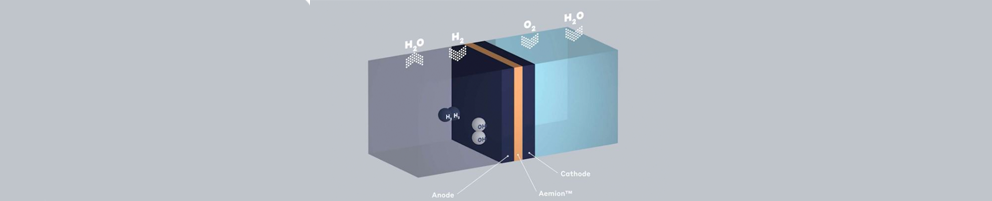
Fuel Cells
Hydrogen fuel cell stacks
- Home
- Renewable Energy
- Fuel Cells
- Ion Exchange Membranes
Ion Exchange Membranes
Ion exchange membranes are versatile and widely used in various applications across industries. These membranes are known for their ability to selectively remove ions from aqueous solutions, making them ideal for use in several applications, such as:
Water Purification: Ion exchange membranes are used in water purification processes to remove impurities such as salts, heavy metals, and organic compounds. This makes them ideal for use in the treatment of brackish and seawater, as well as in the purification of industrial and municipal wastewater.
Electrodialysis: Ion exchange membranes are used in electrodialysis, a process that separates ions based on their electrical charge. This application is commonly used in the food and chemical industries to concentrate or purify salts and other minerals.
Fuel Cells: Ion exchange membranes are used as separators in fuel cells to prevent the mixing of hydrogen and oxygen and to allow the transfer of ions between the electrodes.
Chlor-Alkali Production: Ion exchange membranes are used in the chlor-alkali industry to produce chlorine and caustic soda through the electrolysis of salt solutions.
Desalination: Ion exchange membranes are used in reverse osmosis desalination to remove salts and other impurities from seawater and brackish water, making it suitable for drinking and irrigation.
To summarize, ion exchange membranes have a wide range of applications, making them an essential component in several industries. Their ability to selectively remove ions makes them ideal for use in water purification, electrodialysis, fuel cells, chlor-alkali production, and desalination processes.
Structure of Ion exchange membranes
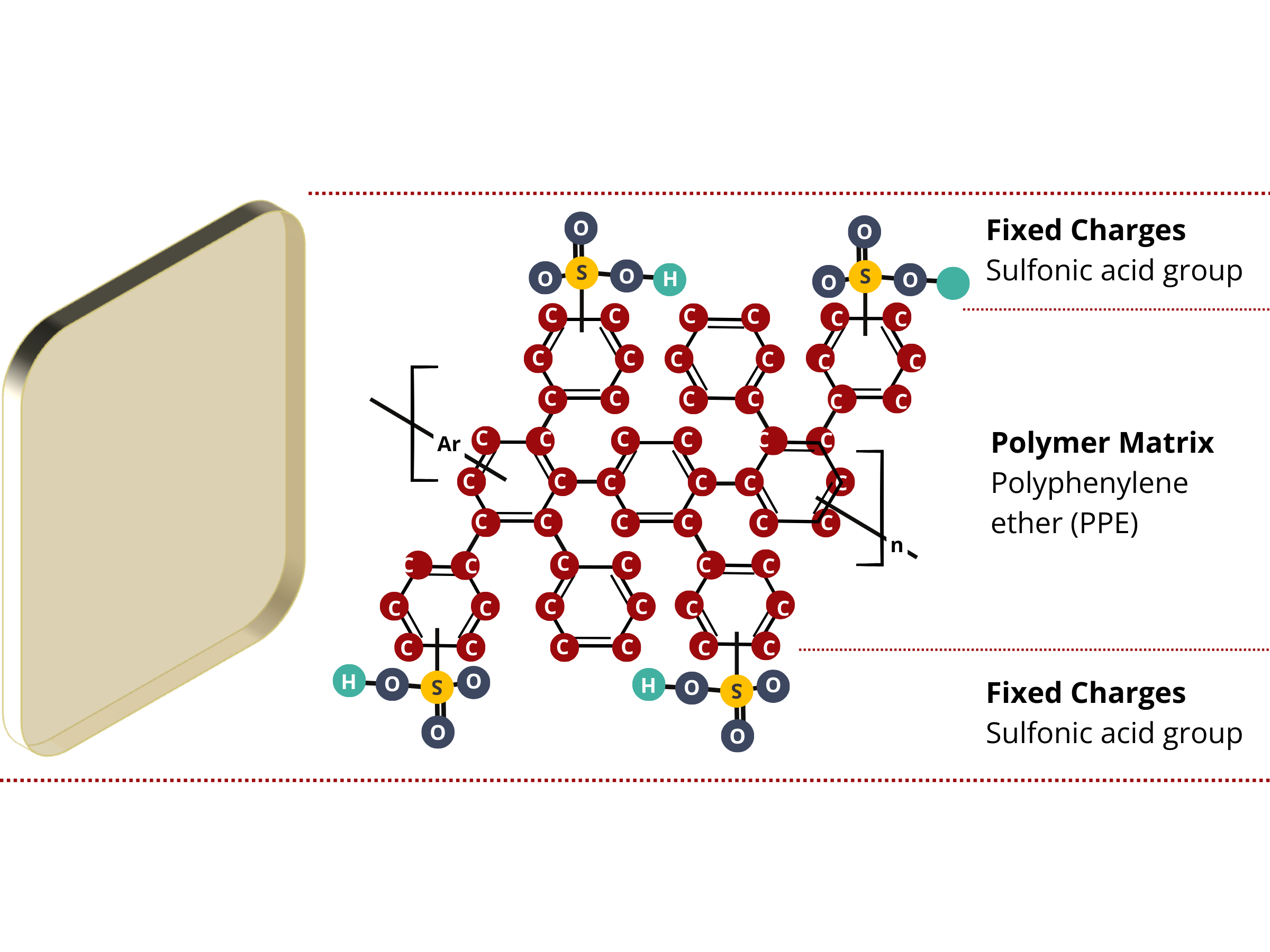
Ion exchange membranes are composed of two primary components.
- Immobile or stationary electric charges that are permanently attached to the polymer matrix of the membrane. These fixed charge groups completely or partially repel similarly charged ions (co-ions) from the membrane and allow the movement of differently charged ions (counter-ions) through the membrane.
- Main structural material or substance that forms the framework of the membrane and holds the ion exchange groups and other components within the membrane
Ion exchange membranes in Fuel cells
Efficient energy conversion systems need a chemical barrier, a membrane. The polymer membrane acts as an electrolyte, separating hydrogen and oxygen while only permitting the passage of certain ions. Ion-exchange materials can selectively filter positive or negative ions, including acid and base ions. Additionally they interrupt side reactions, increasing the block’s efficiency.
So in the case of a fuel cell, Hydrogen enters at the anode part where it get separated by its electrons. These electrons then travel through the vehicle’s circuit to the cathode in the form of electricity.
Key Material Property Considerations for Ion Exchange Membranes in Fuel Cell Applications
A high performance IEM should exhibit high ionic conductivity, high IEC, permselectivity close to unity, and excellent dimensional, chemical, mechanical, and thermal stabilities.
Key Properties
- Ion Exchange Capacity (IEC). IEC is the concentration of the fixed charged species measured as milliequivalent per gram (meq (fixed charge)/g (dry IEM)). The IEC of most commercially available IEMs varies from 1–3 meq/g. IEC is an important material property because it affects other IEM properties, such as ionic conductivity, swelling ratio, water uptake, and fluid permeability.
- Ionic conductivity. Ionic conductivity is a quantitative measure of the electric-field induced transport of ions across the IEM. It is the inverse of the membrane specific resistivity, which is an intrinsic IEM property that can be used for the comparison of the inherent efficiency of different IEMs. To put it simply, ionic conductivity tells how well the membrane can facilitate the transport of the counter-ions across. It is related to the IEC of the membrane.
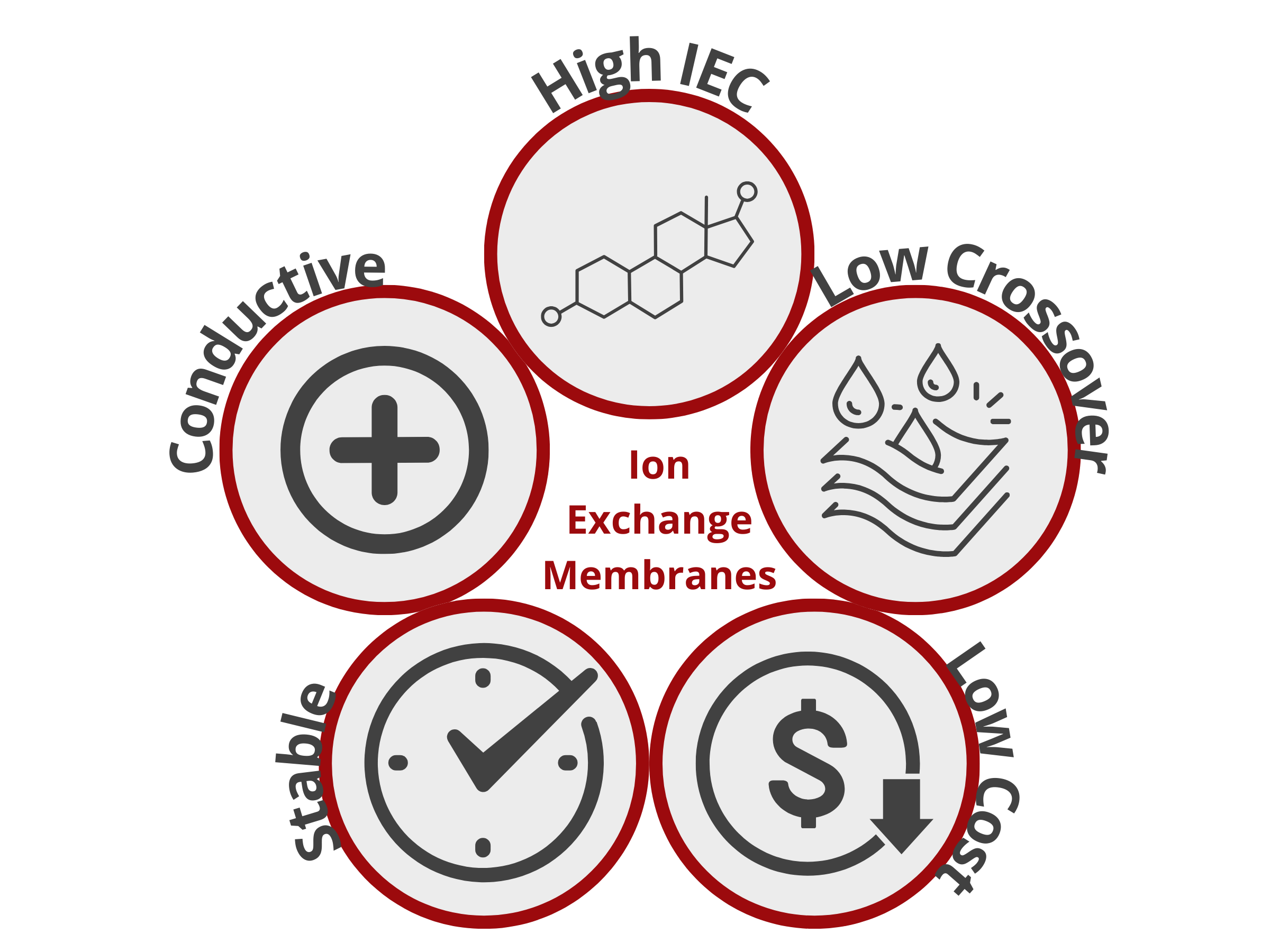
- Permselectivity. Permselectivity is one of the most important properties of IEMs. It refers to the ability of the membrane to selectively allow the transport of the counter-ions while blocking the passage of the co-ions. Permselectivity values range from 0 to 1. For example, a perfectly selective PEM (with a permselectivity of 1) will only allow the diffusion of protons (H+ ions) across the membrane, completely disabling the transport of negatively charged species.
- Dimensional stability (Membrane swelling and water uptake). Membrane swelling measures the degree at which the membrane expands or its volume increases as the IEM absorbs water. Water uptake, on the other hand, measures the amount of water that an IEM can absorb under specific conditions. Optimal levels of membrane swelling and water uptake is required for effective water management in the device.
- Chemical, mechanical, and thermal stability. Chemical stability is important to prevent membrane degradation as they are subjected to very aggressive conditions during operation. Mechanical stability ensures that the membrane will not fail in response to the compressive force applied to produce the stack. Lastly, thermal stability ensures that the IEM can continue to perform and not fail due to temperature effects.
Types of Ion Exchange Membranes according to Ion-Exchange Functionality
Cation Exchange Membranes (CEMs). These membranes selectively allow the passage of positively charged ions (cations) while blocking negatively charged ions (anions).
Anion Exchange Membranes (AEMs). AEMs selectively allow the passage of negatively charged ions (anions) while blocking positively charged ions (cations).
Proton Exchange Membranes (PEMs). PEMs is a special type of CEMs that transports protons (H+ ions).
Bipolar Ion Exchange Membranes (BIEMs). BIEMs have both cation and anion exchange functionalities within the same membrane, allowing for the separation of both cations and anions in different compartments.
Proton exchange membranes
There are two main types of exchange membranes depending on the type of ions that they allow through.
Proton exchange membranes are the most popular, industry standard electrolytes. As the name implies, the membrane exclusively allows positively charged atoms to pass through. Their efficiency has been tested and they have been implemented in manufacturing processes but they can be really expensive and less “Green” due to the precious metal catalysts required.
But not all PEM membranes are the same and there’s definitely room for improvement for this kind of fuel cell stack. Pemion, for example, can add to life and efficiency due to the order of magnitude reduction in H2/N2 crossover. It has lower pollution impact and can heavily reduce platinum dissolution while eliminating EOL bioaccumulative toxicity.
Proton exchange membrane (PEM) fuel cells are also referred to as polymer electrolyte membrane fuel cells. This type of fuel cell uses a polymer electrolyte and operates at lower temperatures of around 80 degrees Celsius. PEM fuel cells are more suitable for mobile and back-up power applications due to their high-power density and quick start-stop capabilities.
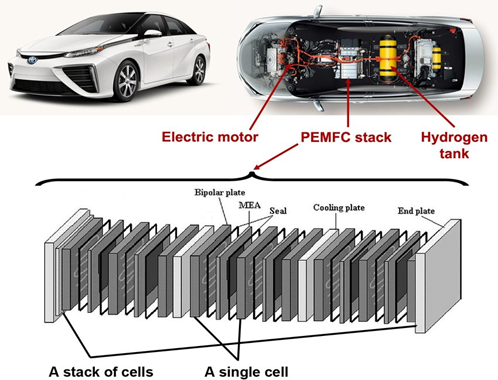
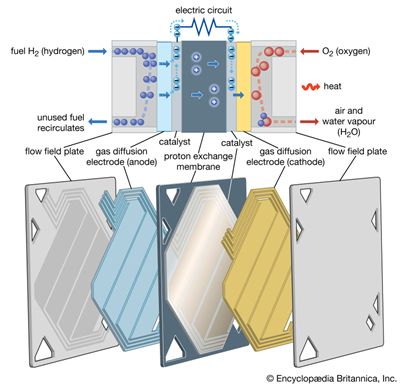
Proton exchange membranes are great for the time being but they are limited by the required catalysts and the platinized titanium components. That’s why we would expect a pendulum swing towards AEM. What’s AEM? You might ask...
Anion exchange membranes
Anion exchange membranes such as AEMION, allow through negatively charged atoms. They make the stack more cost efficient since they reduce the catalyst cost by enabling precious-metal free systems; thus reducing the cost of catalysts, the main cost driver for PEM based fuel cells.They also reduce transport layer costs by eliminating platinised titanium and enabling stainless steel components for simplified and automated machining. Those two simple facts should be enough to make AEM the electrolyte of choice, but the advantages do not stop there.
AEM combine the benefits of both Alkaline and PEM legacy systems. They have very low H2 crossover, high volumetric efficiency and allow rapid cycling for grid balancing.
Anion exchange membranes can also be a great solution to the struggling Hydrogen vehicles
Hydrogen vehicles are currently limited by:
- Lifetime limitations
- High impact & lifetime cost
AEM can put an end to this by:
- Increasing Lifetime, efficiency, range
- Replacing toxic & rare materials
- Unlocking ultra low-cost next-gen systems
- Unlocking alcohol-based fuel cells for low- to no-H2 infrastructure markets
That’s all great and all. But why aren’t they more popular? The main drawback is that they are not implemented in mass production yet so people are still learning about their usage and existence. An industry wide change should be expected in the following years but new technology adoption is always a lengthy procedure.
If you are interested in pioneering in this field with Anion exchange membranes as thin as 25um such as AEMION+™ - AF3-CLF9-25or even high conductivity catalyst ink polymers that enable precious metal free systems you can contact us for more information.
Presentations
Introduction to Ion Exchange Membranes for Electrochemical Applications
This presentation introduces ion exchange membranes– what they are, what they are made up of, where they are being used ...
Related Blogs

CAPLINQ Signs Definitive Agreement to represent Ionomr in Europe
The blog article highlights CAPLINQ's definitive agreement to represent Ionomr in Europe, expanding access to advanced ion-exchange materials. ...

Choosing the Right Ion Exchange Membrane for Your Water Electrolyzer and Fuel Cell Applications?
The blog article provides guidance on selecting the ideal ion exchange membrane for optimizing performance in water electrolyzers and fuel cell applications....

How Will the Impending PFAS-ban Affect Proton Exchange Membranes for Water Electrolyzers and Fuel Cells?
The blog article explores the potential impact of the upcoming PFAS ban on proton exchange membranes used in water electrolyzers and fuel cells, including challenges and possible alternatives....