HPA-LU-M | Low Th & U Alumina
- 4N - 5N Purity
- Ultra low uranium & Thorium
- Ideal as an EMC filler
Product Description
HPA-LU-M is characterized by its exceptionally low levels of uranium and thorium, achieving an impressive purity range of 4N to 5N (99.99% to 99.999%). This ultra-pure material is applicable for critical applications where minimal radioactive impurities are essential, making it particularly well-suited for semiconductor epoxy molding compound (EMC) fillers and other advanced technologies.
HPA-LU-M features an irregular particle morphology that enhances surface contact, resulting in increased dispersion and integration in composite materials. Its specific surface area, ranging from 8 to 15 m²/g, ensures controlled reactivity and stability, contributing to consistent performance across various high-tech applications. With a D50 particle size distribution between 1-5 µm, this alumina product guarantees uniform mixing and processing, crucial for industries that demand precision and reliability. Whether used in semiconductor manufacturing, advanced ceramics, specialty coatings, or optoelectronics
Technical Specifications
General Properties | |||||||||||
Density (g) | 0.3 - 0.5 g/cm3 | ||||||||||
Morphology | Irregular | ||||||||||
Particle size (D50) | 1 - 5 um | ||||||||||
Purity | 99.99 - 99.999 % | ||||||||||
Surface Area | 8 - 15 m2/g | ||||||||||
Chemical Properties | |||||||||||
Phase | a | ||||||||||
Other Properties | |||||||||||
|
Additional Information
Purity | Key Element concentration (ppmw) | ||||||||
Na | Mg | Si | Ca | Ti | Cu | Cr | Fe | K | |
4N | <30 | <5 | <10 | <10 | <5 | <5 | <5 | <20 | <10 |
5N | <4 | <1 | <3 | <3 | <0.5 | <0.5 | <1 | <1 | <0.5 |
Applications
Epoxy Molding Compound (EMC) Fillers
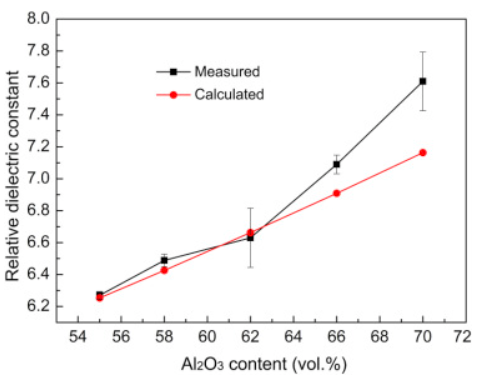
Increasing relative dielectric constant of the Al2O3/epoxy composites as a function of the Al2O3 content
Reference: https://doi.org/10.1016/j.compscitech.2016.01.010
Additionaly, HPA increased the flexural strength of the epoxy molding compound. The table below shows that the flexural strength are remarkably higher on epoxy system with Al2O3 as fillers compared to silica and AlN.
Composites | Filler cont. (Vol.%) | Flex. Strength (Mpa) | Therm. Conduct. (W/m-K) |
---|---|---|---|
AlN/Epoxy | 58 | 101.3 | 3.56 |
Al2O3/Epoxy | 60 | – | 4.3 |
Al2O3/Epoxy | 58 | 150.9 | 7.15 |
AlN/Epoxy | 70 | 180 | 4.6 |
Cryst. SiO2/Epoxy | 70 | 145 | 2.0 |
Diamond/Epoxy | 68 | – | 4.1 |
Al2O3/Epoxy | 70 | 304.9 | 13.46 |
How to improve compatibility of HPA fillers to Epoxy Molding Resin (EMR)?
Using High Purity Alumina (HPA) as a filler in epoxy mold resin (EMR) can have implications for thermal degradation and cracking, depending on factors like filler loading, particle size, and resin compatibility. These are very common not just with HPA, but other fillers as well such as silica. Here are the key considerations:
(1) Epoxy resin decomposition typically starts around 250–350°C, depending on the formulation.
(2) HPA has excellent thermal stability, but if the filler-resin interface is weak, thermal cycling can lead to microvoids or interfacial degradation, reducing performance over time.
(3) High HPA loading can increase thermal conductivity, reducing hot spots, but excessive amounts may compromise the resin’s mechanical integrity.
(4) Poor dispersion of HPA can create stress concentration points, acting as crack initiation sites.
(5) Higher HPA loading increases stiffness but reduces fracture toughness, making the composite more prone to cracking under mechanical stress.
Typical strategies on the EMC formulation for fillers compatibility are the following:
(1) Optimize Filler Loading: Maintain a balance between thermal conductivity improvement and mechanical flexibility.
(2) Use silane coupling agents to improve HPA-resin adhesion, reducing interfacial cracking.
(3) Combining HPA with other fillers (e.g., silica, boron nitride) can help mitigate CTE mismatch and improve fracture toughness.
Semiconductor Manufacturing
In semiconductor applications, the ultra-low impurities of HPU-LU-M reduce the risk of contamination, which can cause device failure or decreased performance. The material's high thermal stability and purity ensure that it performs well in the demanding environments of semiconductor fabrication processes.
Advanced Technical Ceramics
The controlled morphology and high purity of HPU-LU-M enhance the mechanical and electrical properties of technical ceramics. These properties are essential for applications requiring high strength, wear resistance, and low dielectric loss, such as substrates, insulators, and advanced structural components.
Additional Information
HPU-LU-M is produced using state-of-the-art manufacturing techniques that ensure the highest standards of quality and purity. Our advanced processing technology guarantees consistent product performance, making it a reliable choice for high-tech applications. Customizable solutions are available to meet specific application needs, supported by our expert technical team and collaborative R&D partnerships.