LINQCELL TFP250 | 250um Titanium Fiber Paper
- 0.25mm - 250um - 9.8mil
- 50 - 60% Porosity
- Electrode and Support structure
Product Description
LINQCELL TFP250 Low Porosity (50 - 60%) Titanium Fiber Paper is a high-performance material meticulously engineered for exceptional strength, precise gas management, and reliable performance in various applications. With its low porosity design, this 250-micrometer thick titanium fiber paper delivers outstanding durability and efficient gas diffusion. The thickness tolerance of the TFP250 is ±0.1 mm.
LINQCELL TFP250 features a low porosity structure, ensuring precise control over gas diffusion, reactant distribution, and electrolyte permeation. This makes it an ideal choice for applications that require fine-tuned gas management and efficient performance in electrochemical systems.
Despite its robust construction, LINQCELL TFP250 maintains a basis weight of 45.5 grams, offering the perfect balance between lightweight design and structural integrity. This will change based on the product's porosity % so we are expecting TFP250 to range between ±18.4 to 22.6 grams. Its excellent electrical conductivity and corrosion resistance further enhance its suitability for demanding environments, ensuring efficient electron and ion transport.
Technical Specifications
General Properties | |
Basis Weight Basis Weight Basis weight refers to the weight measured in pounds off 500 sheets of paper in that paper’s basic sheet size. | 45.5 g/m2 |
Porosity Porosity Void fraction is a measure of the void spaces in a material | 50 - 60 % |
Total Thickness Total Thickness Total thickness is taking into account all the films, coatings, adhesives, release liners and special layers and is the maximum thickness of a film or tape. | 250 μm |
Additional Information
Gas diffusion layers, also known as porous transport layers, anodic or cathodic distributors, and liquid/gas diffusion layers, serve as porous transport media in electrochemical devices such as water electrolyzers and fuel cells. In these applications, GDLs aid in the delivery of the reactants to the catalyst layer and also facilitate the removal of water from the system. On top of that, GDLs provide electrical and thermal conduction pathways. Simply put, GDLs are responsible for most (if not all) of the mass and electrical transport processes during the electrochemical operation.
As a general rule of thumb, GDLs must possess excellent transport properties, i.e. they must allow the efficient movement of reactants, products, and other species (electrons) within or out of the cell. GDLs also aid in the water management, ensuring that enough is retained to keep the membrane hydrated and at the same time expelled out to avoid membrane swelling and flooding. The transport properties are known to be influenced by a wide array of factors, including but not limited to the device operating conditions, assembly parameters, and their mechanical and structural properties. The structural makeup of GDLs can be described using several morphological metrics. Among these metrics, porosity, pore size distribution, and thickness are three major properties that can affect the transport properties of GDLs.
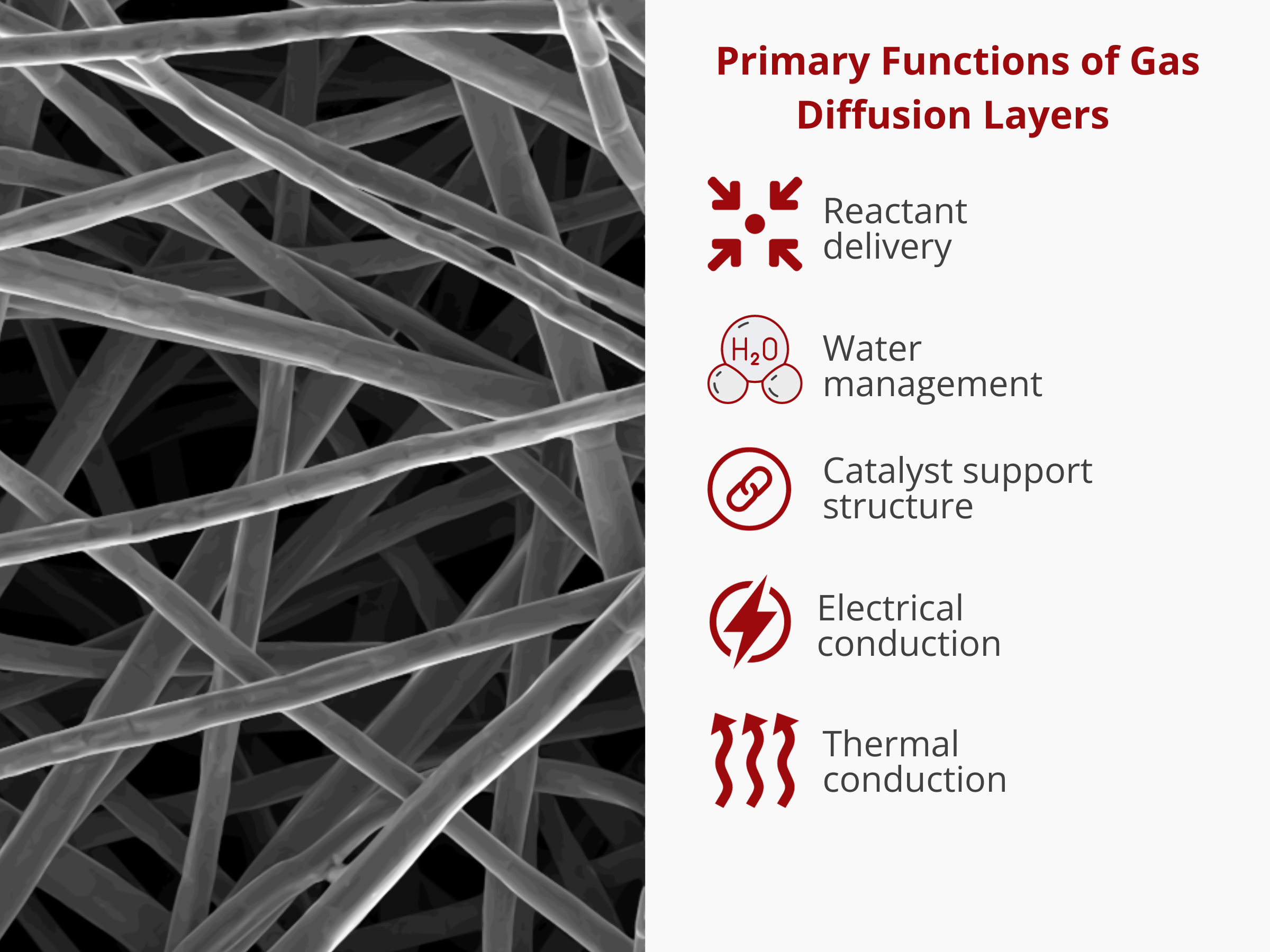
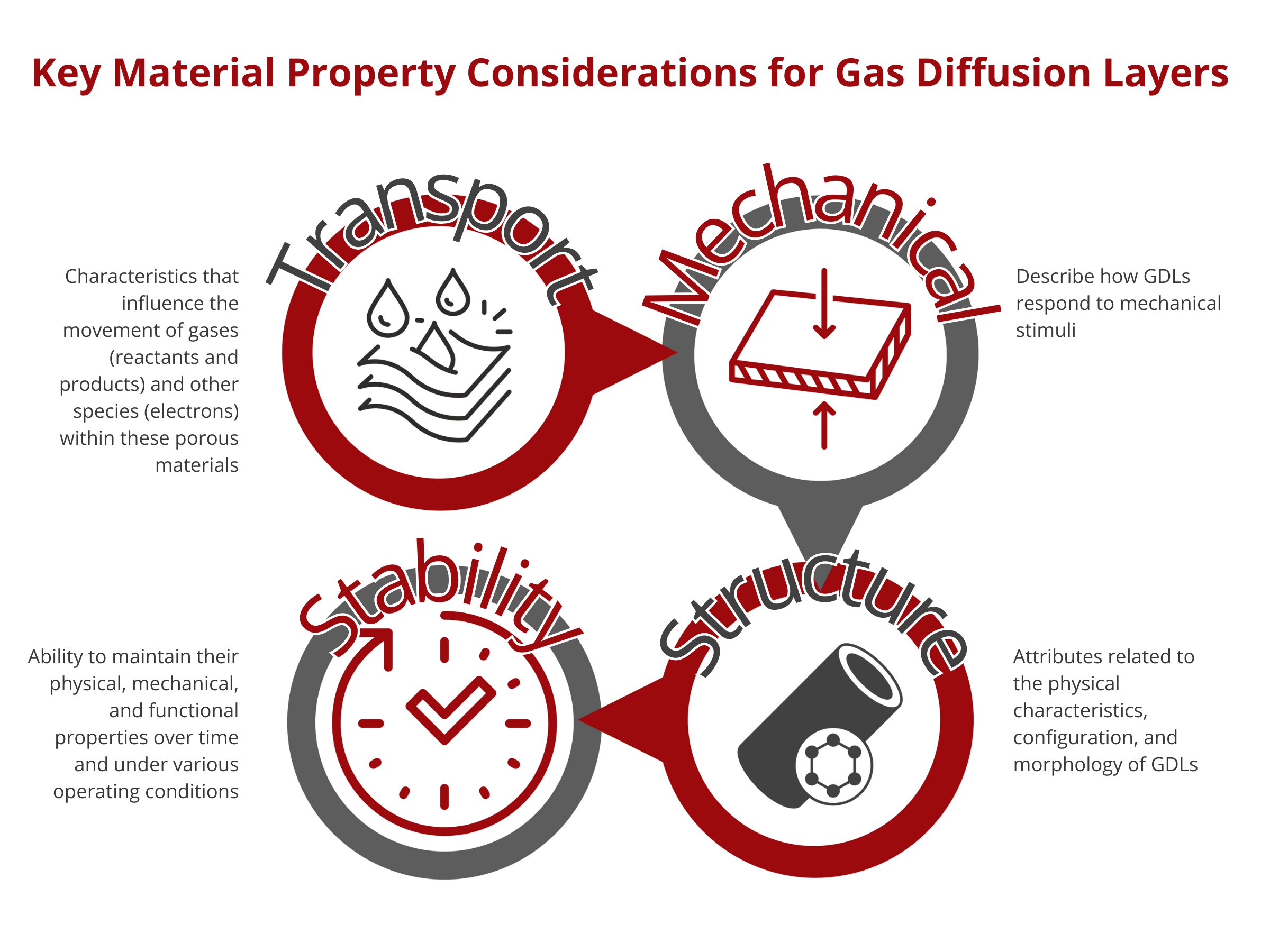
Effect of Porosity on GDL Properties
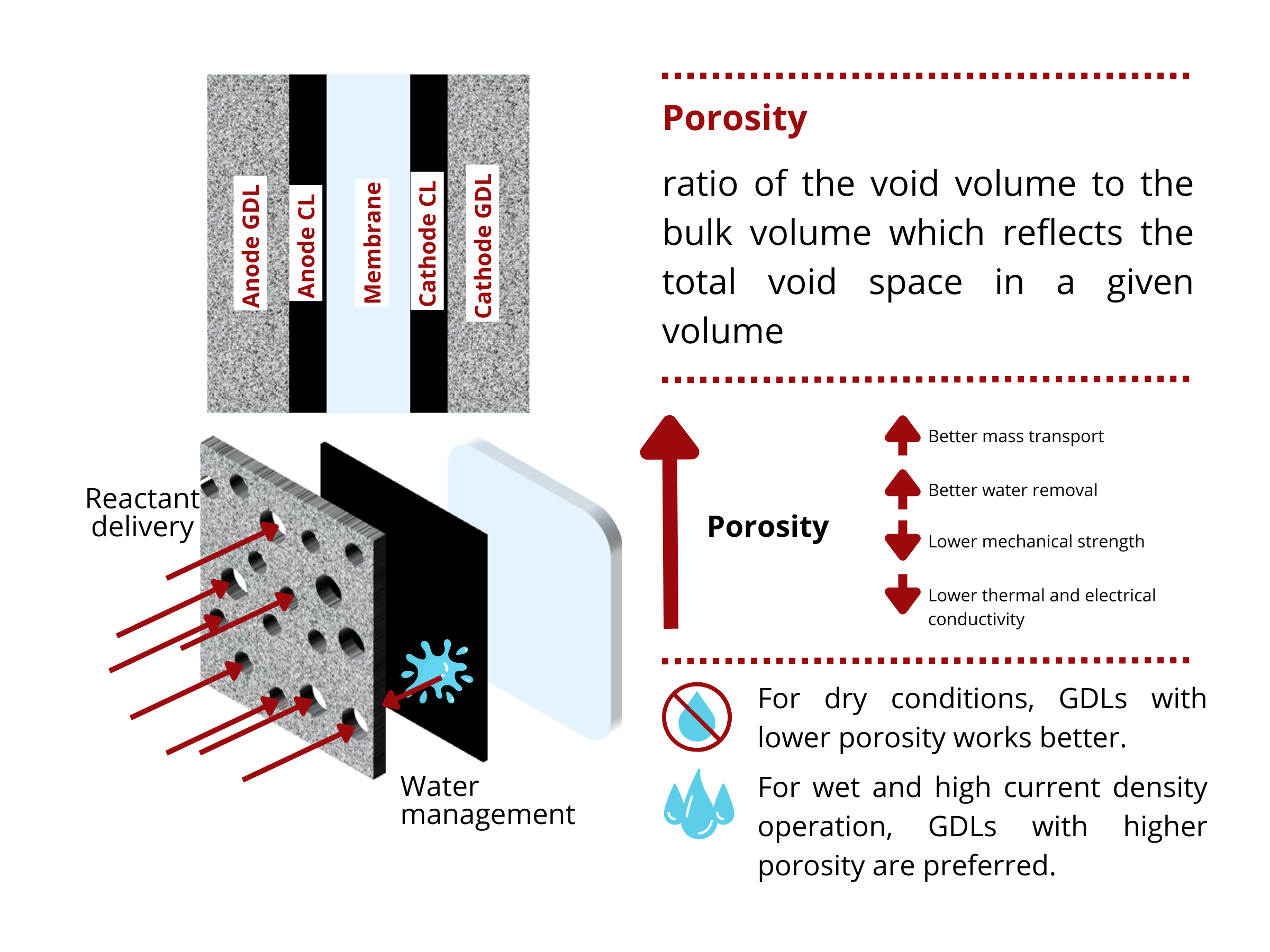
There is no “one size fits all” solution for all water electrolyzer and fuel cell designs. Depending on the cell design and operating conditions, there exists an optimal porosity that balances the mass transport, electrical, thermal, and mechanical properties of the GDL. For example, for high current density applications and wet conditions, GDLs with high porosity are desired. However, when the device is operated at dry conditions, GDLs with relatively lower porosities are recommended to ensure that the membrane is hydrated during the operation.
Effect of thickness on the properties of GDLs
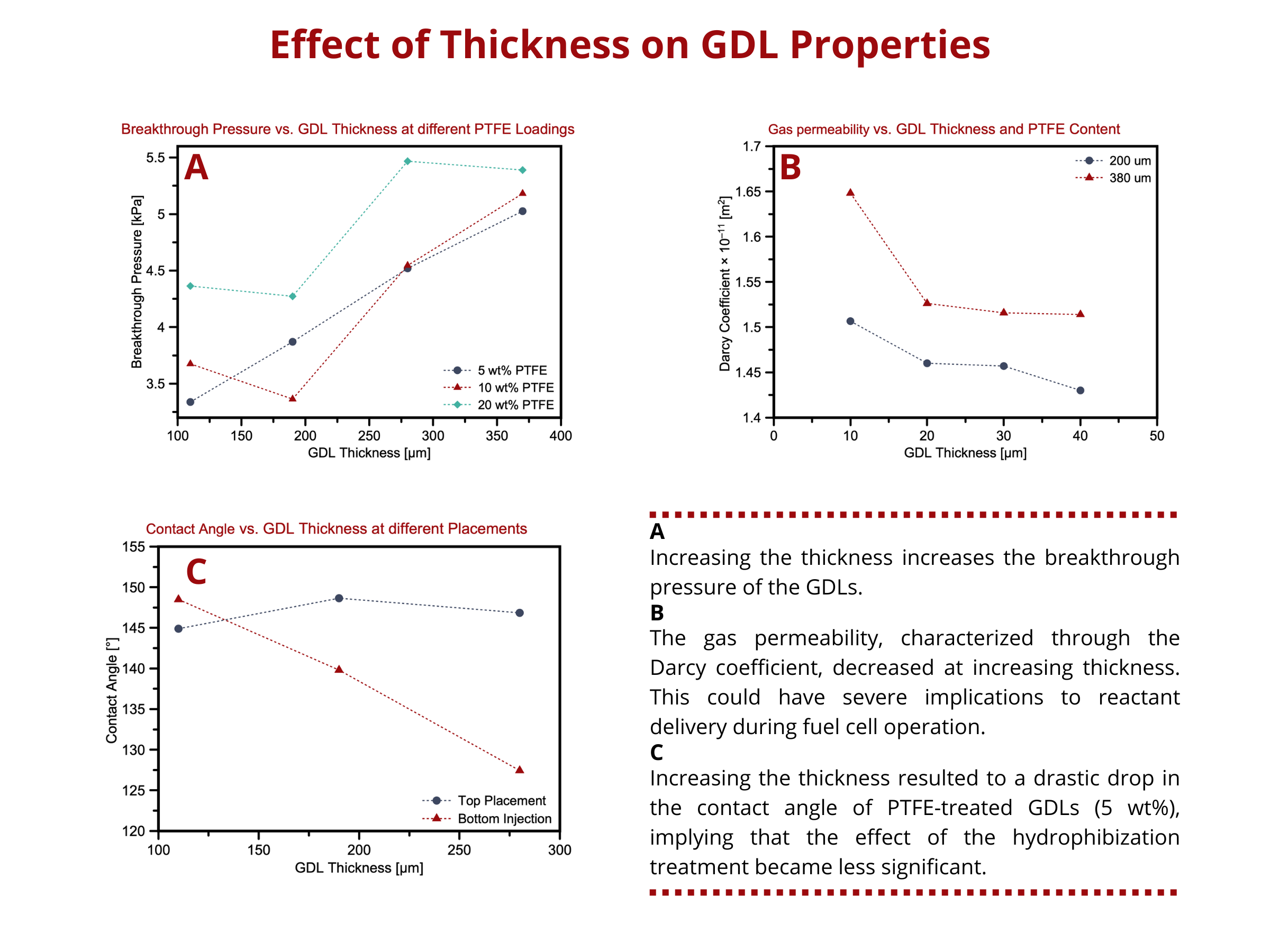
Similar to porosity, thickness affects the transport properties, as well as the electrical and thermal conductivity and mechanical integrity, of the GDLs. How does the thickness of GDLs affect its other properties? A more in-depth discussion on this topic can be found in our blog article (Why do fuel cells use thin GDLs?) but still, here’s a summary. Increasing thickness tends to increase the water breakthrough pressure and water saturation of the GDL. Thicker GDLs have longer path lengths for water diffusion, which increases the resistance to water penetration and pressure to pass through the GDL. As for the water saturation level, thicker GDLs often have high surface areas within its porous structure, allowing water to be absorbed at more sites. As a consequence of longer diffusion paths in thick GDLs, the through-plane transport of reactants and water decreases, whereas the in-plane mass transport increases, which can aid in the uniform distribution of reactants under the ribs of the GDLs. On top of the decreasing through-plane mass transport capabilities, increasing the thickness also reduces the effect of hydrophobization treatments on the GDLs. Hydrophobization treatments are performed to improve the water removal capacity of GDLs, improving its gas transport properties and preventing water accumulation in the stack.
Again, are thick GDLs suitable for all fuel cell and water electrolyzer applications? Not always. An optimum thickness exists that balances the transport performance and other properties of GDLs. What situations will require thick GDLs? Thin GDLs?
Thick GDLs with high water saturation levels are suitable for dry operating conditions. That way, the membrane is always hydrated, retaining its ionic conductivity and maintaining the good performance of the cell. Thick GDLs are also found appropriate to be used with bipolar plates with interdigitated flow channel design. As previously discussed, through-plane transport decreases with increasing thickness. To circumvent this when using thick GDLs, interdigitated flow-field geometries help. This bipolar plate design does not have a continuous diffusion path from the feed to the exhaust point. The channels have dead-ends, which forces gas transport through the GDL to the catalyst layer. This configuration also facilitates the removal of water, effectively balancing with the high water retention of thick GDL.
On the other hand, thin GDLs that have better water removal capability than thick GDLs are best used in wet operating conditions and high current densities. They have also been found to be effective when used in combination with bipolar plates with parallel flow channels. In this design, multiple parallel channels run from the inlet to the outlet. Parallel flow channels are designed to reduce the hydraulic resistivity of the bipolar plate. This implies that there is less resistance in fluid flow, which helps in the water management in the stack.
The relationship between structural properties and the performance is not always linear nor universal. The properties can vary depending on the end-use and the operating conditions they are being subjected to. Contact us and our team is ready to discuss your application in detail to find the appropriate GDL for your unique applications.