Hybrid Dual-Clutch Transmission
Introduction
The integration of advanced transmission systems plays a pivotal role in enhancing vehicle performance and efficiency. Clutch transmissions, particularly dual-clutch systems, are increasingly being adopted in electric and hybrid vehicles to offer seamless power delivery and improved driving dynamics. These transmissions enable quicker and smoother gear shifts, which are essential for optimizing the electric powertrain's efficiency and responsiveness. By utilizing dual-clutch technology, electric vehicles can achieve better acceleration, enhanced energy recuperation, and overall improved drivability.
How Dual Clutch Transmission (DCT) work?
What is the difference for Hybrid Dual Clutch Transmission (HDTC)?
An HDCT incorporates the features of a DCT but is specifically designed to work in conjunction with a hybrid powertrain. In addition to the internal combustion engine, an HDCT integrates an electric motor and a hybrid power system, such as a battery pack. This allows for the seamless blending of power from both the internal combustion engine and the electric motor.
Key features of an HDCT compared to a standalone DCT
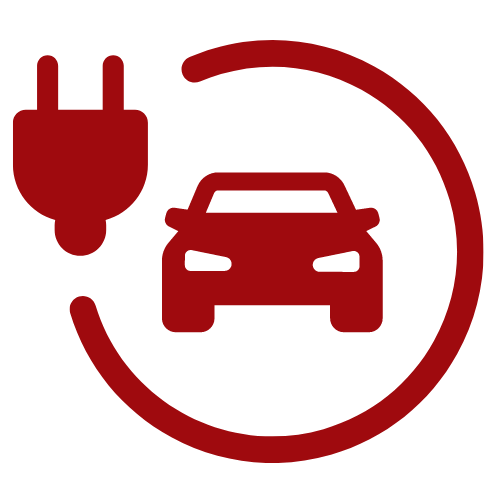
Hybrid Power Integration
HDCT is part of a hybrid powertrain wherein it can manage the distribution of power between the internal combustion engine and the IPM electric motor. This integration enables electric-only driving, hybrid driving modes, and regenerative braking.
.png)
Energy Recovery
HDCT, being part of a hybrid system, can take advantage of regenerative braking to recover and store energy in the battery packs. This contributes to overall energy efficiency and fuel savings.
.png)
Electric-Only Mode
In certain driving conditions, an HDCT-equipped hybrid vehicle can operate solely on electric power, utilizing the electric motor without engaging the internal combustion engine. EV Propulsion System
.png)
Enhanced Fuel Efficiency
The hybridization allows for optimized power conversion delivery based on driving conditions, contributing to improved fuel efficiency and reduced emissions.
Engine and Motor Operation
In a hybrid system, the motor supports the engine, improving driving performance and fuel consumption by regenerating with the motor and storing energy in the battery, using this to drive like an EV and for accelerating. The one-motor two-clutch hybrid system can separate the engine from the drivetrain as necessary. It can utilize the engine and motor as power sources, from running just on the motor to using both motor and engine for full acceleration, achieving a more efficient drive as per the situation. During regeneration and electric-mode driving, the engine is completely disconnected from the drive-train, resulting in zero loss from engine friction.
The operation of the clutches varies based on the driving situation, utilizing the engine and motor in different ways as follows:
Clutch #1 Disconnected, Clutch #2 Connected
Efficient use of battery power | Zero engine friction and noise | Ideal for low-speed or idle situations
Clutch #1 Connected
Immediate power transfer due to the absence of a torque converter | Enhanced driving performance | Suitable for high-speed and high-power demands
Clutch #1 Connected
Utilizes high-output lithium-ion battery for additional power | Optimal for overtaking and rapid acceleration needs
Clutch #1 Disconnected, Clutch #2 Connected
Efficient battery charging from the motor | Reduces wear and tear on the engine | Ideal for energy recovery during deceleration or stationary periods
Components System & Material Solutions
Clutch Assembly
Image from: https://www.linkedin.com/pulse/clutch-components-alice-lan/
Silyl-Modified Polymers (SMP) and Polyurethane (PU) Adhesives and Sealants for Bonding of Clutch Plates
These adhesives provide strong, durable bonds necessary for attaching friction materials to the clutch plates. Their resistance to high temperatures and environmental stressors ensures longevity and reliability.
BS7000F SMP series are fire-safe (meeting EN 45545 standards) and remain elastic over a wide temperature range (-40°C to 100°C), making them suitable for the temperature variations.
BS 9000 Series are PU based chemistry adhesive which has high strength and thixotropy
Transmission Housing
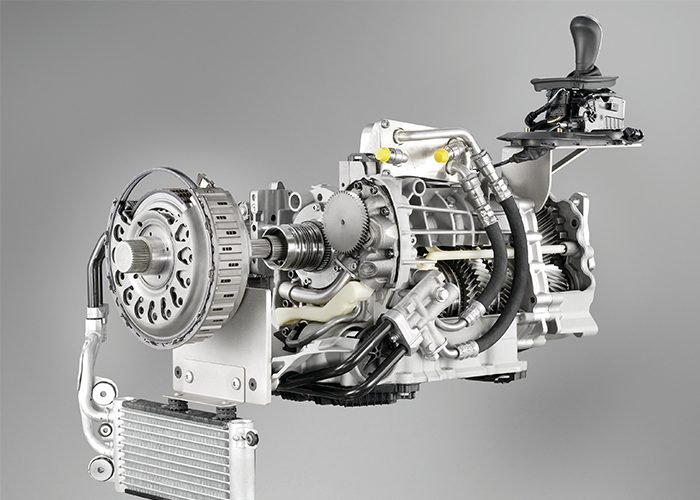
Image from BMW DCT transmission
Polyurethane (PU) Adhesives for Transmission Housing
PU adhesives (BS900) are particularly suited for bonding components within the transmission housing, where their high strength and resistance to oil and heat come into play.
Polyurethane and Silicone Sealants
These sealants are used to create tight seals in the transmission housing, preventing oil leaks and ensuring that the internal components are protected from external contaminants.
Valve Body & Pump Housing
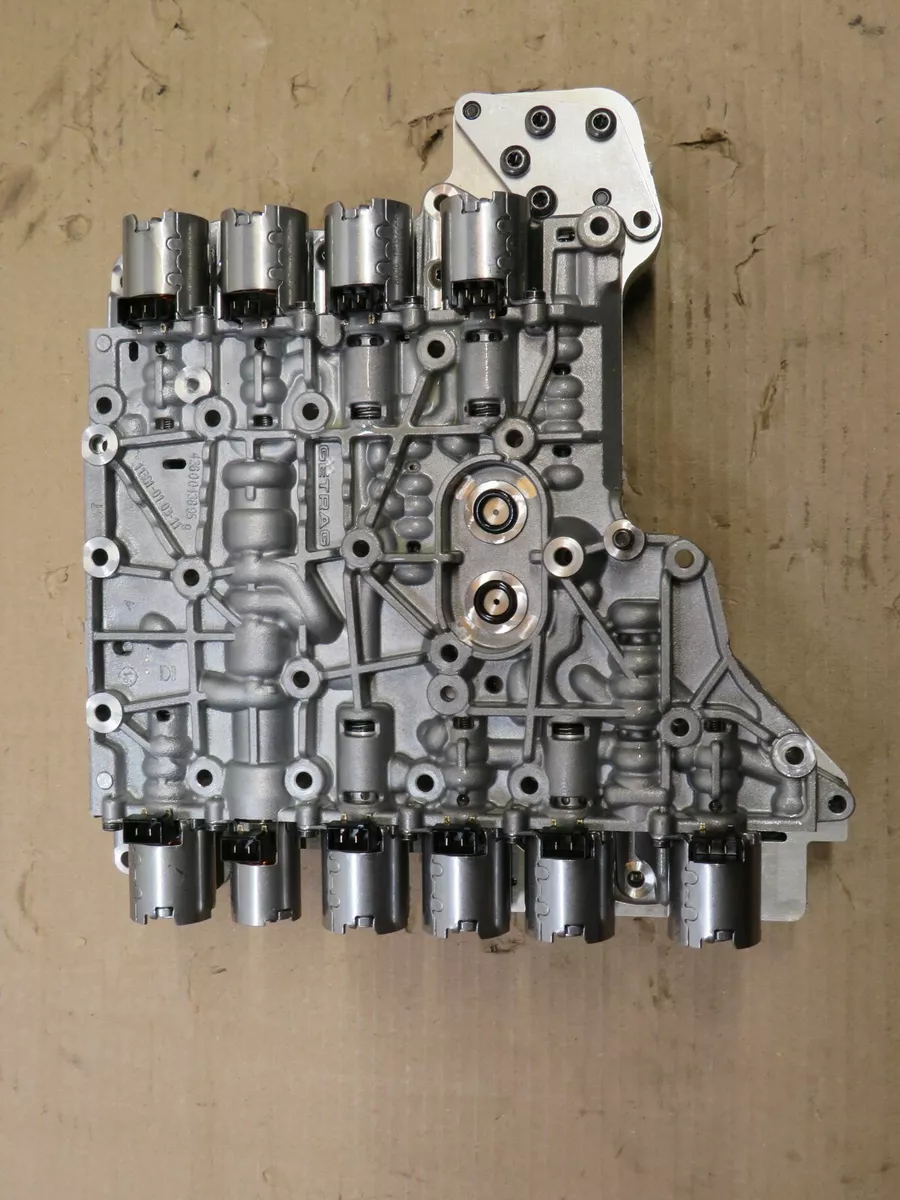
Flat Gaskets:
Provide static seals between stationary parts of the DCT to prevent the leakage of transmission fluid and other contaminants.
LINQSEAL GS-PTFE boasts outstanding dielectric properties and remarkable temperature stability, ranging from –180 °C to 260 °C. Its unparalleled chemical resistance extends to acids, bases, and solvents.
LINQSEAL GS-VMQ possesses excellent resistance to extreme temperatures from –55 °C to 210 °C. It also exhibits low compression sets, meaning it maintains its shape and sealing properties over time, ensuring reliable performance throughout the operational life of the system.
Flat gaskets made of PTFE or FKM are used in sealing valve bodies and pump housings due to their excellent chemical resistance and ability to withstand high temperatures and pressures.
LINQSEAL GS-EPDM is highly recommended as outdoor sealing material. These gasket's rubber material exhibits high resistance to a wide range of environmental factors, including heat, cold, ozone, steam, electricity, UV rays, abrasion, and water, making it a preferred choice for various outdoor and challenging conditions.
LINQSEAL GS-FKM are composed of a fluorocarbon rubber, which stands out as a premier elastomer due to its remarkable chemical resistance. It is a sealing material in the aerospace sector for auxiliary power units, connectors, line fittings, hydraulic actuators, pumps, valves, and oil reservoirs.
Thermal Interface Materials Application on HCDT Components
Operating Temperature, oC | Materials Use | |
Clutch Components | 150 - 200 | Thermal Grease Phase Change Materials |
Power Electronics (Inverter and Motor Controller) | (-40) - 100 | Phase Change Materials |
Power Electronics ( Semiconductor Devices) ex. IGBTS, MOSFETS | (-40) - 150 | Phase Change Materials PTM6000HV (Optimized for IGBT printing) |
Transmission Fluid Temperature Control | 70 - 100 | Phase Change Materials Thermal Gap Pads Thermal Grease |
Electric Motor | Generator | (-40) - 100 | Phase Change Materials Thermal Gap Pads Thermal Grease |