OLS-1000HV | Liquid encapsulant - Two part Epoxy
- Excellent Mechanical Properties
- Halogen Free
- Rapid Cure
Product Description
OPTOLINQ OLS-1000HV is an optically clear spray-on halogen-free epoxy resin specifically designed for metal impregnation and LED lamps packaging applications. This halogen-free resin offers exceptional performance, combining good outgassing properties and extended service life at room temperature with rapid curing at medium temperatures.
OPTOLINQ OLS-1000HV produces cured products with outstanding mechanical strength, excellent electrical performance, superior high-temperature resistance. OLS-1000HV boasts of its low internal stress performance during reflow soldering processes due to its optimized modulus. It is a reliable choice for high-quality through-hole packages requiring uniform high-light transmittance.
OPTOLINQ-1000HV is available with infused visible light-blocking dyes with cutoff wavelengths at 700 nm, 750 nm, and 835 nm. See OCF blockers available for OPTILINQ Products.
Technical Specifications
General Properties | |||||
Appearance Appearance Appearance at room temperature. | Light purple | ||||
Density (g) | 1.15 g/cm3 | ||||
Mix Ratio Mix Ratio The amount of a constituent divided by the total amount of all other constituents in a mixture | 1:1 | ||||
Pot Life Pot Life Pot life is the amount of time it takes for the viscosity of a material to double (or quadruple for lower viscosity materials) in room temperature after a material is mixed. It is closely related to work life but it is not application dependent, less precise and more of a general indication of how fast a system is going to cure. | 4 hours | ||||
Physical Properties | |||||
Viscosity Viscosity Viscosity is a measurement of a fluid’s resistance to flow. Viscosity is commonly measured in centiPoise (cP). One cP is defined as the viscosity of water and all other viscosities are derived from this base. MPa is another common unit with a 1:1 conversion to cP. A product like honey would have a much higher viscosity -around 10,000 cPs- compared to water. As a result, honey would flow much slower out of a tipped glass than water would. The viscosity of a material can be decreased with an increase in temperature in order to better suit an application | 840 mPa.s | ||||
Chemical Properties | |||||
Water Absorption | 0.3 % | ||||
Electrical Properties | |||||
Breakdown Voltage Breakdown Voltage Breakdown voltage is the minimum voltage necessary to force an insulator to conduct some amount of electricity. It is the point at which a material ceases to be an insulator and becomes a resistor that conducts electricity at some proportion of the total current. After dielectric breakdown, the material may or may not behave as an insulator any more because of the molecular structure alteration. The current flow tend to create a localised puncture that totally alters the dielectric properties of the material. This electrical property is thickness dependent and is the maximum amount of voltage that a dielectric material can withstand before breaking down. The breakdown voltage is calculated by multiplying the dielectric strength of the material times the thickness of the film. | 20 V | ||||
Surface Resistivity | 28000000000000000 Ohms/sq | ||||
Volume Resistivity Volume Resistivity Volume resistivity, also called volume resistance, bulk resistance or bulk resistivity is a thickness dependent measurement of the resistivity of a material perpendicular to the plane of the surface. | 6.4x1016 Ohms⋅cm | ||||
Mechanical Properties | |||||
| |||||
Thermal Properties | |||||
| |||||
Glass Transition Temperature (Tg) Glass Transition Temperature (Tg) The glass transition temperature for organic adhesives is a temperature region where the polymers change from glassy and brittle to soft and rubbery. Increasing the temperature further continues the softening process as the viscosity drops too. Temperatures between the glass transition temperature and below the decomposition point of the adhesive are the best region for bonding. The glass-transition temperature Tg of a material characterizes the range of temperatures over which this glass transition occurs. | 137 °C |
Additional Information
OPTOLINQ OLS-1000 Series | Visible Light Blocking Capabilities
OLS-1000LV and OLS-1000HV are developed with compatibility to various dyes with different onset transmittance as shown.
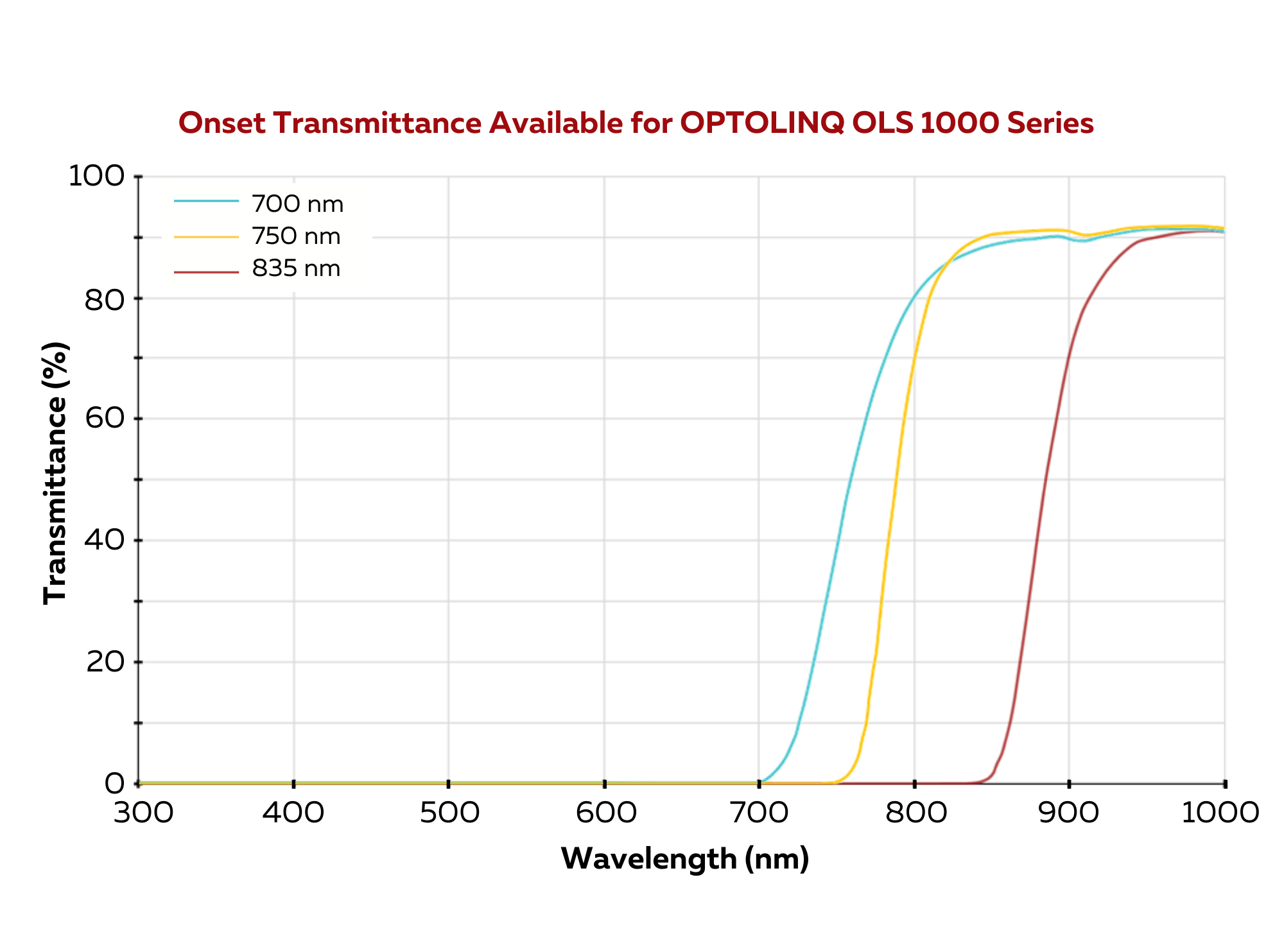
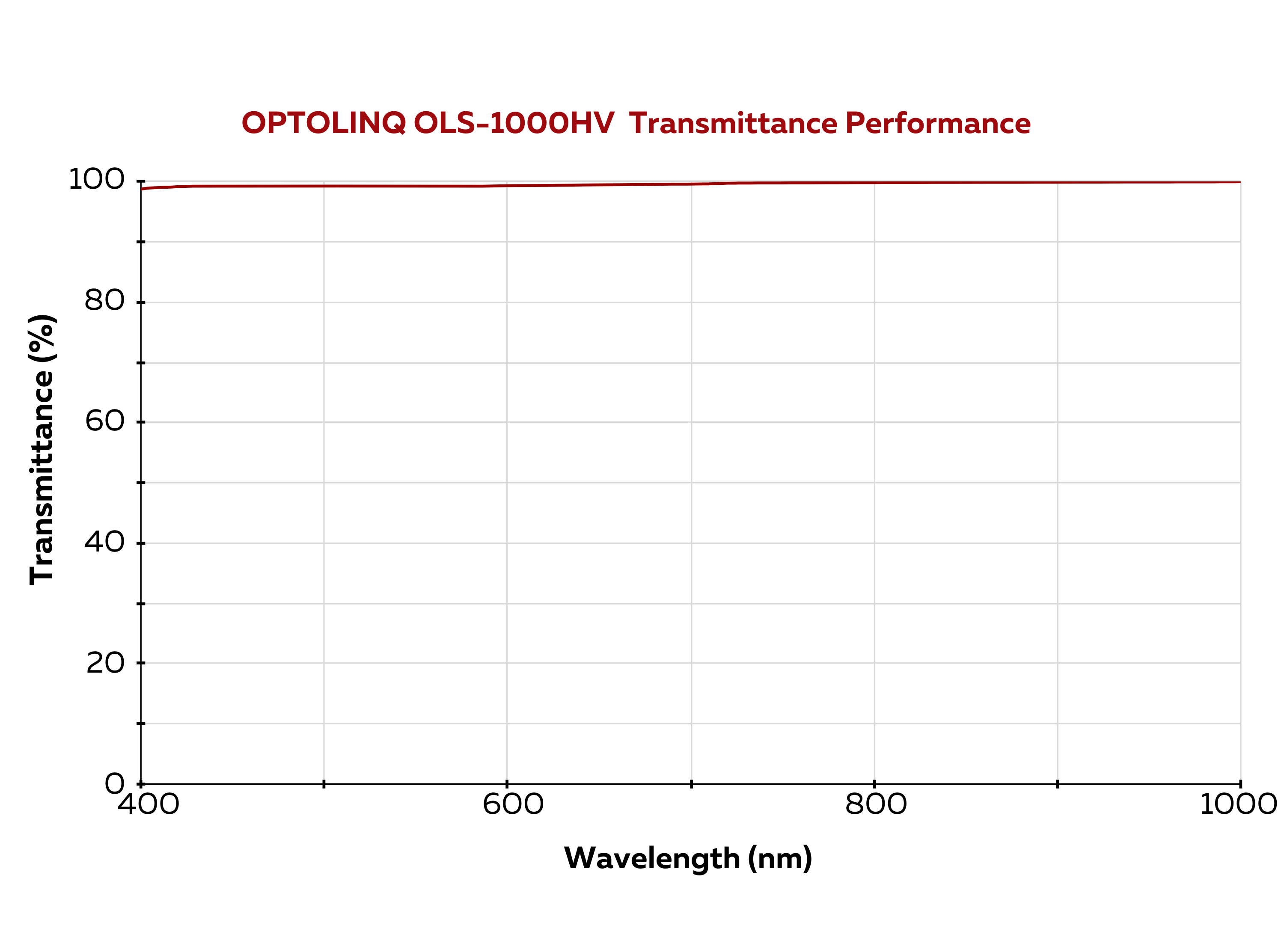
Processing Instructions:
- Pre-heat Part A at 45~60°C for a maximum of 24 hours.
- Mix components A and B and stir uniformly.
- Defoam the mixture for 5 minutes.
- Curing conditions (Determine according to the specific needs of the product, following conditions are for reference only.
- Cure at 130 - 145°C/1 - 1.5 hrs for encapsulation thickness less than 2mm.
- Cure at 125 - 130°C/4 - 5 hrs. for encapsulation thickness greater than 2mm.
Precautions:
- For optimal results, use the mixture within 6-8 hours after combining components A and B. Delaying application may lead to an undesirable increase in viscosity.
- Bake the molded package as soon as possible to prevent degradation by moisture.
- Pre-heating component A at 45~60°C can reduce viscosity, but excessively high temperatures will shorten the its pot life.
- Store the curing agent (component B) in sealed jars to prevent moisture absorption and sedimentation.
- When adding light diffusers, adjust the curing agent accordingly (e.g., A:B:Diffuser = 100:105:10).
- Preheat color additive agents at 60-90°C, ensuring complete dissolution.
- Avoid skin and eye contact. In case of contact, rinse thoroughly with soap (for skin) or clean water (for eyes), and seek medical attention if needed.
- Maintain a clean and ventilated workplace, using extraction trunks when necessary.
- Wear appropriate protective equipment and minimize direct contact with the human body. Refer to the Safety Data Sheet (SDS) before use.
Please note that the provided information is based on available data and typical conditions. For specific applications and detailed test results, refer to the actual test data and conduct appropriate certifications.
Storage and Handling
Store in a ventilated, dry, and clean environment below 25°C. Keep away from fire and heat sources. It is strictly forbidden to store in outdoor environments. At proper storage conditions, Part A has a shelf life of 6 months and Part B a shelf life of 3 months. Shelf life can be extended by using cold storage.