DC/DC Converter
How DC-DC Converter works?
DC-DC Converter primary function is to convert the voltage of a direct current (DC) source from one level to another, ensuring stable and efficient power delivery to various electronic devices and systems.
The transistor rapidly switches on and off, controlling the flow of current through the inductor.
When the switch is on, current flows through the inductor, storing energy in its magnetic field.
When the switch is off, the inductor releases the stored energy, which is then smoothed by the capacitor to provide a stable output voltage.
Common Types of DC-DC Converter and Device Applications
Buck Converter (Step Down) reduces the input voltage to a lower output voltage.
Device Application: Mobile Devices Power Management | Computers (CPU & GPU) | Electric Vehicle Battery Power Management | Renewable Energy SystemsBoost Converter (Step Up) increases the input voltage to a higher output voltage.
Device Application: Solar Power LED Street Light | Flashlights | Laptop | Uninterruptible Power Supply (UPS) | EV DC Motor Drives | Transmitters | Radios | Solar Panel | Wind Turbines | Fuel Cells
Buck-Boost Converter (Universal) can either increase or decrease the input voltage, depending on the circuit configuration.
Device Application: Universal Battery Charger | Digital Cameras | Wearable Devices | Car Electronics | EV LED & Communication Systems | Insulin Pumps | Portable Ventilator
DC-DC Converter Components & Materials
The construction of DC to DC converters involves multiple components such as the transformer, inductor, diodes, capacitors, and semiconductors. These components need to be appropriately connected to perform the required electrical functions. In the assembly process, adhesives are used to secure the components to the printed circuit board (PCB) to ensure that they remain in place during operation. The adhesives used in the assembly process must provide a reliable and robust bond while maintaining the electrical performance of the circuit.
To ensure the long-term reliability of DC to DC converters, the selection of materials is critical. The devices need to withstand extreme environmental conditions such as high temperatures and vibrations without degrading the performance of the circuit. Chemicals such as epoxy resin, silicone, and polyurethane adhesives are used to protect the circuit from environmental factors and ensure that the device remains operational.
Inductors

Epoxy Coating Powders for Inductors
GCP18-05: Halogen-Free Epoxy Coating Powder for Passive Electronic Components
LINQSOL™ GCP1805 is an insulating epoxy coating powder for capacitors, varistors, and other passive components. It was designed specifically as a halogen-free version of DK18-05 with similar technical specifications, just without containing any of the halogens. It can be applied through a fluidized bed with temperatures as low as 105°C. Its excellent curing conditions make the epoxy coating powder also very suitable for tantalum capacitors and other temperature-sensitive devices.
Capacitor

Epoxy Coating Powders for Capacitors
GCP18-05: Halogen-Free Epoxy Coating Powder for Passive Electronic Components
Linqsol GCP1805 is an UL 94 V-0 listed halogen-free product and pass UL RTI rating of 130 °C. With excellent dielectric properties and low moisture absorption, GCP1805 works best for your passive component applications, including capacitors, resistors, inductors, etc.
Epoxy molding compounds for Capacitor
Product | Key Feature |
Hysol GR 2220 | Designed for molding of MnO based tantalum capacitors; Lower cost; High productivity |
Hysol GR 2310 | Standard material designed for tantalum and niobium capacitors using MnO |
Hysol GR 2320 | |
Hysol GR 2330 | |
Hysol GR 2710 | Low stress; Designed for auto-molding of polymer and aluminium capacitors |
Hysol GR 2720 | |
Hysol GR 600 | Low moisture absorption;high reliability for aluminum capacitors |
Hysol GR 2811 | Ultra-low stress; High crack resistance for automolding of conductive polymer especially with thin wall |
Hysol GR 2812 | Up to MSL3; Low ESR; Low leakage; Low stress |
Hysol GR 2820 | Low ESR; Low leakage; Low stress; Suitable for conductive polymer tantalum capacitors |
Hysol GR 2822 | Up to MSL3; Low ESR; Low leakage; Low stress; |
All products are "Green"
Transistor Switch
Silicone Carbide Switches. These MOSFET devices help us pack more punch in a smaller space and allow devices such as power control units to operate. Their vertical design and the very high performance of SiC makes it a major step ahead of the IGBT power modules. The problem with all this power is that it generates heat that needs to be dissipated very efficiently in order for the device to continue to operate. This bring material challenges that can only be solved with cutting edge thermal interface materials and epoxy molding compounds.
Gallium Nitride Switches. These GaN switches have ridiculous switching speeds, up to 2MHz but are limited to specific types of applications for the time being. They are mainly stacked vertically but their exotic high electron structure makes them cost ineffective for large-scale applications (for now). They work amazingly well with chargers and other such devices and are the main reason your latest 120W brick can charge your phone in 15 minutes.
Diode
Diodes in DC-DC converters function is in controlling current direction, facilitating energy transfer, and contributing to rectification. Their characteristics, such as forward voltage drop, reverse recovery time, and current/voltage ratings, are crucial for ensuring efficient and reliable operation of the converter. Schottky Diodes are known for their low forward voltage drop and fast switching speed, making them ideal for high-frequency DC-DC converters.
Controller IC
Controller ICs are for managing the operation of DC-DC converters. They regulate the output voltage or current, control the switching of transistors, and provide feedback mechanisms and protection features.
Other Materials Used in DC-DC Converter Assembly
Chemical substances such as flux and solder paste are also used in the construction of DC to DC converters. The flux is used to remove any impurities or oxidation from the solder surfaces before soldering, enabling a strong bond between the components and PCB. The solder paste is used to join the components to the PCB and is heated to create a strong bond.
Assembly adhesives
Epoxy resin is a common adhesive used in DC to DC converter construction because of its high strength and resistance to thermal and mechanical stress. Silicon adhesives are also used due to their excellent flexibility and electrical insulation properties. Polyurethane adhesives are used to protect circuits from harsh chemicals and extreme temperature environments.
DC to DC converters are a critical component in a range of electrical applications. The construction of these devices involves the use of adhesives, solder paste, and flux to connect the components to the PCB. To ensure long-term reliability, materials such as epoxy resin, silicon, and polyurethane adhesives are used to protect the circuit from environmental factors. The selection of materials and chemicals used in the construction of DC to DC converters is essential for maintaining the operational integrity of the device.
Thermal interface materials
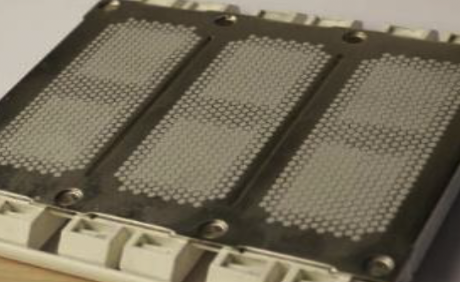
Thermal interface materials (TIMs) are also an important consideration in the construction of DC to DC converters. These materials are used to improve the heat dissipation from the converter components, such as the power semiconductors and inductors, to the heat sink or PCB. This is important because excessive heat can lead to the failure of the device, decrease its performance, or even shorten its lifespan.
There are several types of TIMs that can be used in DC to DC converters, including thermal greases, gap fillers, and phase-change materials. Thermal greases are composed of a silicone oil base with added filler particles, which help to improve thermal conductivity between the surfaces. Gap fillers are soft materials that can conform to irregular surfaces to fill any gaps, providing a more complete contact between the heat sink and the component. Phase-change materials are solid at room temperature but become liquid when exposed to heat, enabling them to flow and fill in any gaps, providing better thermal contact.