Insulated-Gate Bipolar Transistor (IGBT)
IGBTs (Insulated Gate Bipolar Transistors) are power semiconductor devices that combine the high switching speed of MOSFETs (Metal-Oxide-Semiconductor Field-Effect Transistors) and the low saturation voltage of bipolar junction transistors (BJTs). This makes them ideal for high-power applications, such as motor control, renewable energy systems, and power inverters.
IGBTs consist of three main components: an N-type semiconductor, a P-type semiconductor, and an insulated gate. When a voltage is applied to the gate, it creates an electric field that controls the flow of current between the N-type and P-type semiconductors. This allows for precise control of the power flow in high-power applications, and the insulation of the gate reduces the risk of electrical breakdown.
One of the biggest advantages of IGBTs is their fast switching speed, which allows them to respond quickly to changes in voltage and current. This is especially important in applications that require rapid power changes, such as motor control. The low saturation voltage of IGBTs also makes them ideal for high-power applications, as it reduces the risk of thermal damage and extends the lifespan of the device.
IGBTs can handle high voltage and current levels, making them suitable for high-power applications. They are also capable of operating at high frequencies, making them useful for applications such as high-frequency power conversion. In addition, IGBTs are highly reliable and durable, making them ideal for use in harsh industrial environments.
What are the benefits of IGBTs?
IGBTs are traditionally used with Silicon based dies for Power modules. They are made from an emitter, collector and gate terminals, while MOSFETs consist of source, drain and gate terminals. Just like MOSFETs, depending on whether they are thru hole or surface mount they can be housed in a multitude of packages. TO220, TO262 and TO 247 are very common for thru-hole components while TO263 (D2PAK) and TO252(DPAK) are go-to packages for surface mount.
These devices are preferred for medium to high power applications. Compared to MOSFETs they can handle high voltages due to their lower conduction loss but due to their nature they are not meant for high-frequency applications. They can be typically found in welding equipment, automotive power modules, UPS, chargers and are the leading technology in mainstream high voltage packages.
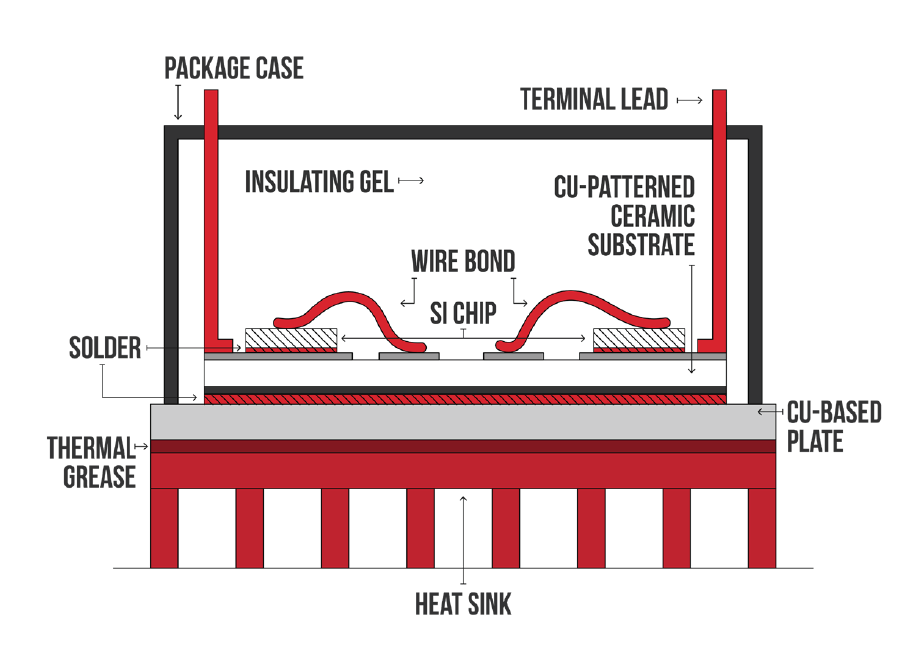
Why Die Attach is critical in IGBTs?
The die attach process is a crucial step in IGBT manufacturing, as it directly impacts the thermal, electrical, and mechanical performance of the device. Here are the key performance requirements for die attach materials in IGBT applications:
- Thermal Conductivity: IGBTs generate significant heat during operation. The die attach material must efficiently transfer heat from the die to the substrate to prevent overheating and ensure long-term reliability.
- Electrical Conductivity: A good die attach material ensures low electrical resistance, which is essential for minimizing power losses and improving efficiency.
- Mechanical Stability: The material must withstand thermal cycling, mechanical stress, and vibrations without cracking or delaminating.
- Thermal Expansion Matching: The coefficient of thermal expansion (CTE) of the die attach material should closely match that of the die and substrate to reduce stress during temperature fluctuations.
- Void-Free Bonding: Voids in the die attach layer can lead to hotspots and reduced performance. A uniform, void-free bond is essential for optimal thermal and electrical performance.
The Die Attach process in IGBT manufacturing
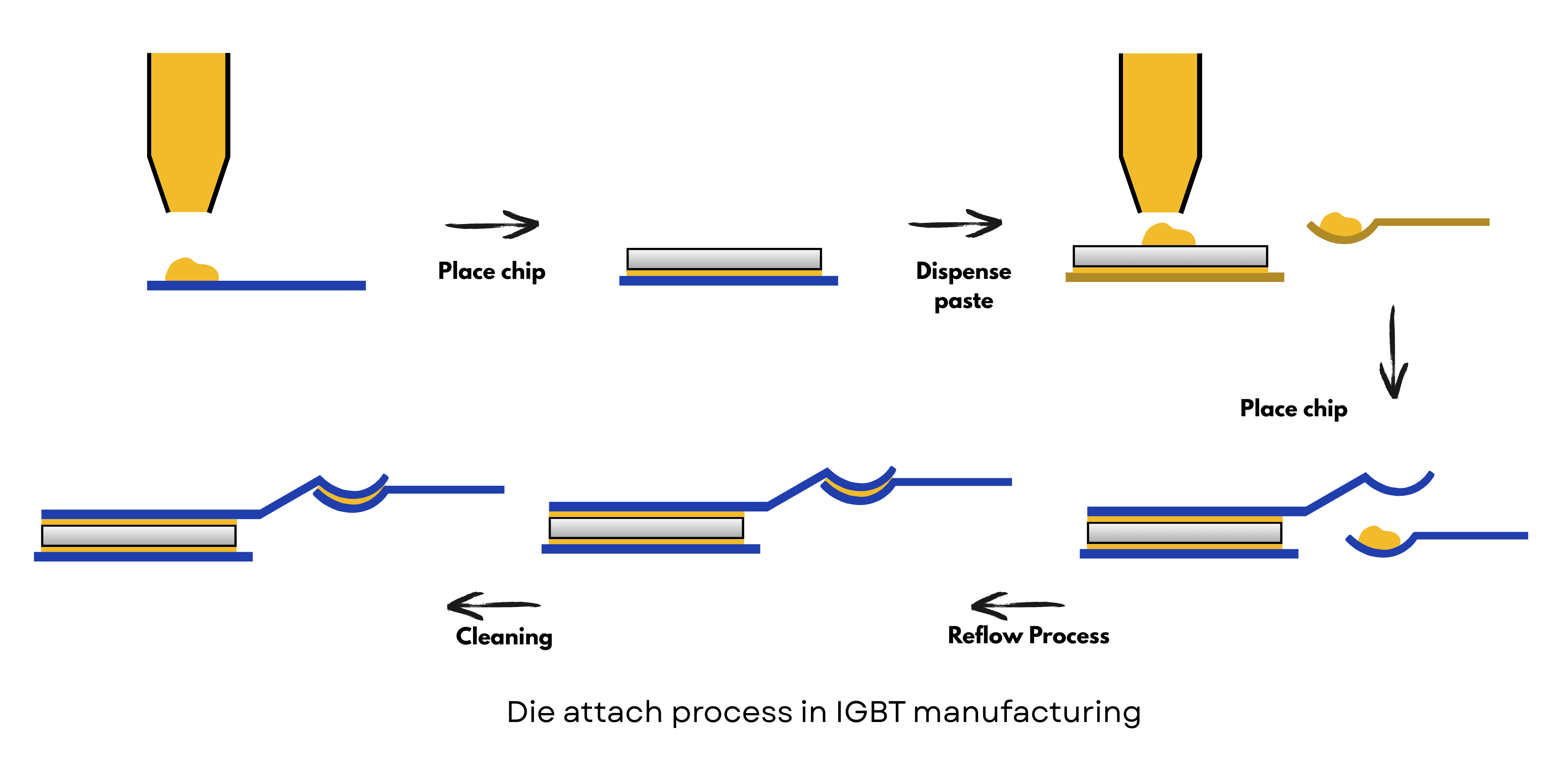
Surface Preparation
The substrate and die surfaces are cleaned to remove contaminants that could affect adhesion. Surface treatments, such as plasma cleaning, may be applied to enhance bonding.
Material Application
The die attach material (e.g., solder paste, epoxy, or sintered silver) is applied to the substrate using techniques like dispensing or stencil printing.
Die Placement
The IGBT die is precisely placed onto the substrate using automated pick-and-place equipment.
Curing or Reflow
For epoxy-based materials, the assembly is cured at a specific temperature to harden the adhesive. For solder-based materials, a reflow process is used to melt the solder and form a strong bond.
Inspection
The bonded assembly is inspected for voids, cracks, or misalignment using X-ray or ultrasonic imaging.
Bond Line Thickness (BLT) in Die Attach
Bond Line Thickness (BLT) is a critical parameter in the die attach process. It refers to the thickness of the die attach material between the die and the substrate. The BLT has a direct impact on thermal and mechanical performance:
- Thermal Performance: A thinner bond line improves heat transfer from the die to the substrate, reducing thermal resistance. However, it must be uniform to avoid hotspots.
- Mechanical Stability: A thicker bond line can absorb stress from thermal expansion mismatches but may increase thermal resistance.
- Optimal Range: For most IGBT applications, the BLT typically ranges from 10 to 50 microns, depending on the material and application requirements.
Controlling BLT requires precise dispensing or printing techniques and careful process optimization to ensure uniformity and reliability.
Qualification test forDie Attach in IGBTs
To ensure the quality and reliability of the die attach process, several qualification tests are performed:
Void Testing:
- Voids in the die attach layer can create hotspots and reduce thermal performance. X-ray imaging or scanning acoustic microscopy (SAM) is used to detect and measure voids.
- Acceptable void percentages are typically less than 5-10%, depending on the application.
Shear Testing:
- This test measures the mechanical strength of the die attach bond. A shear force is applied to the die until the bond fails, and the force required is recorded.
- High shear strength indicates a robust bond capable of withstanding mechanical stress.
Thermal Cycling:
- The assembly is subjected to repeated temperature cycles to simulate real-world operating conditions. This test evaluates the material’s ability to withstand thermal stress without cracking or delaminating.
Thermal Resistance Measurement:
- The thermal resistance of the die attach layer is measured to ensure efficient heat transfer. Lower thermal resistance is critical for high-power IGBT applications.
Cross-Sectional Analysis:
- A cross-section of the die attach layer is examined under a microscope to assess bond line thickness, uniformity, and material integrity.
Conclusion
The die attach process is a critical factor in the performance and reliability of IGBTs. By selecting the right die attach material and ensuring a robust bonding process, manufacturers can achieve optimal thermal management, electrical efficiency, and mechanical stability. Whether you’re working on high-power industrial drives or electric vehicle inverters, understanding the die attach process is essential for success. For high-performance die attach materials, consider exploring Caplinq’s offerings. Our solutions are tailored to meet the needs of advanced IGBT applications, ensuring your devices operate at peak performance.
This page is a work in progress). Come back soon for more information.
In the meantime, you might be interested in thermal solutions for inverters or TO packages for power modules.