Hysol GR15F-MOD2C | Black Epoxy Mold Compound
- Very High Glass Transition Temperature: 236°C
- Longer spiral flow than MOD2
- Designed for high voltage, high power discrete packages
Product Description
Hysol GR15F-MOD2C is a black, epoxy-based molding compound designed for high voltage, high temperature semiconductor applications. It has a very high Glass Transition Temperature (Tg) of 236°C and is in use in 2nd generation silicon carbide (SiC) MOSFET of world’s leading manufacturer of Silicon Carbide based diodes for power control and management. This C product is a longer spiral flow version of the MOD2.
Hysol GR15F-MOD2C is the world's first high Tg, "Green" Anhydride. Anhydride-based epoxy has traditionally had a low Tg and contained halogens, making it not environmentally "Green". On the other hand, anhydride chemistries have very good HTRB test results because there is very little ion movement at higher temperatures, the traditional cause of HTRB failures. Hysol's new MG15F-MOD2C is a breakthrough product that offers an incredibly high Tg, and is an environmentally "green" product without any halogens (Bromine, Chlorine) or antimony (Sb).
Hysol GR15F-MOD2C is well suited for SiC devices. Older generation silicon Si MOSFETS operated at (only) 600V. New Silicon Carbide devices operate at 1200V. These new 1200V MOSFETS deliver power density and switching efficiency at half the cost per amp of our previous generation MOSFETs. CREE claims that with this new MOSFET platform, that they already have design wins in multiple segments like solar inverters and uninterruptible power supply (UPS) systems. They continue to say that due to rapid acceptance of this 2nd generation of SiC MOSFETs, CREE is shipping pre-production volumes ahead of schedule and ramping volume production in-line with customer demand.
Hysol GR15F-MOD2C has excellent high temperature reliability bias (HTRB) test results. MG15F-MOD2C Outperforms competition on HSOP “plastic RF module” by passing 1500 cycles -65/+200ºC. Furthermore, it is qualified on TO220 & TO247 packages with large silicon carbide die running up to 1200V at an operation temperature.To add to that, Hysol has more than 12 years experience molding HF RF amplifiers guaranteed for 200°C for continuous operation.
Technical Specifications
General Properties | |||||||||||||
Color Color The color | Black | ||||||||||||
Filler Content | 81.5 % | ||||||||||||
Specific Gravity Specific Gravity Specific gravity (SG) is the ratio of the density of a substance to the density of a reference substance; equivalently, it is the ratio of the mass of a substance to the mass of a reference substance for the same given volume. For liquids, the reference substance is almost always water (1), while for gases, it is air (1.18) at room temperature. Specific gravity is unitless. | 1.94 | ||||||||||||
| |||||||||||||
Physical Properties | |||||||||||||
Spiral Flow @ 175°C | 101.6 cm | ||||||||||||
Viscosity Viscosity Viscosity is a measurement of a fluid’s resistance to flow. Viscosity is commonly measured in centiPoise (cP). One cP is defined as the viscosity of water and all other viscosities are derived from this base. MPa is another common unit with a 1:1 conversion to cP. A product like honey would have a much higher viscosity -around 10,000 cPs- compared to water. As a result, honey would flow much slower out of a tipped glass than water would. The viscosity of a material can be decreased with an increase in temperature in order to better suit an application | 23000 mPa.s | ||||||||||||
Chemical Properties | |||||||||||||
| |||||||||||||
Moisture absorption | 0.54 % | ||||||||||||
Electrical Properties | |||||||||||||
| |||||||||||||
Dielectric Strength Dielectric Strength Dielectric strength is measured in kV per mm and is calculated by the Breakdown voltage divided by the thickness of the tested material. Those two properties go hand in hand and while Breakdown voltage is always thickness dependent, dielectric strength is a general material property. As an example, the dielectric strength of Polyimide is 236 kV/mm. If we place 1mm of Polyimide between two electrodes, it will act as an insulator until the voltage between the electrodes reaches 236 kV. At this point it will start acting as a good conductor, causing sparks, potential punctures and current flow. | 13 kV/mm | ||||||||||||
Volume Resistivity Volume Resistivity Volume resistivity, also called volume resistance, bulk resistance or bulk resistivity is a thickness dependent measurement of the resistivity of a material perpendicular to the plane of the surface. | 7.3x1016 Ohms⋅cm | ||||||||||||
| |||||||||||||
Mechanical Properties | |||||||||||||
| |||||||||||||
| |||||||||||||
| |||||||||||||
Molded Shrinkage | 0.54 % | ||||||||||||
| |||||||||||||
| |||||||||||||
| |||||||||||||
Thermal Properties | |||||||||||||
| |||||||||||||
| |||||||||||||
Glass Transition Temperature (Tg) Glass Transition Temperature (Tg) The glass transition temperature for organic adhesives is a temperature region where the polymers change from glassy and brittle to soft and rubbery. Increasing the temperature further continues the softening process as the viscosity drops too. Temperatures between the glass transition temperature and below the decomposition point of the adhesive are the best region for bonding. The glass-transition temperature Tg of a material characterizes the range of temperatures over which this glass transition occurs. | 237 °C | ||||||||||||
Thermal Conductivity Thermal Conductivity Thermal conductivity describes the ability of a material to conduct heat. It is required by power packages in order to dissipate heat and maintain stable electrical performance. Thermal conductivity units are [W/(m K)] in the SI system and [Btu/(hr ft °F)] in the Imperial system. | 0.8 W/m.K | ||||||||||||
UL 94 Rating UL 94 Rating Flammability rating classification. It determines how fast a material burns or extinguishes once it is ignited. HB: slow burning on a horizontal specimen; burning rate less than 76 mm/min for thickness less than 3 mm or burning stops before 100 mm V-2: burning stops within 30 seconds on a vertical specimen; drips of flaming particles are allowed. V-1: burning stops within 30 seconds on a vertical specimen; drips of particles allowed as long as they are not inflamed. V-0: burning stops within 10 seconds on a vertical specimen; drips of particles allowed as long as they are not inflamed. 5VB: burning stops within 60 seconds on a vertical specimen; no drips allowed; plaque specimens may develop a hole. 5VA: burning stops within 60 seconds on a vertical specimen; no drips allowed; plaque specimens may not develop a hole | V0 | ||||||||||||
Curing Conditions | |||||||||||||
| |||||||||||||
| |||||||||||||
Transfer Time | 10 - 20 s |
Additional Information
Electrical Properties
Test Mode | Alternating Current | Direct Current | |
Voltage Ramp Speed (KV/sec) | 2 | 4 | |
Dielectric Strength (KV/mm) | MG 15F-MOD2 C | 13 | 41 |
Test utilized insulating oil as surrounding medium.
Epoxy molding compounds for Silicon Carbide (SiC) Shottky diodes.
Where do we go from here?
Do you have any molding compounds that can be used for Space applications and withstand temperatures above 200°C?
There is not much research going on regarding EMC specifically suitable for space applications.
Due to the restriction of the EMC chemistry system itself, they all start to show some extent of properties degradation from 200 ℃. Hysol has done research on innovative resin/hardener types and modifications, but the results are still confidential and could not be shared yet. For example, there is research in china and japan regarding the benzoxazine resin types in the academic institute, but again, not been commercialized yet. Here is a review paper for your reference. There are some other types of encapsulants such as silicone-based ones that could resist higher temperatures, but they are not suitable for the molding process but for potting.
How do you measure temperature stability in EMCs? Is there an industry standard?
The ideal is to test the stability of each property for long hours on your operating temperatures. As you can see, there are several groups of properties to describe an EMC product. The degradation of hygro-thermomechanical, electrical, and chemical properties is what we look into while doing the high-temperature storage tests.
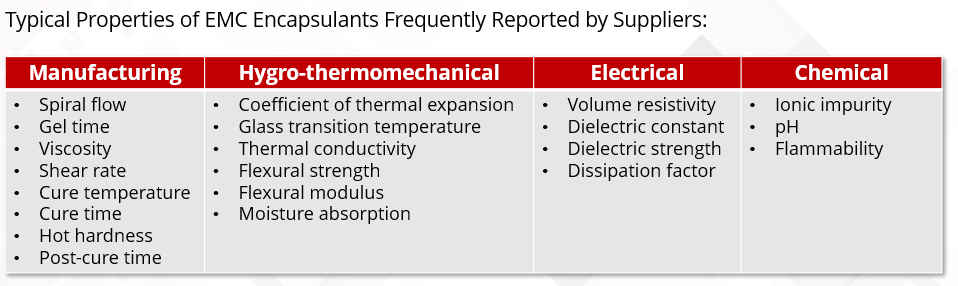
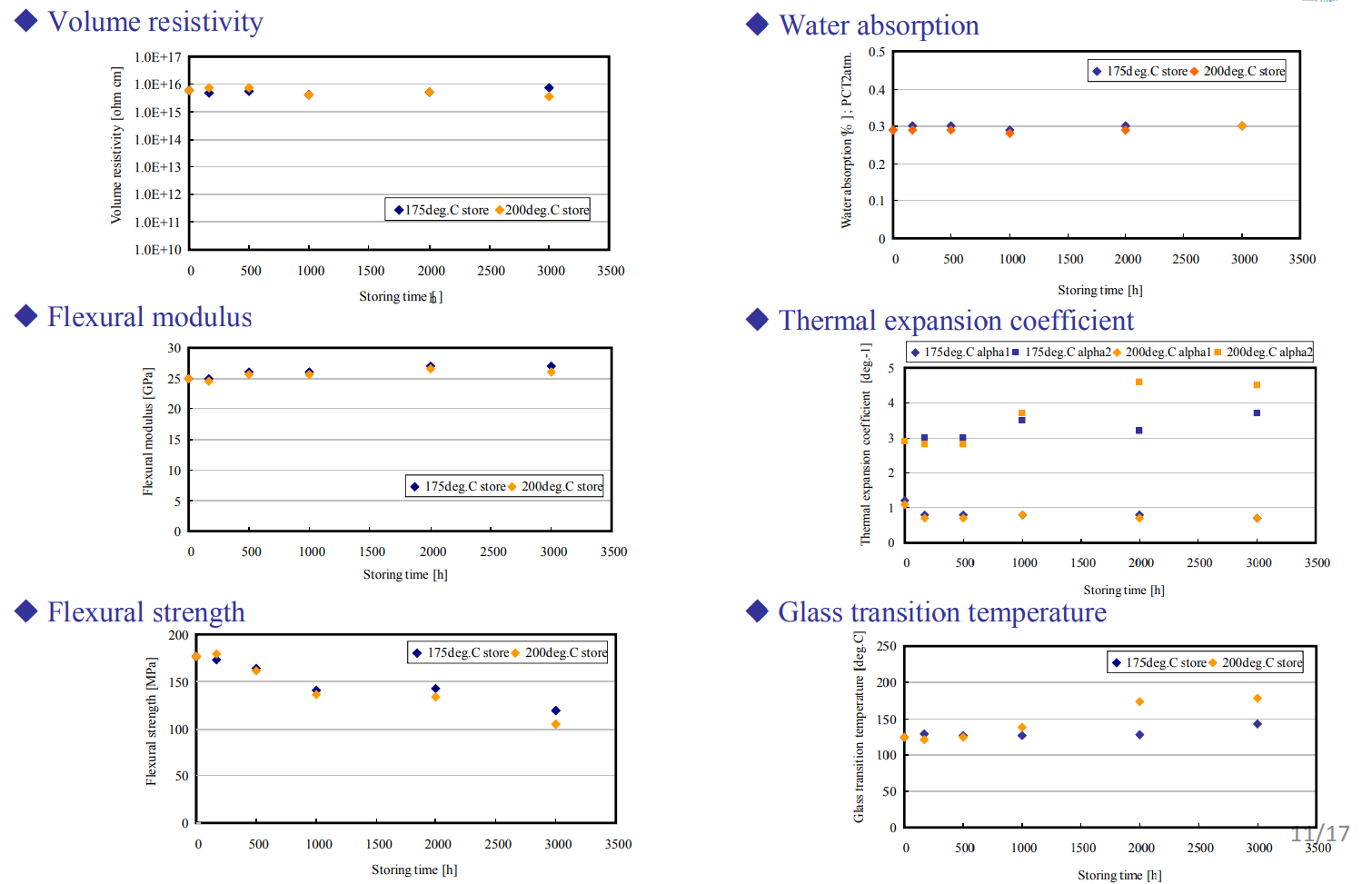
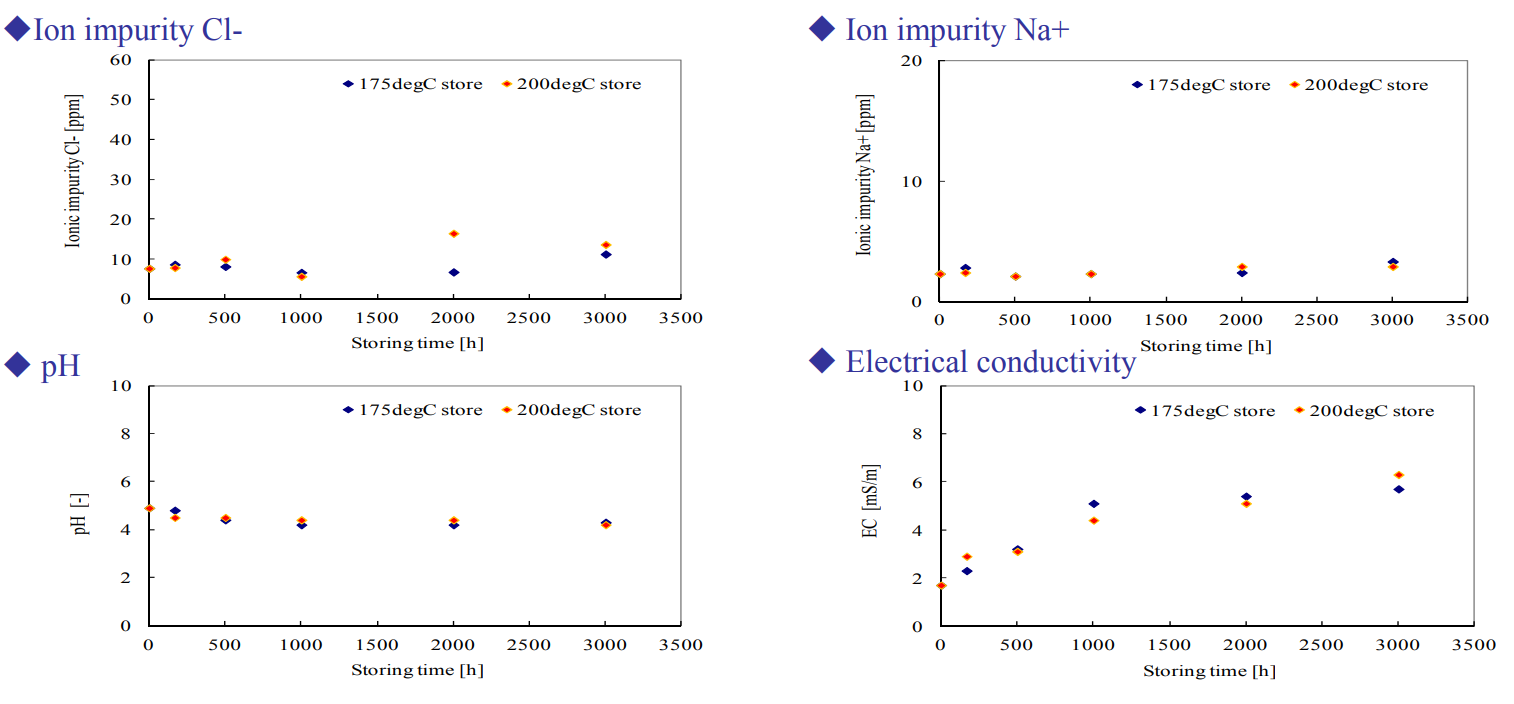
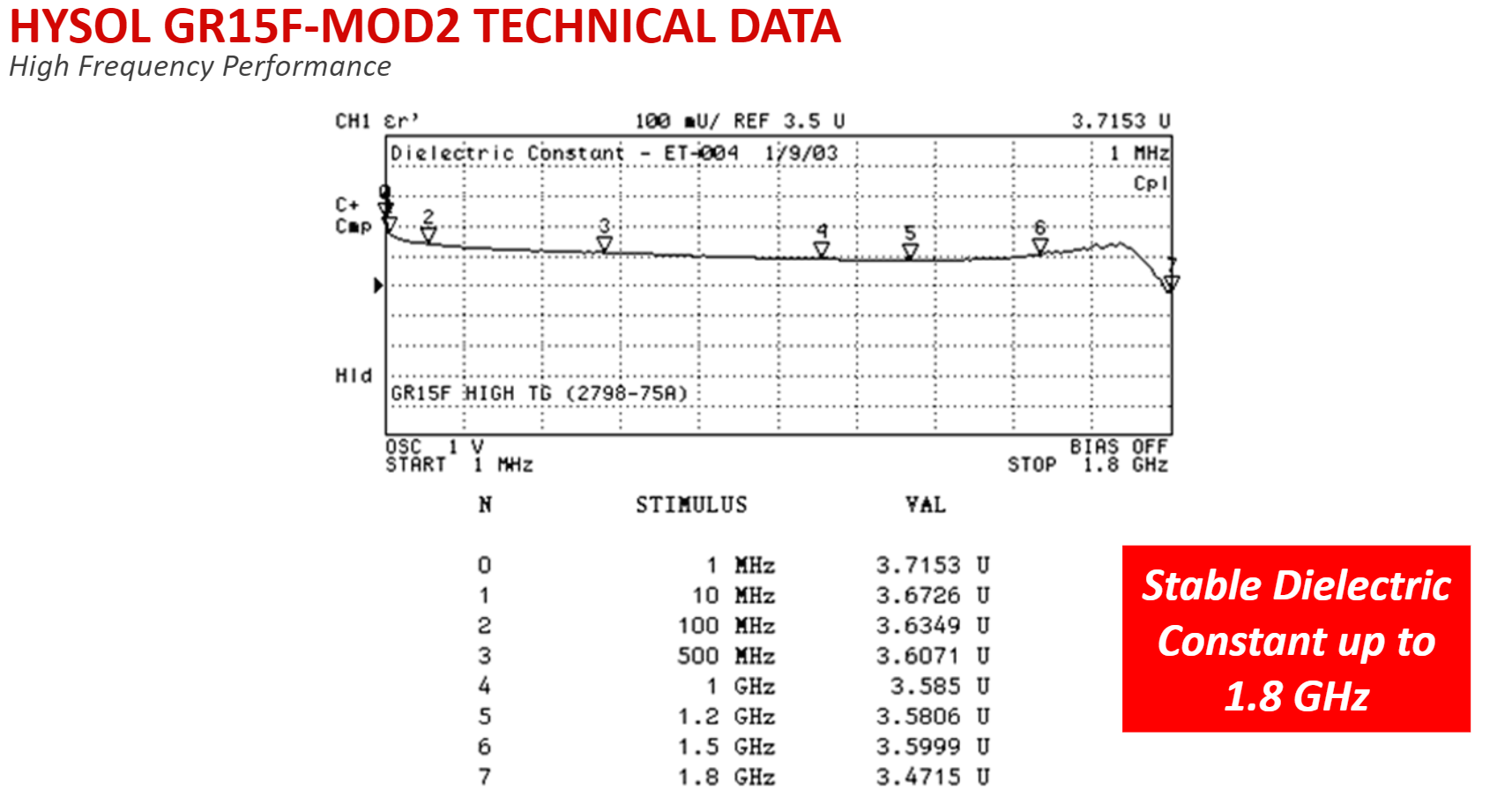
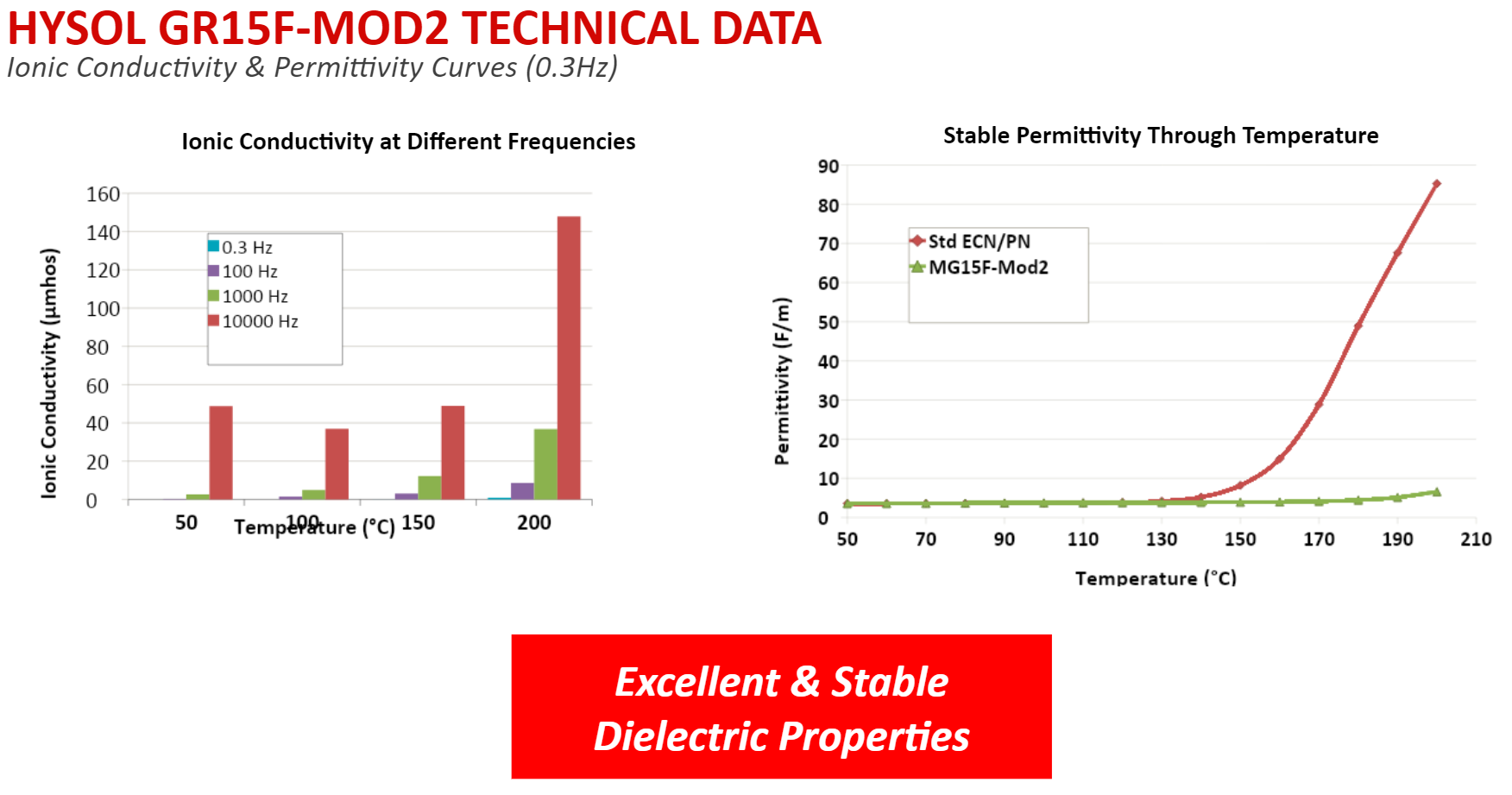
Hysol GR15F-MOD2C Black is sometimes spelled in slightly different ways including:
- Hysol MG 15F-MOD2 C
- Hysol MG15F-MOD2 C
- Hysol MG 15F-MOD2C
- Hysol GR15F-MOD2C
- Hysol GR 15F-MOD2C
Anhydride epoxies tend to stick quite a lot to the mold. It is common to use up to 10 shots of melamine to clean the molding compound residues. Visit our Cleaning and Conditioning category to find the ideal cleaning solution for your process.