PTM 7000-SP | Phase Change Paste
- 0.06 Thermal Impedance
- 6.5 Thermal Conductivity
- Paste form
Product Description
PTM7000-SP is a viscous, stencil printable paste version of PTM7000. It is designed to minimize thermal resistance at interfaces and maintain extremely stable performance through reliability testing required for long product life applications. As with all Phase change materials, it has stable Thermal Impedance across accelerated aging tests and does not display bleed, pump or flow out. PTM7XXX product line has the highest Thermal conductivity and lowest thermal impedance out of the entire PTM Series.
PTM7000-SP has a Thermal conductivity of 6.5 (W/m·K) depending on the bondline thickness and is based on a robust polymer PCM structure that exhibits excellent wetting properties during typical operating temperature ranges, resulting in very low surface contact resistance. This proprietary material has a maximum particle size of 50um, provides superior reliability and maintains low thermal impedance (0.06) , making it desirable for high-performance integrated circuit devices.
Please keep in mind that 7XXX is a Product Series. Base 7000 performs on the baseline of the stated properties while PTM7900 and PTM7950 are the highest performing materials of this product line reaching 8.5 W/m·K and 0.04 TI.
Solvent Drying time:
- 2.5 hours @ 23°C
- 2.5mins @ 100°C
Technical Specifications
General Properties | |
Specific Gravity Specific Gravity Specific gravity (SG) is the ratio of the density of a substance to the density of a reference substance; equivalently, it is the ratio of the mass of a substance to the mass of a reference substance for the same given volume. For liquids, the reference substance is almost always water (1), while for gases, it is air (1.18) at room temperature. Specific gravity is unitless. | 2.3 |
Thickness range | 0.20 - 1.00 mm |
Physical Properties | |
Viscosity Viscosity Viscosity is a measurement of a fluid’s resistance to flow. Viscosity is commonly measured in centiPoise (cP). One cP is defined as the viscosity of water and all other viscosities are derived from this base. MPa is another common unit with a 1:1 conversion to cP. A product like honey would have a much higher viscosity -around 10,000 cPs- compared to water. As a result, honey would flow much slower out of a tipped glass than water would. The viscosity of a material can be decreased with an increase in temperature in order to better suit an application | 120,000 mPa.s |
Electrical Properties | |
Volume Resistivity Volume Resistivity Volume resistivity, also called volume resistance, bulk resistance or bulk resistivity is a thickness dependent measurement of the resistivity of a material perpendicular to the plane of the surface. | 2.1x1014 Ohms⋅cm |
Thermal Properties | |
Thermal Conductivity Thermal Conductivity Thermal conductivity describes the ability of a material to conduct heat. It is required by power packages in order to dissipate heat and maintain stable electrical performance. Thermal conductivity units are [W/(m K)] in the SI system and [Btu/(hr ft °F)] in the Imperial system. | 6.5 W/m.K |
Thermal Impedance | 0.06 °C·cm²/W |
Additional Information
When choosing a printable paste it is important to understand the process parameters and limitations.
That's why we ask, when you contact us, to include the following information:
- What is your print thickness?
- How long is your printing time and working window?
- What is your drying step after printing?
- Temperature (Room temperature or something else?)
- Time
- Do you have any viscosity limitations in the printing process?
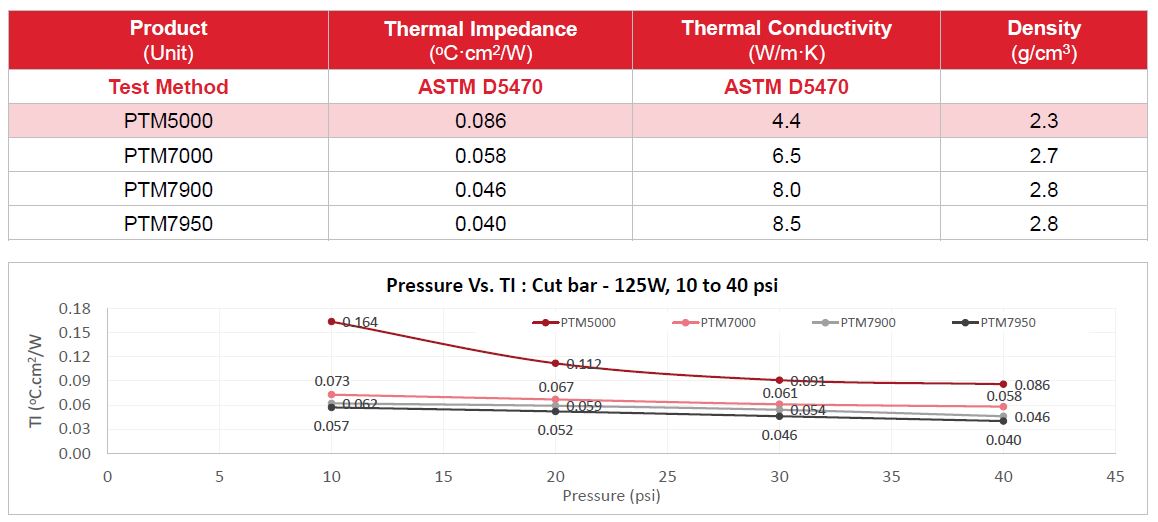
PTM7XXX Series - Pressure vs Thermal Impedance
PTM7XXX Series vs Competition comparison
What is the shelf-life of the PTM7000-SP?
Shelf-life refers to the amount of time the material can be kept when stored under the recommended storage conditions. The shelf-life of the PTM7000-SP is 12 months when kept below 25°C and with less than 20% relative humidity (RH).
How is the material prepared prior to use?
If the material is supplied in 280cc cartridges, then the PTM7000-SP can be dispensed directly onto the stencil. If the PTM7000-SP is supplied in 1kg can, then it is best to mix or roll the material prior to each use. "Rolling" involves simply having the material "self-mix" which the can is being rolled (for this there is standard "jar roller" equipment).
Any recommended printing equipment, squeegees etc?
DEK TQ stencil printers, currently made by ASM Pacific have been proven to work well. DEK equipment has built-in stencil cleaners. ASM also has recommended consumables to be used for printing. Rubber squeegee blades need to be cleaned every hour if they are not used continuously.
How should I transfer it to the dispensing tanks?
This question usually arises from customers that wonder whether to pour or pump the material. Our current customers are all pouring PTM7000 into the dispense tanks.
Which packaging, the 1kg can or the 280cc aluminum cartridge is best recommended to use?
This depends on how you plan to apply the material. If you plan to dispense from a cartridge (hardly anyone dispenses) using a nozzle, then a cartridge is recommended. Also, if you plan to do much smaller batch sizes (ie less then 1kg at a time), then 280cc cartridges are better because you will lose less material per use. Printing, however, is a high throughput process. On any print cycle you will need at least 100cc of material on the stencil during printing which can coat many pieces per stroke. You will easily use up 280cc of material per shift during printing.
What is the potlife of the PTM7000-SP?
Potlife (also referred to as work life) refers to the amount of time the material can be still be used after it has been opened. When kept in the 1kg cans, the potlife is 12 hours from the time the can is opened. When the lid is replaced and the can is closed again, you will have 48 hours to use the balance of the material. The remaining material should also be remixed (or re-rolled on a jar roller) prior to use.
Similarly, in the 280cc cartridge, the potlife is 24hrs if dispensed from the cartridge directly. If the cartridge is opened to add material to the printer and then closed again, the balance of the material should be used within 24-36 hours.
The work life of this phase change paste is 1 hour at room temperature, for the material that has been poured into the printer. If the solvents are allowed to evaporate for more than that, you won't be able to properly print. That's a sign that the material has gone bad. Please note that the material is optimized for printing and not for dispensing.
What is the thickness difference before and after drying?
It is typical to lose approx. 20% thickness due to solvent drying. For example, a 300µm (0.3mm) thickness stencil of wet PTM7000-SP will result in 240µm (0.24mm) after drying. If the thickness loss is more than 20%, then the can was not stirred or rolled and it is indicative of mixing issues prior to dispensing them on the printing equipment.
What is Homogeneity?
Homogeneity is caused by filler settling down during long periods of storage, if refrigerated, filler settling is much slower as compared to storing at room temperature. Refrigerated material should be thawed for 4hours before using.