MCP-5000 | Motor Coating Powder
- Green Color
- High Edge Coverage
- Insulation Class B
Product Description
LINQSOL MCP-5000 is a green epoxy coating powder with good heat resistance and electrical insulation. MCP-5000 is suitable for motor and rotor coating, also coil end encapsulation. With its low pick-up temperature and quick pick-up rate, MCP-5000 builds up quickly.
LINQSOL MCP-5000 has high hardness, great edge coverage (55%), a high recovery rate, and is able to produce 15% more units compared to competitive products, with the same amount of powder. It comes into different arrangements with various particle size distributions (PSD) from 150um down to 38um. Please check the table in the additional information section.
Key Features:
- Comparable with DK7-0953M
- Good adhesion to copper
- Fast curing and high powder build rate
- Excellent edge coverage, hardness, and cut-through resistance
- Applicable in electrostatic fluidized bed
Recommended Coating Temperature:
- 200 °C x 15 min
Technical Specifications
General Properties | |||||
Color Color The color | green | ||||
Specific Gravity Specific Gravity Specific gravity (SG) is the ratio of the density of a substance to the density of a reference substance; equivalently, it is the ratio of the mass of a substance to the mass of a reference substance for the same given volume. For liquids, the reference substance is almost always water (1), while for gases, it is air (1.18) at room temperature. Specific gravity is unitless. | 1.60 | ||||
Chemical Properties | |||||
Water Absorption | 0.6 (boil 2h) % | ||||
Electrical Properties | |||||
Breakdown Voltage Breakdown Voltage Breakdown voltage is the minimum voltage necessary to force an insulator to conduct some amount of electricity. It is the point at which a material ceases to be an insulator and becomes a resistor that conducts electricity at some proportion of the total current. After dielectric breakdown, the material may or may not behave as an insulator any more because of the molecular structure alteration. The current flow tend to create a localised puncture that totally alters the dielectric properties of the material. This electrical property is thickness dependent and is the maximum amount of voltage that a dielectric material can withstand before breaking down. The breakdown voltage is calculated by multiplying the dielectric strength of the material times the thickness of the film. | 25000 V | ||||
Volume Resistivity Volume Resistivity Volume resistivity, also called volume resistance, bulk resistance or bulk resistivity is a thickness dependent measurement of the resistivity of a material perpendicular to the plane of the surface. | 1.0x1016 Ohms⋅cm | ||||
| |||||
Mechanical Properties | |||||
Edge Coverage | >55 % | ||||
Impact Strength | 500 mm | ||||
| |||||
| |||||
| |||||
Thermal Properties | |||||
| |||||
| |||||
Glass Plate Flow Glass Plate Flow Glass plate flow determines the flow distance of thermosetting epoxies, resins or coating powders on a smooth inclined glass surface in a certain time and temperature. This value is the distance in millimetres from the upper point of the original position of the pellet to the point of extreme flow. Typically measured at 150°C but please check the TDS for more info | 12~18 (@150°C, 60°, 2g) mm | ||||
Glass Transition Temperature (Tg) Glass Transition Temperature (Tg) The glass transition temperature for organic adhesives is a temperature region where the polymers change from glassy and brittle to soft and rubbery. Increasing the temperature further continues the softening process as the viscosity drops too. Temperatures between the glass transition temperature and below the decomposition point of the adhesive are the best region for bonding. The glass-transition temperature Tg of a material characterizes the range of temperatures over which this glass transition occurs. | 110 °C | ||||
|
Additional Information
MCP 5000 - Particle Size Distribution Options
Particle size | Option A | Option B | Option C | Option D | Unit |
150um | 0 - 3 | 0 - 3 | 0 - 1 | 0 - 1 | % |
150 - 106um | 5 - 20 | 10 - 20 | 0 - 3 | 0 - 8 | % |
106-38 um | 45 - 75 | 55 - 75 | 65 - 85 | 36 - 70 | % |
38um | 20 - 40 | 15 -25 | 10 - 25 | 30 - 55 | % |
The end properties are identical. PSD is the only variable
Industrial motors include power tools, home appliances and industrial motors. In automotive, motors are used for enclosures, windshield wipers, seat adjusters, window lifts and fuel pumps, quality cars can have up to 130 motors. An electric motor is made by wrapping an electric current around a magnetic core, and these two must be insulated from each other. This can be done by using insulating epoxy coating powder. Epoxy coating powders is widely used due to the advantages of efficiency and reliability. Check our Application Page Slot Insulation for more details.
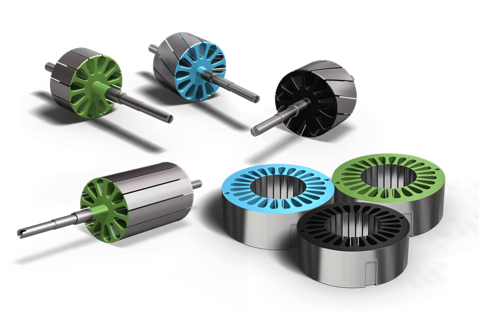
Insulation Epoxy Coating Powder Requirements
Great Performance
- Excellent edge coverage
- High cut through resistance temperature (minimum 300°C)
- High service temperatures and insulation class
- Capability to provide a range of thermal conductivities
Great Manufacturing Productivity
- High build rate enables faster coating line speed
- Outstanding adhesion to metal and plastics
- Low thickness required to achieve max performance
- Both induction and oven cure chemistries
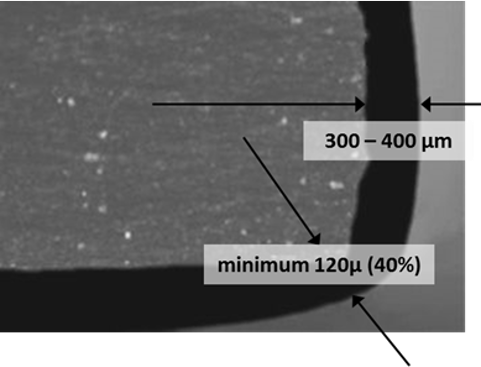
Epoxy coating powders is likely to be cut by copper wire at the edges. Minimum 300-400um coating thickness and 40% edge coverage ratio are required. MCP-5000 has the edge coverage of 55%.
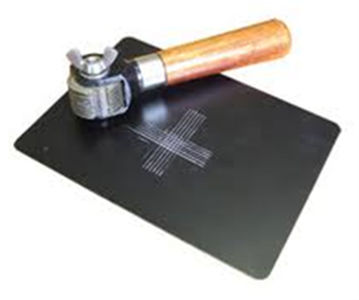
Coatings must have a perfect and consistent adhesion to the armature surface. MCP-5000 is tested great adhesion on coppper and Fe-Fe shear adhesion strength of more than 30 MPa.
Lower temperature and faster cure plus great electrostatic pickup increase productivity and save money, MCP-5000 has low melting temperature as 58°C, which allows quick pick up.
Storage
Store in a ventilated, dry, and clean environment below 25°C. Keep away from fire and heat sources. It is strictly forbidden to store in outdoor environments. At proper storage conditions, the product has a shelf life of 6 months.
Precautions
- Avoid long-term skin contact. Powder that touched the skin should be rinsed off quickly.
- During operation dust-proof masks should be used to avoid inhalation.
- Keep the oven temperature stable, so as not to affect the colour and quality of the coating due to excessive temperature deviation.
- The concentration of dust should be controlled within a safe range to avoid malfunction of the coating equipment.