Redox Flow Batteries
Electrodes for Redox Flow Batteries
In redox flow batteries, energy is stored in solutions that flow through the system, with their capacity being directly related to the volume of the solution tanks. This battery type is made up of two electrodes separated by a membrane. The energy storage and conversion processes occur on the surface of these electrodes, making the properties of the electrode materials critical to the battery's performance.
Carbon materials, such as graphite felt and graphitized carbon paper, are typically used as electrodes in redox flow batteries. These materials are chosen for their excellent conductivity, chemical stability, and high surface area. Several factors determine the performance of carbon electrodes in VRFBs:

The mass transfer of ions and protons in the pores of the carbon material, as well as the transport of electrons within the carbon structure, significantly affect the reaction rate. Efficient transport properties ensure that reactants reach the active sites quickly and that the generated electrons are efficiently collected and transported away from these sites.
Wettability
The wettability of the carbon electrode affects the penetration of the electrolyte into the pores, which in turn influences the accessibility of the active sites for the redox reactions. Improved wettability ensures better contact between the electrolyte and the electrode, enhancing the overall reaction kinetics.


Surface Area and Pore Structure
The surface area of the carbon material, along with its pore size distribution, directly impacts the number of active sites available for the redox reactions. A higher surface area provides more active sites, which can enhance the battery's capacity and efficiency.
Active Sites
The amount and nature of active sites on the carbon surface determine the charge transfer kinetics. An increase in the number of active sites can lead to a higher reaction rate, thereby improving the battery's charge-discharge efficiency and power density.

LINQCELL Graphite Felts are non-woven materials specifically engineered for use in redox flow batteries. GFP graphite felt series is made from high-quality polyacrylonitrile (PAN) fibers. These fibers are processed into a non-woven structure, which is then carbonized and graphitized. The result is a material with exceptional properties: it exhibits high electrical conductivity due to high-temperature treatment above 1000 °C, superior oxidation resistance, and excellent thermal stability. The non-woven structure of LINQCELL GFP provides flexibility and resilience, making it adaptable to various applications.
Product | Felt Type | Thickness [mm] | Basis Weight [g/m2] | Voltage Loss [mV] | Roll Width [cm] |
---|---|---|---|---|---|
GFP2000 | PAN Graphite | 2 | – | <35 | >40 |
GFP3000 | PAN Graphite | 3 | – | <35 | >40 |
GFP6500 | PAN Graphite | 6.5 | 550±100 | – | >90 |
Ion Exchange Membranes for Redox Flow Batteries
Ion exchange membranes serve as a separator between the cathode and anode compartments within the redox flow battery stack. Ideally, it should only allow non-vanadium ions to pass through, maintaining electrolyte purity and ensuring charge balance in the system.
Basically, the ion exchange membrane in redox flow batteries needs to do two things:
ALLOW ONLY SPECIFIC IONS (LIKE H+) TO MOVE THROUGH
The IEM must facilitate the transport of protons (H⁺) or other charge carriers to maintain high ionic conductivity and enable efficient charge transfer between the cathodic and anodic compartments.
BLOCK UNWANTED IONS
The membrane must act as a barrier to prevent vanadium ions (V²⁺, V³⁺, VO²⁺, VO₂⁺) from migrating between the positive and negative electrolyte compartments. Vanadium ion crossover disrupts electrolyte balance, leading to capacity fade and self-discharge, which reduce battery efficiency over time.
An ideal IEM should have the following key properties to ensure optimal performance in redox flow batteries:

IEMs must have high ionic conductivity, efficiently conducting the target ions to facilitate efficient charge transfer. Area-specific resistance (ASR) or ionic conductivity can be used as indicators of this property, with lower values reflecting better performance.
The membrane should exhibit high ion selectivity, meaning it should allow the desired ions to pass through while effectively blocking vanadium ions, thereby preventing crossover and maintaining electrolyte balance. This is measured by the selectivity ratio (S), which compares proton conductivity to vanadium ion permeability. Higher selectivity ratios indicate better selectivity.


Chemical stability is crucial, as the membrane must withstand the highly acidic and oxidative environment of the VRFB without degrading, especially due to vanadium ion attack. If the membrane degrades, it can lead to increased ion crossover, reducing efficiency and causing premature failure. Additionally, the material must resist physical and chemical damage over time to ensure a longer operational lifespan and consistent performance under demanding conditions.
LINQCELL VRB-MEM Membranes are perfluorinated cation exchange polymers in the acid H+ form produced through solution casting. This chemistry and manufacturing method provide several benefits, including high acid capacity and conductivity, enhanced crystallinity and tensile strength, reduced linear expansion and anisotropy, and an extended service life. These characteristics make LINQCELL VRB-MEM Membranes highly recommended for use as ion exchange membranes in redox flow batteries, particularly in all-vanadium flow batteries.
LINQCELL VRB-MEM Membranes are available in two standard thicknesses—50 µm (VRB-MEM50) and 75 µm (VRB-MEM75)—and can also be custom-fabricated to meet specific requirements. The maximum roll width is 75 cm.
Product | Type | Thickness [µm] | Conductivity [S/cm] | Available Acid Capacity [meq/g] | Water Content [%] |
---|---|---|---|---|---|
VRB-MEM50 | Cation exchange | 50 | 0.1 | 1 | 5 |
VRB-MEM75 | Cation exchange | 75 | 0.1 | 1 | 5 |
Gaskets for Redox Flow Batteries
Redox flow batteries operate under challenging chemical conditions, typically between 40°C and 60°C, using an electrolyte of dissolved salts in sulfuric acid. These conditions demand that all components of the battery, including gaskets, meet stringent performance criteria.
Gaskets are crucial in RFB stacks, yet their importance is often underestimated. They play a pivotal role in ensuring the mechanical integrity of the battery stack. The selection of appropriate gasket materials is essential to prevent cracks in bipolar plates and to maintain the structural integrity of the membrane. A well-chosen gasket must seal the stack effectively to manage cumulative tolerance effects during both design and operation.
The primary functions of gaskets in an RFB stack include:
- Sealing and Leakage Prevention: Gaskets must prevent leaks in both the anode and cathode areas, as well as in cooling plates.
- Compensation of Tolerances: They must accommodate dimensional changes during stack assembly caused by interactions with different stack components.
- Mechanical Integrity: Gaskets need to support the stack without causing damage to other components.
Given the diverse requirements and specific operating conditions of different RFB systems, gaskets must be highly customized for each stack manufacturer. This customization ensures that the gaskets can effectively support the mechanical and chemical demands of the battery stack, thereby enhancing the overall efficiency and longevity of the system.
Several materials are commonly used for gaskets in RFBs, each with distinct properties:
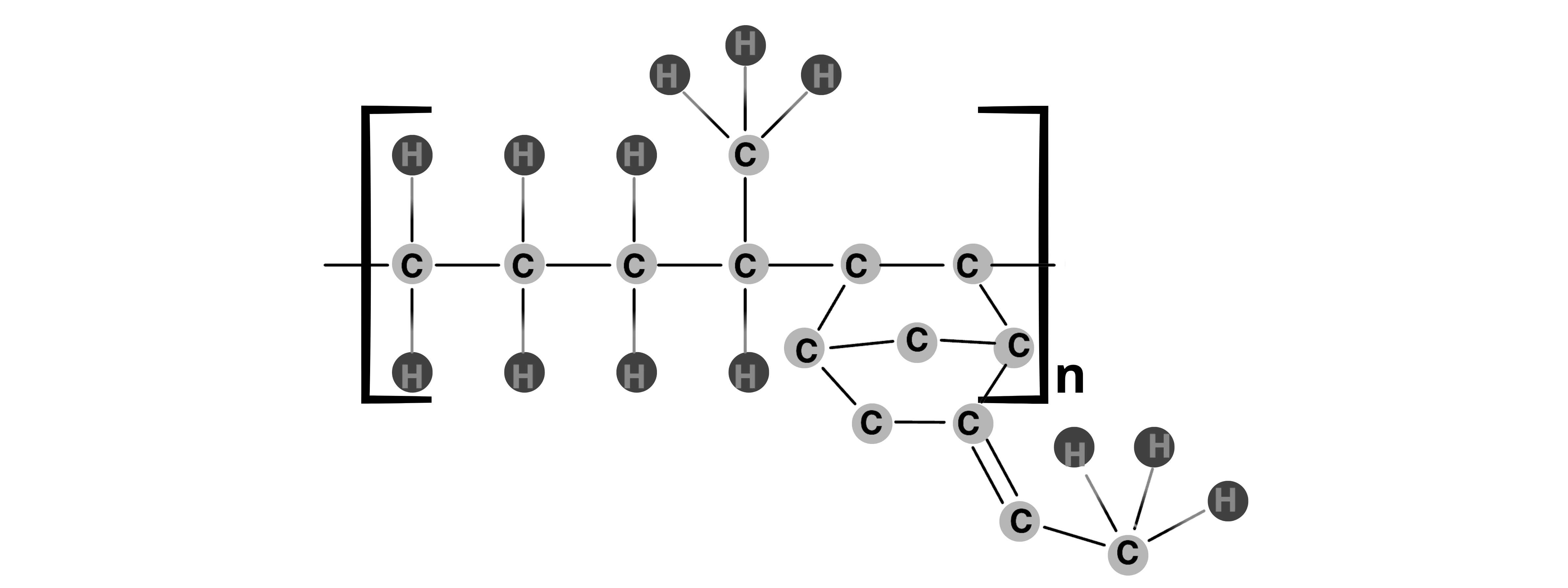
EPDM, a synthetic rubber from the 1960s, excels in redox flow batteries. Its flexible ethylene, propylene, and diene monomer composition ensures tight seals, resisting chemical damage and gas leaks. With high-temperature stability and low gas permeability, EPDM enhances performance and lifespan in harsh conditions.
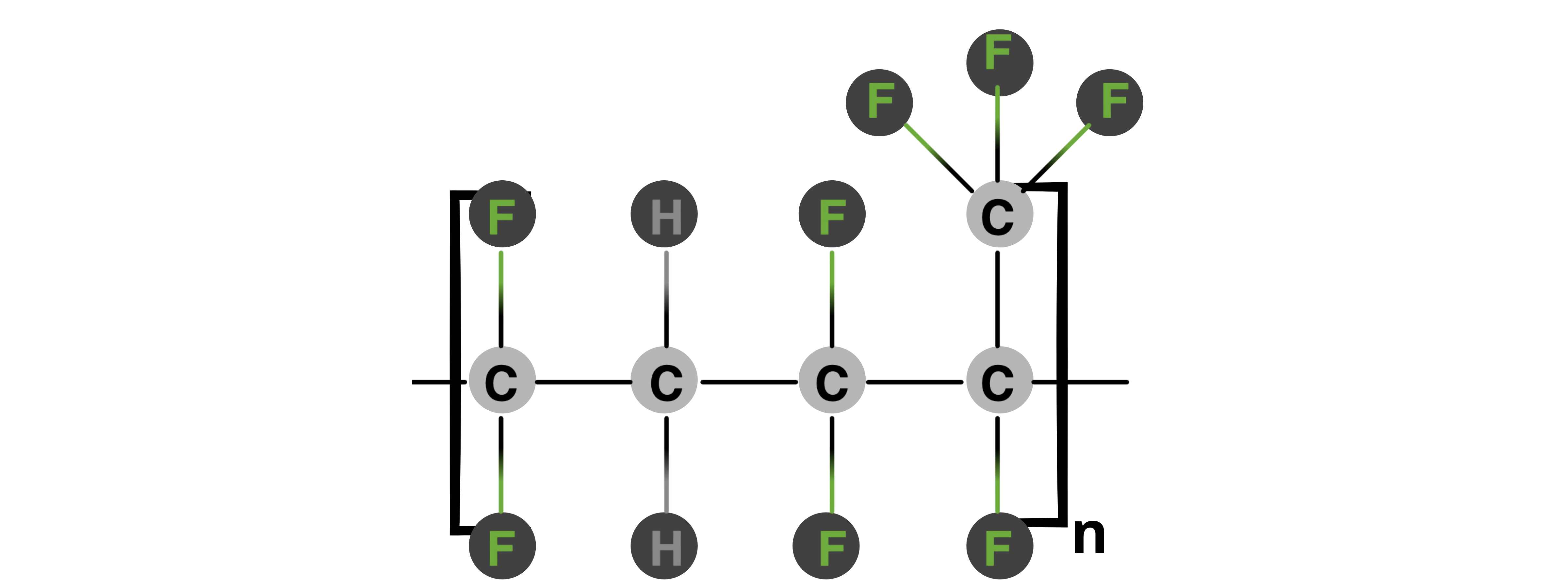
Fluorine Kautschuk Material (FKM)
FKM, or fluorinated rubber material, has high chemical resistance and high temperature stability (–20 °C to 250 °C). Made from fluorinated hydrocarbon polymers, FKM resists acids, bases, fuels, and solvents, ensuring reliability in demanding environments. Their flexibility and compression set resistance provide effective sealing under varying pressures and temperatures.
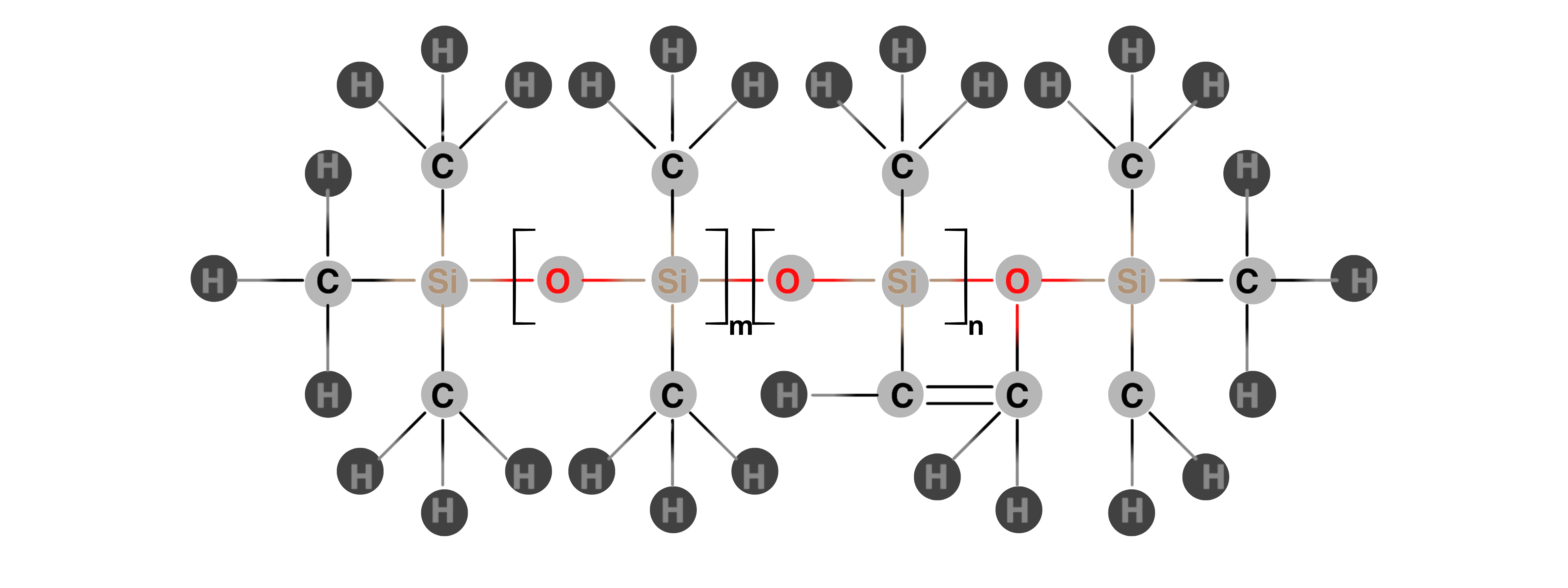
Viny Methyl Silicone (VMQ) Rubber
VMQ, a synthetic polymer made from silicon, oxygen, carbon, and hydrogen, offers superior flexibility, temperature resistance (–50° C to 230 °C), and sealing performance. Silicone rubber resists water, chemicals, and extreme temperatures, and its low compression set ensures long-term reliability. Additionally, it is compatible with a wide range of materials, preventing contamination and ensuring seamless integration in various applications.
Flat Gasket Chemistry | Density [g/cm3] | Elongation at Break [%] | Tensile Strength [MPa] | Hardness [Shore A] | Operating Temperature [°C] | Voltage Loss (mV) |
---|---|---|---|---|---|---|
EPDM | 1.45–1.50 | 200 | 2.5 | 80 | –57 to 150 | 29.8 |
FKM | 1.90–2.00 | 250 | – | 75 | –50 to 260 | 35 |
PTFE | 2.10–2.30 | 150 | 21–28 | – | –180 to 260 | 27.6 |
VMQ | 1.25–1.30 | 350 | 6 | 65–75 | –50 to 210 |
Frequently Asked Questions about Redox Flow Batteries
While metals can technically be used as electrodes in redox flow batteries (RFBs), the industry predominantly uses carbon-based electrodes due to several key advantages. Metal electrodes face practical limitations such as susceptibility to corrosion in acidic or alkaline environments, high costs for corrosion-resistant metals, and lower surface area compared to carbon materials.
Carbon electrodes, on the other hand, offer excellent corrosion resistance, high surface area for improved electrochemical activity, cost-effectiveness, and good electrical conductivity. These characteristics make carbon materials the preferred choice for RFBs, ensuring long-term stability, efficiency, and affordability for large-scale energy storage applications.
The thickness of electrodes in redox flow batteries varies depending on the design and application. Carbon felt electrodes typically range from 2 to 5 millimeters thick, offering high surface area and good conductivity. On the other hand, graphite plates or sheets can vary from 3 to 10 millimeters in thickness. The exact thickness is chosen to balance the need for sufficient surface area for redox reactions and minimal resistance to fluid flow, optimizing power density and system performance.
Presentations
Related Blogs

What are the Differences between Carbon Cloth, Paper, and Felt?
This blog explores the key differences between carbon paper, felt, and cloth as electrodes for redox flow batteries. It highlights how their unique properties impact battery efficiency and performance. Choosing the right material is crucial for optimizing energy storage and system longevity.