Wax Conditioning Materials
Wax Mold conditioners and mold surface sealers are sheets and transfer pellets that condition the transfer-grade or compression-grade mold for the use of thermoplastic and thermoset plastic materials. These materials are used after the cleaning process to ensure that the mold is set to mold another 50, 300 or 800 shots of epoxy molding compound - without sticking - before needing to be cleaned again.
Mold conditioners are often heavily waxed, not catalyzed version of the thermoset plastic being used. When molding epoxy molding compounds, the mold conditioners have three to four times the release wax typically used to ensure that enough wax is left on the surface for proper release of the parts after molding.
Please continue to our Learn More section to learn more about what types and forms of mold conditioners are available, the differences in their types and application methods, and how CAPLINQ can help you to select and order the mold conditioning product that is right for your application.
MCN-T20 | Transfer-Grade Wax Conditioning Pellets
- Wax Compound
- Filling deep cavities
- Transfer Molding
- 8 - 12 weeks
WS810 | Wax Conditioning Sheets
- High flow
- Excellent elastic properties
- Homogeneous waxing
- 4 - 6 weeks
WS830 | Wax Conditioning Sheets
- High flow
- Excellent elastic properties
- Homogeneous waxing
- 6 - 8 weeks
WS800 | Wax Conditioning Sheets
- Excellent conditioning for green EMCs
- Fast cure time
- No lead frame and preheating required
- 6 - 8 weeks
Product Selector Guide
Product Name | Technical Specifications | Comments | ||||
---|---|---|---|---|---|---|
Package | Application method | Pressure (T) | Mold Temperature (°C) | Curing Time (min) | ||
WS300 | Wax Sheet | Compression | 30 - 130 | 165 - 200 | 5 - 10 | Carcinogen free. High fluidity, and minimal odor are intended for IC & Discrete application processes. |
WS350 | Wax Sheet | Compression | 20 - 150 | 160 - 190 | 5.9 | Ecellent workability and no preheating required. |
WS360 | Wax Sheet | Compression | 30 - 150 | 160 - 190 | 4 - 6 | Good workability, highly effective as a protection and release product. |
WS800 | Wax Sheet | Transfer | - | 175 | 2-5 | Minimal application shots, resulting in reliable mold performance |
WS 810 | Wax Sheet | Compression | - | 175 | 3 - 5 | Excellent mold protection requires minimal application shots and shorter cure times. |
WS 830 | Wax Sheet | Compression | - | 175 | 3 - 5 | It can be used for Green or non-Green EMC and manual or auto-molding processes. |
MCN-T20 | Wax Pellet | Transfer | 90 - 110 | 175 - 185 | 2 - 3 | Transfer type. Good workability with minimal odor and exceptional fluidity to fill deep cavities easily |
Learn More
What are Mold Conditioners and why should I condition my mold machine?
Every thermoplastic or thermoset plastic molding machine - on any given molding production line – is limited to a certain number of shots before quality drops and production has to stop for downtime for cleaning.
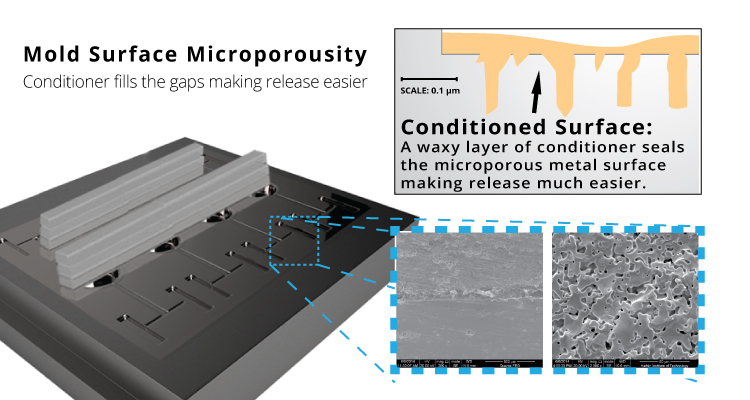
Every molding machine needs downtime for cleaning. The frequency and the time it takes to clean can be reduced by conditioning your mold machine.
On average, thermoset and thermoplastic molding machines can do 300 shots before needing to be cleaned. This is because most plastic compounds leave a residue of internal release behind in the cavity after the de-molded part is removed. This builds up and oxidizes causing a terminal deterioration of quality over time.
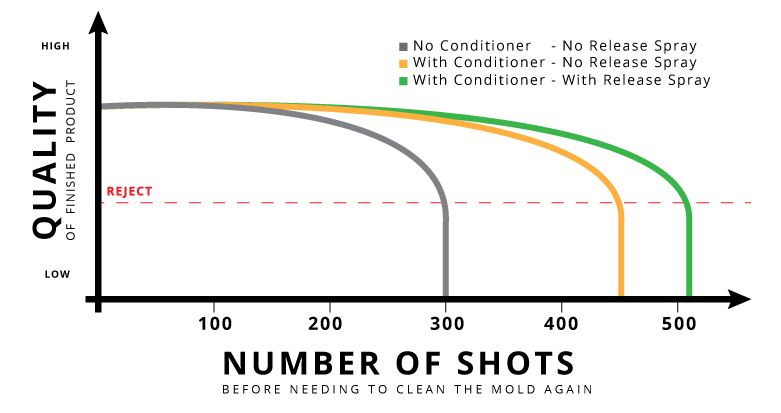
The rate of deterioration of quality can be significantly decreased by conditioning the surface of your mold. This increases the number of shots between cleaning cycles. Conditioner therefore effectively decreases downtime and increases productivity.
Mold Conditioners vs Mold Release Spray
An application of mold conditioner forms a semi-permanent layer on the surface of the mold. This semi-permanent layer seals the microporous metal structure of the mold plates surface. It is also designed to last longer before oxidizing and to function not only as a release but as a mitigating buffer between the internal release of the molding compound and the surface of the mold. Mold Release Sprays, on the other hand, are a temporary layer of a compound designed only to help increase the releasability of the de-molded part.
Another important distinction is that mold release sprays must be manually applied by technicians so they are prone to inconsistent application and even user error. In contrast, mold conditioner is applied mechanically, either by compression or transfer: delivering consistent application: free of human-error.
Notice that mold release spray is messy and gives an uneven layer: either too thick or thin.
Mold Release Spray also only last 50 shots before needing another spray which inevitably builds upon previous inconsistencies making the spray ever more uneven over time.

Chemlinq Mold Conditioner for Transfer Molding
Our pelletized mold conditioner is great for reaching all the nooks and crannies, corners, and edges of more complex or delicate transfer molds. Since they are applied in the same way as the standard pellets of molding compounds they also condition the inner channels and runners of the mold –admittedly this is less of an issue since they are not directly under temperature.
It is also highly accurate: conditioning exactly where the epoxy molding compound with come into contact with the mold surface. Our Chemlinq conditioners are especially compatible with epoxy mold compounds because they share the same essential composition, just with much more wax.
Procedure for conditioning the mold using melamine compounds
The melamine cleans the mold down to the bare metal. It is necessary to have a layer of wax on the surface so that the mold compound will release from the mold.
Once the mold is clean, follow these steps:
- Set the press to standard processing parameters
- Prepare the mold by first lightly waxing with spray wax
- Then mold 3 to 5 shots of melamine conditioning compound using a curing cycle 2 to 3 times longer than normal
- The first three shots of standard molding compound should be cured 2 to 3 times longer than normal in order to ensure that press equilibrium temperature and optimum release characteristics are achieved
- Then resume molding under normal process conditions.
Chemlinq Conditioning Wax Sheets: Mold Conditioner for Compression Molding.
Conditioning Wax Sheets are better for covering molds with larger surfaces area as they spread out very far under compression. The sheets come in a variety of different grades: low, medium, and high wax content conditioning sheet for maximum mold surface protection.
All of our Wax Conditioning Sheets have great workability!
Depending on the workability of your molding compound (how easy it demoulds) grades with a higher wax content are better for compounds that tend to cling to the mold cavity more. We also have Wax Conditioning Sheets in low and high viscosity iterations: low viscosity for simple molds and high viscosity for more complex mold cavities.
Procedure for conditioning the mold using wax sheets
Once the mold is clean, follow these steps:
- Set the press to standard processing parameters
- Rip the wax sheets to the best size to be used in your mold
- Cover the mold with a generous amount of wax conditioning sheets.
- Mold a shot of wax conditioning sheets using a regular curing cycle
- Repeat this conditioning process with 2 to 3 shots of wax conditioning sheets
- Then resume molding under normal process conditions