Light Emitting Diodes
Light emitting diodes are light emitting dies that get their color or hue through the phosphor that is coated on top of the die. They are typically blue tinted and are getting their color from a combination of the phosphor, the die light intensity and the overmolded optoelectronic molding compound. There are multiple LED types for a huge variety of applications, ranging from simple through hole monochrome LEDs to backlight, organic, miniLEDs and industrial baylights. All of these LED types have the same principle but completely different application and reliability requirements.
Light emitting diodes generate light upon the absorption of electrical energy. include a multitude of technologies and devices that utilize the interaction between light and materials. To maximize light generation and emission, LEDs are designed to minimize reflection at material interfaces and are encapsulated with materials that allow light transmission while protecting the LED.
Target Applications for Next-Generation LED Materials
UV LEDs for applications below 300 nm, where transmission is challenging
Mid- to high-power LEDs with junction temperatures exceeding 150 °C, requiring UV-resistant materials due to epoxy and silicone degradation.
Outdoor RGB SMD LED applications that require UV resist
UV and visible light reflectors with excellent temperature resistance and color stability, particularly in white
How can a diode produce light?
Diodes produce light through a process called electroluminescence. When an electron in a diode moves from a higher energy state to a lower one, it releases energy in the form of a photon. This energy can be visible as light if the diode is made of a material that allows for the emission of photons within the visible spectrum.
As discussed in diode application, free electrons can fall into empty holes from the P-type layer. This transition from a higher energy level to a lower one results in the emission of a photon. However, the specific frequency and energy of the emitted photon depend on the material used in the diode.
Standard silicon diodes, for instance, emit photons in the infrared range. This means the light they produce is invisible to the human eye. However, other materials, like gallium arsenide phosphide, can be used to create diodes that emit photons in the visible spectrum, producing visible light. These diodes are commonly used in LEDs (Light-Emitting Diodes) for various applications, including lighting, displays, and communications.
The main semiconductor materials used to manufacture LEDs are:
- Indium gallium nitride (InGaN): blue, green and ultraviolet high-brightness LEDs
- Aluminum gallium indium phosphide (AlGaInP): yellow, orange and red high-brightness LEDs
- Aluminum gallium arsenide (AlGaAs): red and infrared LEDs
- Gallium phosphide (GaP): yellow and green LEDs
How white light is produced?
There are several methods of generating white light using LEDs. Below is 2 typical emission methods.
Blue LED+Yellow Phosphor
Combining a blue LED with yellow phosphor is a widely used method to produce white light. The blue LED emits light in the blue spectrum that passes through a layer of yellow phosphor, which is a material that absorbs some of the blue light and re-emits it as yellow light. The combination of the remaining blue light and the newly emitted yellow light creates white light. This is because blue and yellow are complementary colors, and when mixed, they produce a broad spectrum of light that appears white to the human eye.This method is easier than other solutions and provides high efficiency, making it the most popular choice on the market.
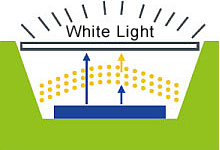
Red LED+Green LED+Blue LED
Combining red, green, and blue LEDs can produce white light through a process called additive color mixing. When the light from these three primary colors is combined in the right proportions, it creates the perception of white light. This method is commonly used in full-color LED devices, such as screens and displays, to produce a wide range of colors by varying the intensity of each LED
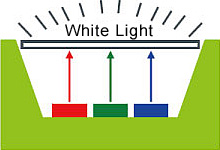
General Considerations For LED Encapsulants
As LED encaplants, besides general consideration of packaging materials, optical performance with long-term reliability is specially emphasized.
Challenges & Solutions
Challenges | Problem Description | Encapsulation Solutions |
---|---|---|
Light Extraction |
|
|
Delamination |
|
|
Thermal-Yellowing |
|
|
UV-Yellowing |
|
|
Aging/Lifetime |
| Above All |
Sensor Transmission |
|
|
LED Clear Molding Compounds Product Overview
Monochrome LEDs | HD RGB LEDs | White LEDs | |||||
Product | TC-8020 (Star Product) | TC-8040 | TC-7600 (Popular Product) | TC-7800 (In Development) | TC-8030 | TC-8060 (Popular Product) | TC-8090 (In Development) |
Summary |
|
|
| ||||
Applications | 7-segment LED display, compact LED indicator, monochrome Chip LED, photo-link | High density (fine-pitch) RGB LED display | Decorative White LED | Backlight | High Reliability Backlight | ||
Light Decline Aging Test | - | Medium 10-50% RT*20mA*500hrs | Medium 10-50% RT*5mA*1000hrs | Low <50% RT*20mA*500hrs | High <10% RT*5mA*1000hrs | ||
Reliability Tests | Reflow, TCT, 85℃@85%RH | Reflow, TCT, 85℃@85%RH, PCT | Reflow, TCT, 85℃@85%RH | ||||
Highlight | Low stress and filter versions available | High reliability Mid blue-ray decay | Low blue-ray decay | Low blue-ray decay High anti-yellowish | Low cost | Low blue-ray decay | Low blue-ray decay Anti-moisture |
Comparable | XX-18, XX-1012, XX-8524 | XX-600H | XX-600H | XX-600H-94000 | XX-1014, XX-8524 | XX-1000, XX-814, XX-97 | XX-1000, XX-814, XX-97 |
Child Product | TC-8020L/LS low-stress TC-8020T-SR self-release version TC-8050 for large package |
|
|
| TC-8034 with low decay TC-8036 with low decay | Low CTE product TC-9000T with transparent filler TC-8060 IMP low modulus version |
|
Die Attach For LEDs
LOCTITE ABLESTIK ABP 8037TI silver-filled die attach adhesive paste is specifically designed to attach small diodes in high volume manufacturing. Even more specifically, it is the highest volume silver-filled die attach paste for high reliability LED attach and manufacture when using small die on Au-finished leadframes. Used in high-volume manufacturing throughout China and Malaysia.
Also extremely popular:
LOCTITE ABLESTIK 84-1LMISR4 is a manufacturer's product of choice, can be used for LED applications and like most epoxies it is suitable for Copper substrates.
One alternative:
LOCTITE® ABLESTIK ABP 8035M is a non-conductive clear silicone designed for high brightness LED die attach applications.
Non conductive option:
LOCTITE ABLESTIK QMI536NB creates packages and devices that have high resistance to delamination and popcorning after multiple exposures to lead-free solder reflow temperatures. It has good optical performance with high transmittance, Optical Density and HRI and is a great solution for ASIC attach and LED attach.
High Purity Alumina (HPA) For LEDs
HPA as LED Encapsulant
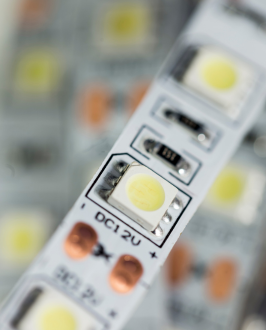
LED encapsulation protects and packages LED chips to enhance their performance and longevity. Common types include epoxy encapsulants, which are cost-effective and transparent but have limited thermal conductivity and may yellow over time; silicone encapsulants, known for their excellent thermal stability and UV resistance but at a higher cost and slightly reduced transparency; and ceramic, offering superior thermal conductivity and mechanical strength, ideal for high-performance LEDs.
HPA as Coatings for Phosphors in LEDs
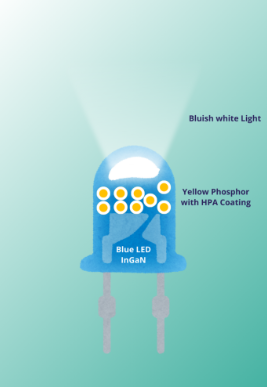
The purity of alumina used in LED production should be 99.99% (equivalent to Grade 4N) or higher. This exceptionally high purity is important, as even trace impurities can greatly affect the performance and lifespan of LEDs.
Grade (Purity) | Na | Mg | Si | Ca | Ti | Cu | Cr | Fe | K |
3N (99.9%) | <150 | <20 | <50 | <50 | <20 | <10 | <5 | <50 | <20 |
4N(99.99%) | <30 | <5 | <10 | <10 | <5 | <5 | <5 | <20 | <10 |
5N(99.999%) | <4 | <1 | <3 | <3 | <0.5 | <0.5 | <1 | <1 | <0.5 |
HPA-SDF is an advanced 5N high-purity alumina engineered for sapphire production, featuring spherical morphology, high crystallinity, and a controlled specific surface area. These key properties enhance its performance in precision optical applications, making it an ideal material for mini-LED and micro-LED displays, where superior clarity, durability, and efficiency are essential.
HPA M Series (M1, M3, & M5) - The HPA M Series is a high-purity (5N) alumina with an irregular morphology, designed for high temperature applications. The series is differentiated by its D50 particle size value, offering customized solutions for various requirements. Its unique irregular morphology makes it particularly well-suited for phosphor coatings in LED applications, enhancing light conversion efficiency and overall performance.
Frequently Asked Questions about Light Emitting Diodes
OLED (Organic Light Emitting Diode) displays use organic materials to emit light when an electric current is applied, allowing each pixel to emit its own light for deep blacks and high contrast. However, they use a passive matrix to control pixels, which is slower and less precise, making them suitable for smaller screens.
In contrast, AMOLED (Active Matrix Organic Light Emitting Diode) displays incorporate an active matrix layer with thin-film transistors (TFTs) and capacitors for faster pixel response times, higher refresh rates, and more precise control. This makes AMOLED displays ideal for larger screens and higher resolutions, offering better performance and efficiency, which is why they are commonly used in high-end smartphones and tablets.
How does the encapsulation material affects the performance of LEDs?
The materials used in LED encapsulants significantly impact their performance by providing protection and enhancing efficiency. Encapsulants shield the delicate LED chip from environmental factors such as moisture, dust, and UV radiation, which can degrade performance over time. Materials like epoxy resins offer excellent adhesion, thermal resistance, and light transmission, ensuring consistent light output and durability. Silicone encapsulants provide superior thermal stability and UV resistance, making them ideal for harsh conditions. Polyurethane and acrylic encapsulants offer mechanical strength and optical clarity, respectively. By selecting the appropriate encapsulant material, manufacturers can enhance the longevity, efficiency, and overall performance of LEDs.
How does HPA compare to other substrate materials in LEDs?
Compared to other materials like silicon or silicon carbide, HPA-based sapphire substrates offer better thermal stability, higher hardness, and improved light transmission, making them the preferred choice for high-performance LEDs.
What are the benefits of using HPA in LEDs?
Enhanced brightness – Provides high optical clarity for better light output.
Improved thermal management – Efficiently dissipates heat, preventing overheating.
Longer LED lifespan – Reduces material degradation over time.
Greater reliability – Maintains performance in high-temperature and high-humidity environments.
Color filtering involves selectively allowing certain wavelengths of light to pass through while blocking others. This process does not change the wavelength of the light; it simply filters out unwanted colors. For example, a red filter will let red light pass through while absorbing or reflecting other colors.
Color conversion, on the other hand, involves changing the wavelength of light. This process absorbs light at one wavelength and re-emits it at a different wavelength. For instance, a material might absorb blue light and re-emit it as green light. This is commonly used in applications like phosphor coatings in LEDs, where blue light is converted to white light by re-emitting it at different wavelength.
What is the difference between SMT and Through-hole LEDs?
The primary difference between SMT (Surface-Mount Technology) and through-hole LEDs lies in their mounting methods and applications. SMT LEDs are mounted directly onto the surface of a printed circuit board (PCB) without the need for drilling holes. This allows for a more compact design, higher component density, and automated assembly, making them ideal for modern, space-constrained electronic devices. In contrast, through-hole LEDs have leads that pass through holes drilled in the PCB and are soldered on the opposite side. This method provides greater mechanical stability and is often used in applications requiring durability and resistance to physical stress, such as industrial equipment and outdoor displays.
How is HPA used in LED production?
HPA is primarily used in manufacturing synthetic sapphire substrates, which serve as the base material for LED chips. It ensures high light transmittance, improves efficiency, and provides thermal stability for LEDs.
Can HPA be used in Mini-LEDs and Micro-LEDs?
HPA is essential for Mini-LED and Micro-LED technologies due to its role in improving brightness, energy efficiency, and pixel density. It ensures precise light control, making it ideal for next-generation display applications.