Lithium Ion Batteries
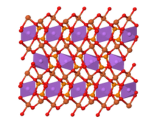
Lithium iron phosphate (LFP)
LFP is widely used in automotive applications due to its high power capability, making it ideal for handling rapid charging, such as regenerative braking, and delivering quick bursts of acceleration. It’s also one of the more cost-effective chemistries, as iron phosphate is abundant and inexpensive. LFP is considered safer than some other chemistries because it is more tolerant of overcharging and high temperatures. However, it has a lower energy density, which means it stores less energy per unit weight, resulting in less severe consequences in the event of a failure.
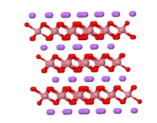
Lithium cobalt oxide (LCO)
LCO is commonly used in consumer electronics like smartphones, cameras, and laptops, where high energy density and long cycle life are critical. While LCO excels in these areas, it has drawbacks, including instability at higher temperatures and a tendency to become reactive above 130 °C, which can lead to thermal runaway. Due to these safety concerns and its higher cost (owing to the significant cobalt content), LCO is less favored for large-scale applications, such as automotive use, though it remains a mainstay in small electronics.
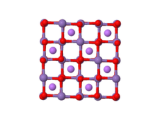
Lithium mangenese oxide (LMO)
LMO is known for its high energy and power capabilities, making it suitable for applications where long run time is needed, such as in portable power tools. However, LMO has a shorter cycle life, meaning it doesn’t last as long under repeated charging and discharging. This limitation makes it less suitable for automotive applications where longevity is crucial, but it remains valuable in scenarios where immediate power and energy are prioritized over long-term durability.
Anode
In lithium-ion batteries, the anode plays a critical role in determining the performance and efficiency of the cell. Currently, most anodes are made from graphite or variations of carbon, such as soft or hard carbons. Graphite is particularly favored because of its stable structure and ability to intercalate lithium ions effectively. The quality of the graphite used can significantly influence the battery's behavior, with high-grade graphite offering better conductivity and durability. However, research is constantly pushing the boundaries to explore new materials that could enhance battery performance.
One such material is lithium titanate (LTO), which has gained interest due to its high power density and ability to operate at lower temperatures. While LTO anodes offer some advantages, including faster charge times and better thermal stability, they come with the drawbacks of a lower nominal voltage and higher cost compared to traditional options like nickel manganese cobalt (NMC) or lithium iron phosphate (LFP) cells. Despite these challenges, LTO is being actively developed for use in specific applications, such as micro-hybrid electric vehicles, where its benefits can outweigh its limitations. Meanwhile, other promising materials like silicon and tin are under investigation, though they face significant hurdles, such as volumetric expansion during cycling, which impacts their commercial viability. As research continues, these new materials could eventually lead to significant advancements in lithium-ion battery technology.
Separator
In lithium-ion batteries, the separator plays a key role in ensuring the cell's safety and efficiency. It is usually a thin layer made from plastic or ceramic materials that physically keeps the anode and cathode apart. This separation is critical because if these two electrodes were to touch, it could cause an internal short circuit, leading to potential cell failure.
The separator must be robust and chemically resistant, as it needs to endure the harsh, often corrosive, hydrocarbon-based electrolytes found within the battery. Although it may seem delicate, the separator is essential for maintaining the battery's structural integrity and safety. It prevents the electrodes from coming into direct contact while still allowing ions to flow freely during the battery's operation. Therefore, the design and choice of materials for the separator are crucial elements that influence the overall performance and reliability of lithium-ion batteries.
Most Common Separator Materials for Lithium Ion Batteries
The most common materials used for separators in lithium-ion batteries are polypropylene (PP) and polyethylene (PE) plastics. These materials are chosen for their unique properties that balance functionality and safety.
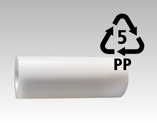
Polypropylene (PP) is a popular choice due to its excellent chemical stability and mechanical strength. It is resistant to the electrolyte solutions used in lithium-ion batteries, which helps prevent degradation over time. PP also has a high melting point, which makes it suitable for applications where thermal stability is important.
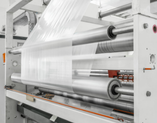
Polyethylene (PE) is valued for its flexibility and low cost. PE separators often have a slightly lower melting point compared to PP, which can be advantageous in some designs where a lower temperature threshold is desired.
Together, these plastics are designed to be porous, allowing lithium ions to pass freely between the anode and cathode during the charge and discharge cycles. The porous structure ensures that the flow of lithium ions is not obstructed, which is crucial for maintaining the battery’s efficiency and capacity.
Challenges in Separator Materials for Lithium Ion Batteries
The thermal stability of these separators can be a concern. At elevated temperatures, typically above 90 to 110 °C, the plastic material can start to shrink or melt. This can lead to a situation where the separator loses its effectiveness, potentially causing internal short circuits within the battery. To address this issue, some manufacturers use multilayer separators, combining PP and PE in a trilayer configuration. In such designs, the middle PE layer is engineered to melt at a lower temperature, which helps in managing high-temperature scenarios by closing the pores and preventing short circuits, while the outer PP layers remain intact until higher temperatures are reached. This design approach enhances safety and helps ensure the longevity and reliability of the battery under various operating conditions.
Ceramic (High Purity Alumina) Coatings to Improve Thermal Stability of Separator Materials
Some lithium-ion cell manufacturers are increasingly incorporating ceramic-layered separators into their designs to enhance both safety and performance. Ceramic separators offer significant advantages over traditional plastic separators, particularly in terms of thermal stability and safety.
Ceramic materials can withstand much higher temperatures than polypropylene (PP) or polyethylene (PE), making them more effective in preventing thermal runaway and ensuring battery safety during extreme conditions, such as nail penetration tests. In these tests, the battery is subjected to physical damage that could potentially cause a short circuit or thermal event. Ceramic separators are more robust under such stress, reducing the risk of catastrophic failures.
Additionally, ceramic-layered separators contribute to improved power rate capability by lowering the internal resistance of the cell. This reduction in resistance allows for more efficient ion transport between the anode and cathode, which enhances the battery's performance and efficiency. As a result, cells with ceramic separators can deliver higher power output and maintain better performance under high-current conditions, making them suitable for applications requiring rapid discharge and charge cycles.
High-purity Alumina (HPA) Grades of Lithium Ion Battery Separator Coatings
Currently, 4N grade HPA is commonly used as a ceramic coating lithium ion battery separators. Higher 4N+ grade contains >99.99% alumina. High purity is needed to minimize metallic cation impurities and metal impurities, which should be less than a few ppm. Impurities can leach into the electrolyte, form dendrites, or serve as nuclei that accelerate dendrite formation. Metals in the ceramic layer, introduced either through raw materials or the manufacturing process, are a source of short-circuits due to their proximity to the polymer membrane. Higher grades, 5N or 6N, are offered and carry premium pricing over 4N. Various process techniques allow producers to consistently meet 4N+ grade spec, but at relatively high overall product cost. At 4N grade, HPA has under 100 ppm of total impurities.
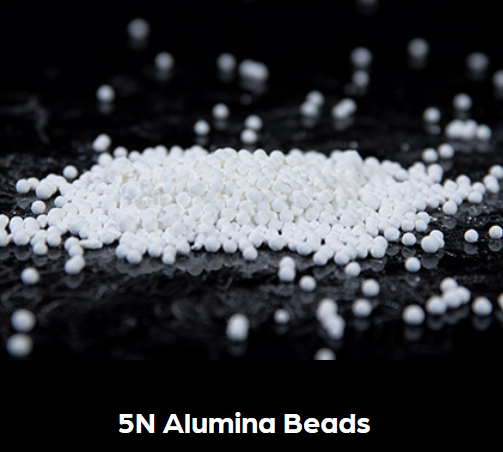
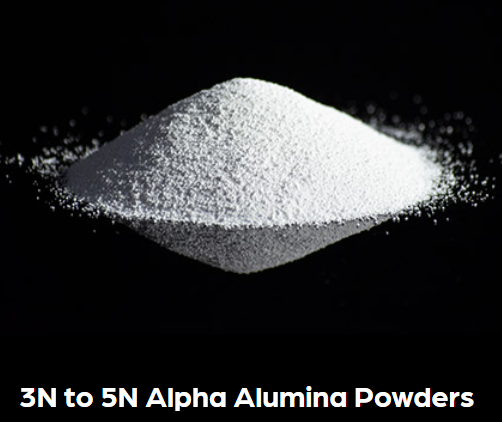
Frequently Asked Questions about Lithium Ion Batteries
Lithium-ion batteries are generally safe when used and handled properly. However, they can pose safety risks if damaged, overcharged, or exposed to extreme temperatures. Manufacturers include safety features like thermal fuses and pressure-sensitive vents to reduce the risk of thermal runaway and fires.
What are the key considerations for using lithium-ion batteries in high-power applications?
When using lithium-ion batteries in high-power applications, several key factors must be considered for optimal performance and safety. The electrolyte needs high ionic conductivity (greater than 10⁻³ S/cm) to ensure efficient ion transport. The solid-electrolyte interface (SEI) on the graphite anode must be stabilized to prevent capacity loss, and the lithium salt must remain thermally stable against organic solvents, especially at high temperatures. The cathode material should not dissolve in the electrolyte to avoid capacity reduction and safety risks. Lastly, the battery must tolerate rapid charging and discharging to prevent overheating or short circuits. These considerations are crucial for the safe and effective use of lithium-ion batteries in high-power settings.
Yes, lithium-ion batteries can be recycled to recover valuable materials such as lithium, cobalt, nickel, and copper. Recycling helps reduce the environmental impact of battery disposal and conserves natural resources. However, proper recycling requires specialized facilities due to the complexity of the battery's components.
What materials are recovered by specialized recyclers from lithium-ion batteries?
Specialized battery recyclers extract several valuable materials from lithium-ion batteries, focusing mainly on cobalt, nickel, and manganese. These metals are crucial due to their high value and role in manufacturing new batteries, with cobalt enhancing energy density and stability, and nickel and manganese improving performance and longevity. Lithium is also recovered but often requires further processing for reuse. Additionally, recyclers recover copper and aluminum, used in electrical connections and current collectors. This recycling process is vital for reducing the environmental impact of battery production, conserving resources, and minimizing the need for new mining, thus supporting the sustainability of battery technology and reducing its ecological footprint.