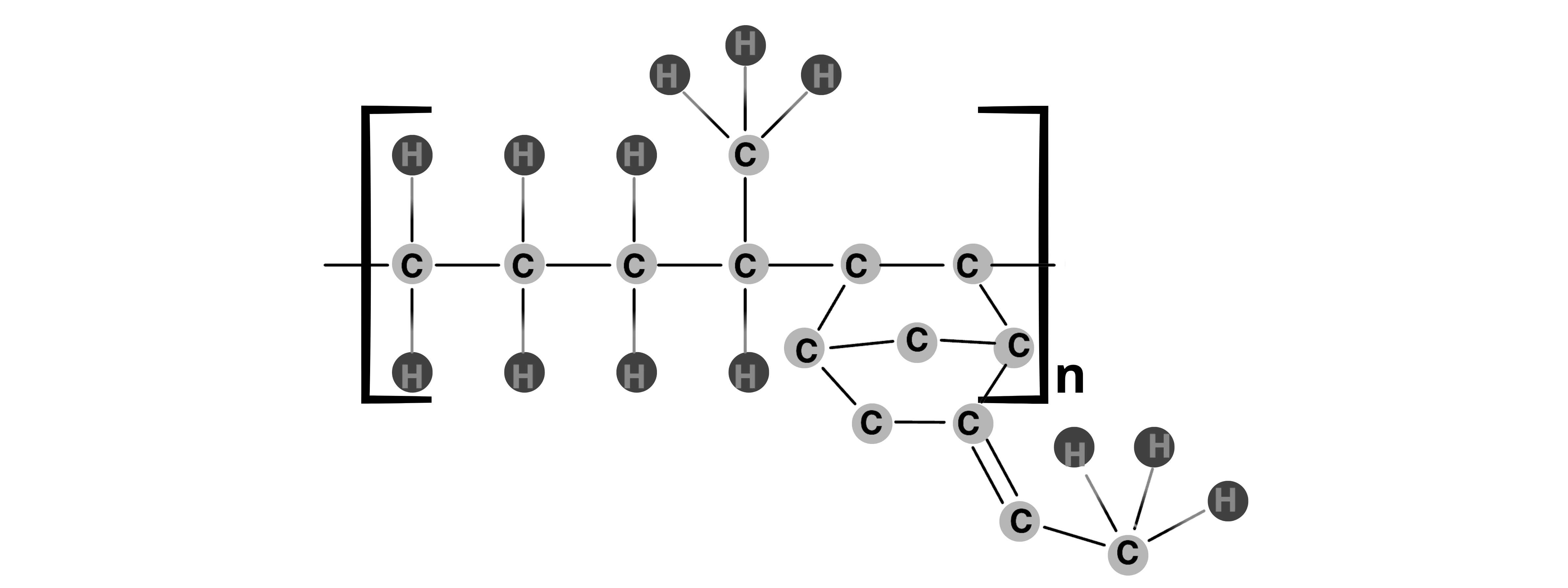
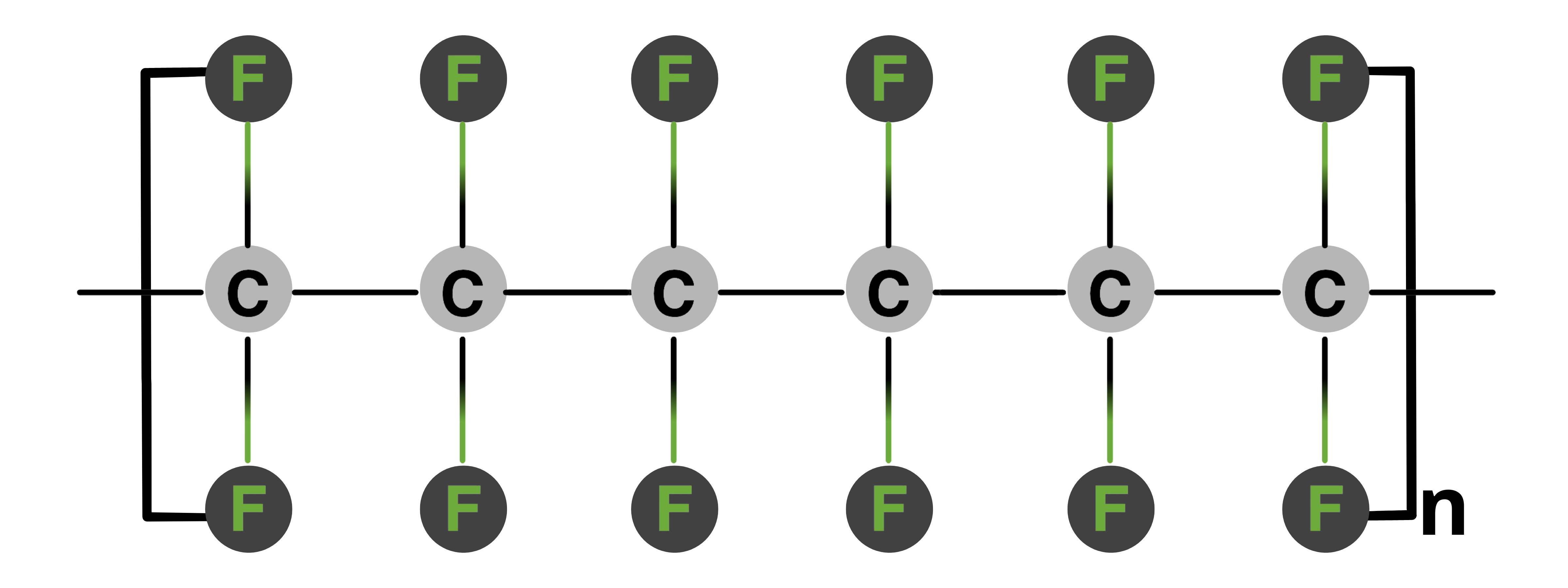
Polytetrafluoroethylene (PTFE)
PTFE is ideal for gaskets in water electrolyzers and fuel cells due to its unique properties. Made from repeating tetrafluoroethylene units, PTFE offers exceptional chemical resistance, high temperature stability (– 200 °C to 260 °C), and non-reactivity. Its low friction, flexibility, and durability ensure effective sealing and long service life, maintaining purity and smooth operation in demanding environments.
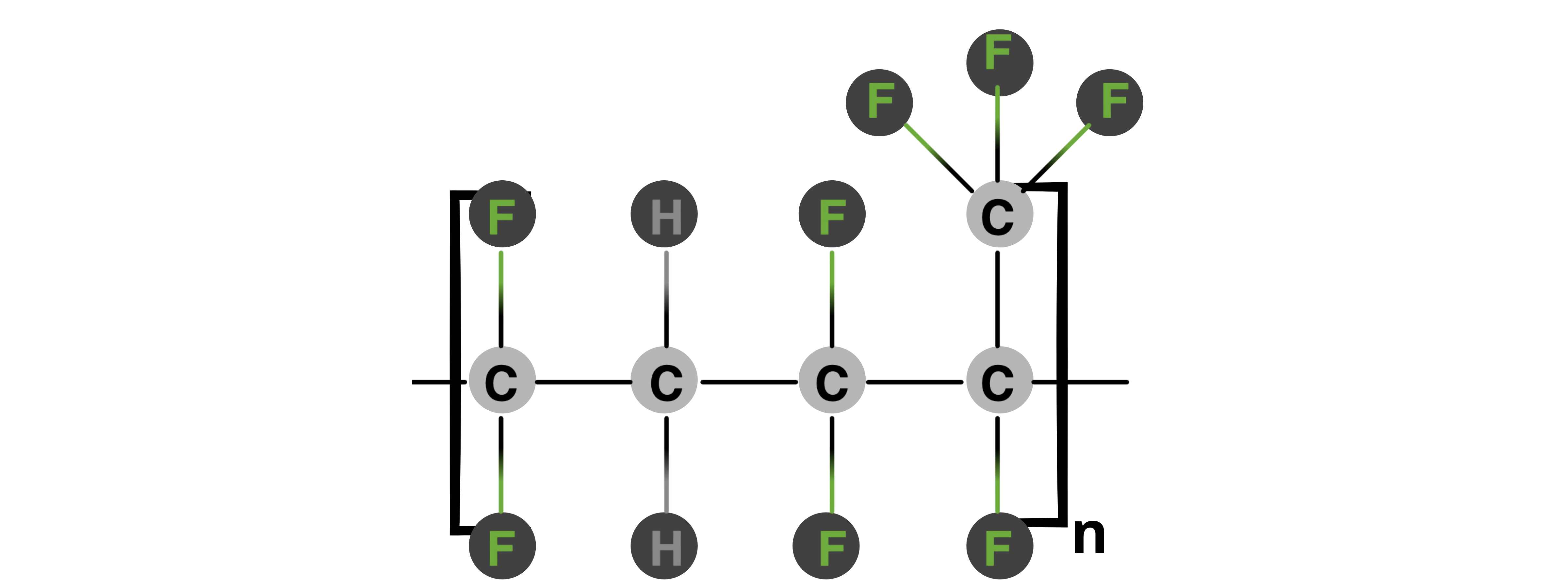
Fluorine Kautschuk Material (FKM)
FKM, or fluorinated rubber material, is excellent for gaskets in water electrolyzers and fuel cells due to their chemical resistance and high temperature stability (–20 °C to 250 °C). Made from fluorinated hydrocarbon polymers, FKM resists acids, bases, fuels, and solvents, ensuring reliability in demanding environments. Their flexibility and compression set resistance provide effective sealing under varying pressures and temperatures.
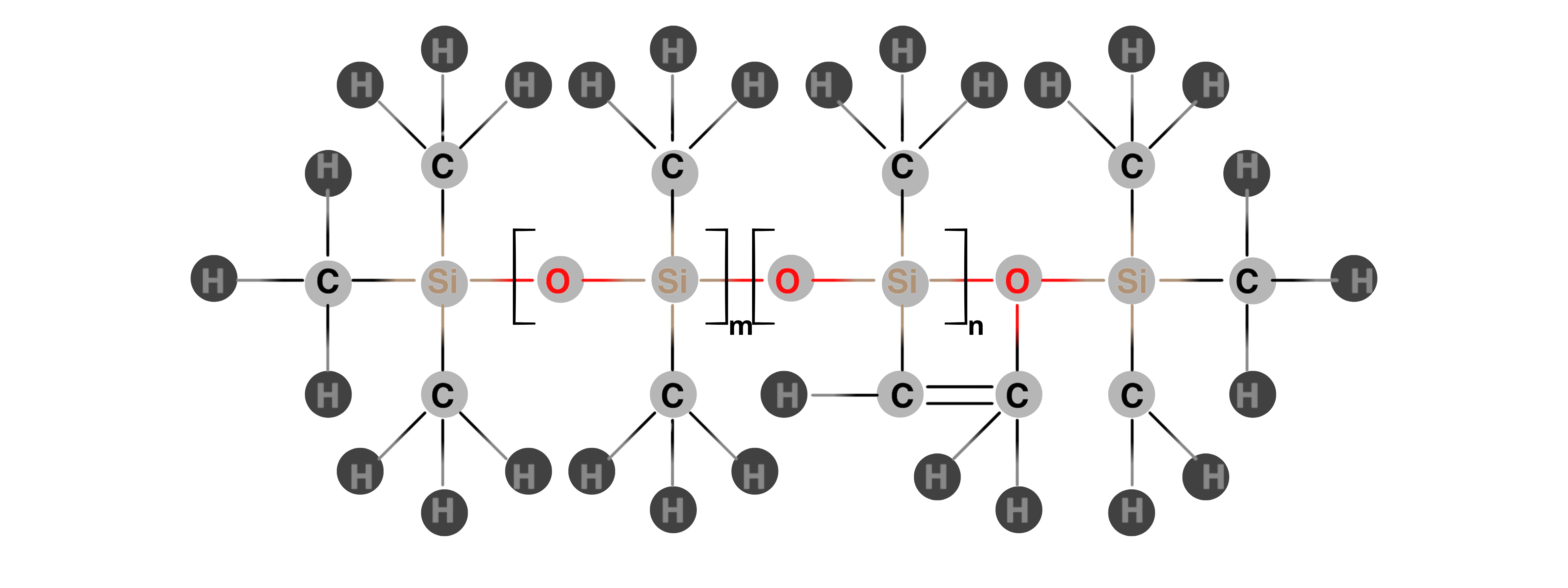
Viny Methyl Silicone (VMQ) Rubber
VMQ, a synthetic polymer made from silicon, oxygen, carbon, and hydrogen, offers superior flexibility, temperature resistance (–50° C to 230 °C), and sealing performance. Silicone rubber resists water, chemicals, and extreme temperatures, and its low compression set ensures long-term reliability. Additionally, it is compatible with a wide range of materials, preventing contamination and ensuring seamless integration in various applications.
Property comparison for materials used as gaskets for electrochemical devices
Property | EPDM | FKM | PTFE | VMQ |
Chemical Resistance | ■■■□ Good | ■■■■ High | ■■■■ High | ■■■□ Good |
High-Temperature Resistance | ■■■□ Good | ■■■■ High | ■■■■ High | ■■■■ High |
Compression Set Resistance | ■■■□ Good | ■■■■ High | ■■■■ High | ■■■■ High |
Flexibility | ■■■■ High | ■■■□ Good | ■■■■ High | ■■■■ High |
Stability | ■■□□ Moderate | ■■■■ High | ■■■■ High | ■■■■ High |
Cost | ■■■□ Cheap | ■□□□ Expensive | ■□□□ Expensive | ■■□□ Moderate |
Property Requirements for Gaskets in Water Electrolyzers and Fuel Cells
For gaskets used in water electrolyzers and fuel cells, several property requirements need to be considered:
- Thickness. The thickness of the gasket is important as it affects the compression and sealing ability. Thickness affects how much the flow fields press into the electrodes. It should be chosen based on the specific requirements of the application, ensuring proper sealing without excessive compression that could lead to damage or leakage.
- Very Good Leakage Performance. Gasket materials should offer excellent sealing to minimize leakage and maintain high electrolyzer efficiency.
- Chemical Resistance. Gaskets must resist degradation from the electrolytes, fuels, and other chemicals present in the system to maintain their integrity and sealing performance.
- Good Mechanical Properties. Gaskets should have low creep and defined setting behavior to prevent deformation during operation, ensuring stability and reliability.
- Temperature Stability. Gaskets should maintain their sealing properties over a wide range of temperatures, as these systems can operate at both high and low temperatures.
- Electrical Insulation. Gaskets need to provide electrical insulation when used within the stack to prevent short circuits and ensure safe operation.
- Long Service Life. Materials should have a long service life to minimize maintenance needs and ensure the continuous operation of electrolyzers with minimal downtime.