Wire Meshes
Wire meshes are fundamental components in the realm of electrochemical processes, offering a versatile array of applications. These finely woven grids, renowned for their ability to adapt to specific electrochemical needs, play a crucial role in ensuring the success of various processes.
Stainless steel wire meshes combine corrosion resistance with budget-conscious sensibility, they provide a dependable solution suitable for a diverse array of applications. The adaptability of stainless steel meshes extends their utility to different electrolytes, guaranteeing reliable performance across the board.
Titanium wire meshes are primarily preferred for their resilience. With their exceptional corrosion resistance, these meshes find their strength in challenging environments. The versatility of titanium meshes accommodates a broad range of electrolytes, assuring durable, consistent performance.
Nickel wire meshes take center stage as cost-effective, dependable components, often favored in alkaline electrolyzers. They provide a practical solution that meets electrochemical demands without significant financial investment. Whether you're looking to optimize efficiency, ensure durability, or address budget constraints, our wire mesh products are thoughtfully engineered to align with your specific electrochemical material requirements.
LINQCELL NWM 300 | 0.3mm Nickel Wire Mesh
- 0.30 mm wire diameter
- Excellent chemical stability and anti-corrosion resistance
- High electrical conductivity
- 8 - 12 weeks
LINQCELL NWM 250 | 0.25mm Nickel Wire Mesh
- 0.25 mm wire diameter
- Excellent chemical stability and anti-corrosion resistance
- High electrical conductivity
- 8 - 12 weeks
LINQCELL CAT-NiAl
- Low overpotential for hydrogen evolution reaction
- Platinum-group metal (PGM)-free catalyst
- Optimized as cathode for alkaline water electrolyzers
- 8 - 12 weeks
LINQCELL ANO-NiAl
- Low overpotential for oxygen evolution reaction
- Platinum-group metal (PGM)-free catalyst
- Optimized as anode for alkaline water electrolyzers
- 6 - 8 weeks
LINQCELL CAT-NiMoAl
- Low overpotential for hydrogen evolution reaction
- Platinum-group metal (PGM)-free catalyst
- Optimized as cathode for alkaline water electrolyzers
- 8 - 12 weeks
Product Selector Guide
Nickel Wire Meshes
Product | Nickel | Iron | Silicon | Copper | Sulfer | Manganese |
NWM-250 | >99 | <0.4 | <0.35 | <0.25 | <0.01 | <0.35 |
NWM-300 | >99 | <0.4 | <0.35 | <0.25 | <0.01 | <0.35 |
Nickel-based Electrodes
Product | |Current| at –1.5 V | Mechanical Stability (Weight loss ) | Performance Decay |
Cathodes | |||
CAT-NiAl | >1 A | <1% | <2% |
CAT-NiMoAl | > 1.2 A | <1% | <2% |
Anodes | |||
ANO-NiAl | — | <1% | <2% |
Frequently Asked Questions
Frequently Asked Questions About Wire Meshes
How are wire meshes used in electrochemical processes?
Wire meshes play a crucial role in electrochemical applications by serving as key components in various types of electrolyzers. They are used as electrodes to facilitate the efficient separation and production of gases, such as hydrogen and oxygen. These electrodes provide the surface area and conductivity necessary for electrolysis reactions.
What materials are commonly used for wire meshes in electrochemical systems?
Wire meshes are typically constructed from materials like stainless steel, titanium, nickel, and precious metal-coated variants. These materials are chosen based on their properties and compatibility with specific electrolytes. Stainless steel, for example, is valued for its balance of corrosion resistance and cost-effectiveness.
What are the advantages of using wire mesh electrodes in electrolyzers?
Wire mesh electrodes offer excellent electrical conductivity and a well-defined surface, enabling efficient electrocatalysis. They are also known for their durability, corrosion resistance, and suitability for various types of electrolytes. These characteristics make them essential for applications like water electrolysis and electrochemical gas production.
In which electrochemical applications are wire meshes predominantly used?
Wire meshes are commonly employed in various electrochemical processes, such as alkaline electrolyzers and proton exchange membrane (PEM) electrolyzers, to facilitate the efficient conversion of water into hydrogen and oxygen gases. These applications are integral to hydrogen production and other clean energy technologies.
How do I choose the right wire mesh for my electrochemical project?
The choice of wire mesh depends on factors like the type of electrolyzer, the specific electrolyte, operating conditions, and budget constraints. Titanium is favored for its corrosion resistance, while nickel offers a cost-effective solution in alkaline electrolyzers, for example. It's essential to select the material that aligns with your project's requirements and objectives.
What maintenance is required for wire mesh electrodes in electrochemical systems?
Maintenance typically involves regular cleaning and inspection to ensure the wire mesh remains free from contaminants that might hinder its performance. Corrosion-resistant materials like titanium may require less frequent maintenance. Proper maintenance practices ensure the longevity and effectiveness of wire mesh electrodes in electrochemical systems.
Learn More
Nickel Mesh for Electrochemical Applications
Nickel wire mesh plays a vital role in various electrochemical applications. The most commonly used types, Nickel 200 and Nickel 201, are renowned for their exceptional corrosion resistance and versatility. Let's delve into their key characteristics and applications:
Characteristics | Nickel 200 and Nickel 201 |
---|---|
Composition | Pure nickel content, 99.6% or higher |
Corrosion Resistance | Excellent, making them ideal for challenging environments |
Applications | Widely used as electrodes in diverse electrolyzers, including alkaline systems |
Advantages | Highly cost-effective, efficient, and reliable choice for clean energy technologies |
Notable Features | High purity, exceptional resistance to corrosive conditions |
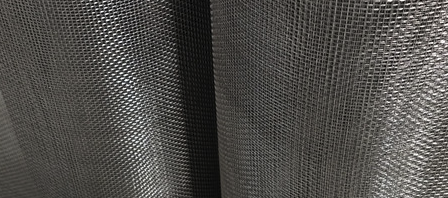
Applications of Nickel Mesh:
Electrolysis Cells: Nickel wire mesh serves as crucial electrodes in various electrolyzers, facilitating the production of hydrogen and oxygen gases.
Alkaline Electrolysis: It's a preferred material in alkaline electrolyzers for hydrogen generation, offering both cost-effectiveness and efficiency.
Stainless steel Wire mesh
Stainless steel wire mesh, particularly grade 316 (SS316), is a highly regarded material in electrochemical applications. It boasts remarkable corrosion resistance, making it an excellent choice for challenging and corrosive environments typically encountered in electrochemical processes. SS316's inclusion of molybdenum further enhances its resilience against chloride-containing solutions, rendering it ideal for applications where corrosion resistance is of paramount importance. Additionally, the material offers robust mechanical properties and widespread availability, solidifying its status as a preferred option in a diverse array of electrochemical applications.
Key Characteristics | Stainless Steel Type 316 (SS316) |
---|---|
Corrosion Resistance | Excellent, ideal for aggressive environments |
Molybdenum Inclusion | Enhances resistance to chloride-containing solutions |
Mechanical Properties | Maintains good mechanical strength |
Versatility | Suitable for a wide range of electrochemical applications |
Applications of Stainless Steel Wire Mesh:
Electrolysis Cells: Indispensable in water electrolysis, facilitating hydrogen and oxygen production.
Chlor-Alkali Production: Used in cells for chlorine, sodium hydroxide, and hydrogen production, enduring harsh chemical conditions.
Electrochemical Sensors: A preferred choice for sensor construction, offering durability and resistance.
Electrochemical Machining: Serves as tool electrodes for precision material removal.
Corrosion Testing: A standard material for assessing corrosion resistance in various environments.
Electroplating: Employed as anodes and cathodes in electroplating, known for extended service life.
Water Treatment: Actively involved in wastewater treatment systems, assisting in pollutant removal.
Hydrogen Production: Pivotal in water electrolysis for hydrogen gas generation, an essential component in clean energy technologies.
Fuel Cells: Reliable choice for specific fuel cell components due to its corrosion resistance qualities.
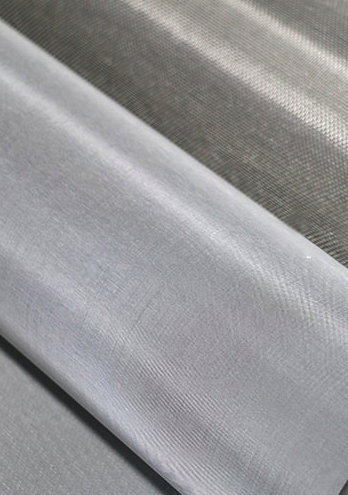
What are the main differences between Mesh and Felt?
In the realm of electrochemical applications, the choice between wire mesh and felt products hinges on specific performance requirements. Wire mesh, characterized by a grid-like structure of interwoven metal wires, offers distinct advantages. Its key differentiators include superior electrical conductivity, which enables efficient charge transfer, and the option for catalytic coatings that enhance electrochemical reactions. However, wire mesh's planar surface area is relatively limited, affecting its ability to accommodate high gas diffusion rates.
In contrast, felt products, composed of non-woven and compressed fibers, provide a high, porous, and three-dimensional surface area. This porous structure promotes enhanced gas diffusion, making felt an optimal choice for gas diffusion layers in fuel cells. Nevertheless, felt materials often lag behind wire mesh in terms of electrical conductivity, which is crucial for certain electrochemical processes. Therefore, the selection between wire mesh and felt significantly relies on the specific requirements of the application, balancing factors like electrical conductivity, surface area, and catalytic properties.
At the end of the day, the choice extends to the materials used. Wire meshes are commonly constructed from materials like stainless steel, titanium, and nickel, each offering varying levels of corrosion resistance and compatibility with different electrolytes. Stainless steel, specifically SS316, is a popular choice for its balance of corrosion resistance and cost-efficiency, while titanium wire meshes excel in aggressive and challenging environments due to their exceptional resistance. Nickel wire meshes are preferred in alkaline electrolyzers for their cost-effectiveness, making them a practical solution that aligns with electrochemical demands while addressing budget constraints.
On the other hand, felt products usually consist of materials like carbon, providing ample surface area for improved gas diffusion. The choice between wire mesh and felt is inherently linked to the application's unique demands and the materials that best suit the electrochemical environment's challenges.
Characteristic | Wire Mesh | Felt |
Structure | Grid-like, interwoven metal wires | Non-woven, compressed fibers |
Surface Area | Limited, flat, planar surface | High, porous, three-dimensional |
Electrical Conductivity | Excellent | Limited, less conductive |
Catalytic Properties | Can be coated for catalysis | Coating may be less effective |
Corrosion Resistance | Material-dependent | Material-dependent |
Gas Diffusion | May offer good gas diffusion | Improved gas diffusion due to porous structure |
Common Applications | Electrodes in electrolyzers | Gas diffusion layers in fuel cells |