LINQCELL GFP2000 | Graphite Felt
- 2.00 mm - 2000 µm - 78 mil
- High chemical resistance, electrical conductivity, and open porosity
- Electrode materials for high-temperature batteries
Product Description
LINQCELL GFP2000 is a 2.00-mm thick graphite felt made from high-quality polyacrylonitrile (PAN) fibers. The felt is processed into a non-woven structure, then carbonized and graphitized to enhance electrical conductivity, oxidation resistance, and thermal stability. It is well-suited for redox flow and sodium nickel chloride batteries, providing an exceptional blend of electrical conductivity, electrochemical stability, high porosity, and flexibility. This combination promotes effective charge transfer between the electrolyte and the bipolar plate.
Key Features:
- High Electrical Conductivity: The graphitic structure of GFP2000, achieved after high-temperature treatment (above 1000 °C), imparts high electrical conductivity to the felt.
- Oxidation Resistance: PAN is known for its high resistance to oxidation, and GFP2000 exhibits even greater oxidation resistance due to the additional graphitization treatment.
- Thermal Stability: GFP2000 can withstand high temperatures without significant degradation, maintaining its physical and electrical properties under extreme conditions.
- Mechanical Properties: The non-woven structure offers flexibility and resilience, which can be advantageous in applications where the material needs to conform to various shapes or withstand mechanical stress.
- High Open Porosity: GFP2000 maintains high open porosity due to the absence of resins during its manufacturing process, unlike graphitized carbon fiber papers that use a carbonizable resin during the impregnation stage.
Highly Recommended For:
- Electrodes (anode and cathode) of redox flow batteries
- Electrodes in NaNiCl batteries
- Electrodes for electro-synthesis
- Electrodes in sediment microbial fuel cells
Technical Specifications
General Properties | |
Total Thickness Total Thickness Total thickness is taking into account all the films, coatings, adhesives, release liners and special layers and is the maximum thickness of a film or tape. | 3000 μm |
Electrical Properties | |
Voltage loss | 35 mV |
Additional Information
Key Differences between Carbon (Graphite) Cloths, Papers, and Felts
The most common types of carbon (graphite) fiber sheets are carbon (graphite) cloth, carbon paper, and carbon felt, each with distinct characteristics.

Carbon (graphite) cloth is a woven fabric, composed of carbon fibers woven together. Its woven nature makes cloths more flexible and durable, allowing it to conform better to various shapes and sizes, which is advantageous in applications requiring flexibility and durability without the need for additional binders.

Carbon (graphitized carbon) paper is a non-woven material, made from carbon fibers without the need for weaving, resulting in a structure that is typically stiffer and less flexible than carbon cloth. This rigidity provides a stable and consistent structure, making CP ideal for applications where structural integrity is critical.

Carbon (graphite) felt is composed of randomly oriented, spaghetti-like fibers. This random orientation provides high porosity and a less structured material compared to both carbon cloth and carbon paper, which can be advantageous in applications requiring high gas permeability.
SEM images of carbon cloth, paper, and felt are from F.C. Lee, M.S. Ismail, D.B. Ingham, K.J. Hughes, L Ma, S.M. Lyth, M. Pourkashanian, Alternative architectures and materials for PEMFC gas diffusion layers: A review and outlook, Renewable and Sustainable Energy Reviews, Volume 166, 2022, 112640, ISSN 1364-0321, https://doi.org/10.1016/j.rser.2022.112640.
Carbon fiber paper vs. carbon fiber felt
Both materials are non-woven, but one is stiff while the other is flexible. The difference lies in the manufacturing process: carbon fiber paper is produced using resins to form the sheet, whereas carbon fiber felts are non-woven fabrics made from fibers bonded together through felting, thermal bonding, chemical bonding, or mechanical entanglement.
Resins help maintain the straightness of carbon fibers in carbon fiber paper by coating and bonding the fibers during the wet-out process, which ensures they are well-supported and aligned. During curing, the resin hardens, locking the fibers into their straight positions and preventing misalignment. The resin also provides stability and support, ensuring the fibers remain straight and do not shift under stress. In prepreg manufacturing, the pre-impregnated resin further ensures consistent fiber alignment before final processing.
How do Vanadium Redox Flow Batteries Work?
Redox flow batteries (RFBs) stand out as promising solutions for medium to large-scale energy storage applications. Unlike traditional secondary batteries, RFBs provide a unique advantage– the independent scaling of power and energy. This flexibility allows for versatile configurations and operational adaptability. RFBs employ various chemistries, featuring a mix of inorganic and organic species, along with both aqueous and organic solvents. Among the commercially available RFB chemistries, the all-vanadium RFB emerges as the most mature and extensively studied option.
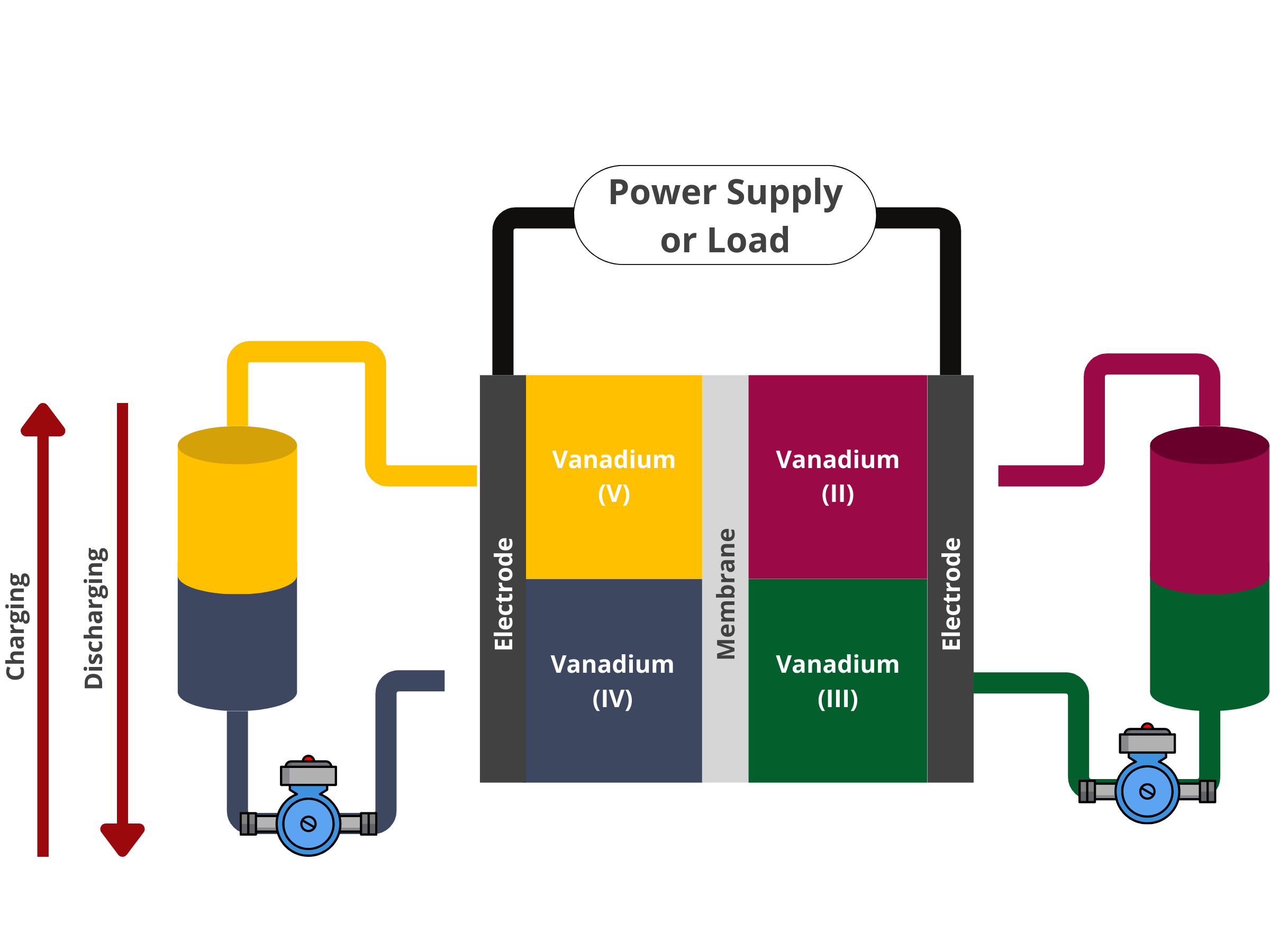
During discharge, V3+ is oxidized to V2+ at the negative side. The generated electron flows through the current collector, the load, and finally to the current collector at the positive side. Ions from the electrolyte (either H+ or SO42–) flow through the ion exchange membrane. Using the ions and generated electrons, VO2+ is then reduced to VO2+ on the positive electrode.
During charging, the reverse processes occur. In simpler terms, throughout the charge-discharge cycle, the active vanadium species in the electrolyte undergo reduction and oxidation, effectively converting chemical energy into electrical energy. Maintaining electroneutrality is seamlessly achieved by transporting ions within the electrolyte through the membrane. The presence of dissolved redox species in the recirculated solution distinguishes RFBs from other batteries that store energy within electrode structures, like lead-acid and lithium-ion batteries. The unique 'non-participating electrode' structure of VRBs allows for the independent customization of power rating and storage capacity.
Electrodes for Redox Flow Batteries
In redox flow batteries, energy is stored in solutions that flow through the system, with their capacity being directly related to the volume of the solution tanks. This battery type is made up of two electrodes separated by a membrane. The energy storage and conversion processes occur on the surface of these electrodes, making the properties of the electrode materials critical to the battery's performance.
Carbon materials, such as graphite felt and graphitized carbon paper, are typically used as electrodes in redox flow batteries. These materials are chosen for their excellent conductivity, chemical stability, and high surface area.