AEMION+™-AF3-HWC9-70
- Water Electrolysis
- Acid Recovery and Salt Splitting
- 70 micron thick membrane with woven PEEK reinforcement
Product Description
AEMION+™-AF3-HWC9-70 is a breakthrough advanced polyimidazolium-based ion exchange membrane that enables the rapid growth of the hydrogen economy. Ionomr's Aemion+® anion exchange membranes are significantly more durable than our competitors', leading to thinner membranes, longer service life and reduced overall system costs.
AEMION+™ membranes have low ionic resistance and high electrical resistance. They are the first available commercial materials with excellent chemical stability in solutions of both high and low pH, and even in the harshest alkaline electrolysis systems (2–3M KOH, 80-100 °C). These advanced anion exchange membranes are frontiers in materials science with their unique hydrocarbon structure and good mechanical strength. All of these desirable properties unlock other potential applications that were previously constrained by the membrane’s poor durability and integrity. AEMION+™ is the enabling, platform material for the scale-up of AEMWE technology to industrial level.
AEMION+™-AF3-HWC9-70 is the thinner version of AEMION+™ - AF3-HWK9-75. The thickness of ion exchange membranes plays a crucial role in the performance and efficiency of water electrolyzers and fuel cells. Generally, thinner membranes are often preferred to maximize conductivity and efficiency. Therefore, thin membranes are more suitable in applications where high power density and rapid response are more critical. On the other hand, thicker membranes are preferred or applications requiring long-term stability and robustness. Optimizing the membrane thickness to your specific electrochemical process and operating conditions is the key to unlocking optimal performance.
With its excellent chemical stability at the full pH spectrum (0–14), AEMION+™-AF3-HWC9-70 can also be used in acid receovery and salt splitting applications. Aemion+® anion exchange membranes exhibit high oxidative tolerance, selectivity, and extended maintenance cycles, contributing to extended system lifetimes. AEMION+™-AF3-HWC9-70 demonstrates slightly lower proton blocking at high acid concentrations compared to other purpose-built AEMs. Still, it demonstrates significantly lower resistance and total power consumption per mole of acid, making them effective in concentrating applications (i.e., removal of total sulfate to 0 from a stream), and in use for acid concentration up to 5–7 wt%.
Technical Specifications
Hydrolytic Properties | |||||
Linear Expansion | 3 (22 °C) % | ||||
Water Uptake | 15 (22 °C) % | ||||
Z-Expansion | 5 (22 °C) % | ||||
Electrochemical Properties | |||||
Thru Plane Cl- Conductivity | >5 | ||||
General Properties | |||||
Total Thickness Total Thickness Total thickness is taking into account all the films, coatings, adhesives, release liners and special layers and is the maximum thickness of a film or tape. | 70–75 μm | ||||
Physical Properties | |||||
Young's modulus | 600–850 MPa | ||||
Mechanical Properties | |||||
Elongation Elongation Elongation is the process of lengthening something. It is a percentage that measures the initial, unstressed, length compared to the length of the material right before it breaks. It is commonly referred to as Ultimate Elongation or Tensile Elongation at break. | >15 % | ||||
| |||||
Thermal Properties | |||||
Glass Transition Temperature (Tg) Glass Transition Temperature (Tg) The glass transition temperature for organic adhesives is a temperature region where the polymers change from glassy and brittle to soft and rubbery. Increasing the temperature further continues the softening process as the viscosity drops too. Temperatures between the glass transition temperature and below the decomposition point of the adhesive are the best region for bonding. The glass-transition temperature Tg of a material characterizes the range of temperatures over which this glass transition occurs. | >300 °C |
Additional Information
Non Disclosure Agreement
This is a proprietary product from Ionomr, therefore, we require a signed NDA between the end customer and Ionomr before we are able to ship out the material, either for commercial use, or research.
This is done to prevent reverse engineering and public disclosure. The NDA does not restrict patenting anything, but does include the physical materials and their composition as confidential which prevents specific disclosure in a patent or otherwise but not calling out use of an AEM including Aemion by trade name. The test results are included as confidential information, and require approval from both parties to disclose. We are not concerned about blocking any publications, but would typically advise if we believe better results can be achieved.
We have a more explicit MTA (Materials Transfer Agreement) we use with academic/research organizations which outlines more detail around materials IP and publication.
Please find the NDA here and fill it in when contacting us for quotations.
What are anion exchange membranes?
Anion Exchange Membranes (AEMs) are a specialized type of ion exchange membrane that are specifically designed to exchange anions (negatively charged ions) in electrochemical processes. They are used in various applications such as water treatment, fuel cells, and batteries, where it is important to regulate the flow of anions. Some of the key features and benefits of AEMs include:
High selectivity: AEMs are designed to selectively exchange anions, ensuring the stability and efficiency of electrochemical reactions.
Improved performance: The use of AEMs can result in improved performance in electrochemical processes, particularly in fuel cells and batteries.
Customizable properties: The properties and characteristics of AEMs can be customized to meet the specific needs of different applications.
Durable and long-lasting: AEMs are designed to be strong and long-lasting, making them ideal for demanding applications.
AEMs are made of a polymer material that contains functional groups with a negative charge, such as sulfonic acid or carboxylic acid. These functional groups are capable of exchanging anions in electrochemical processes. The structure of the membrane and the type of functional group can affect the properties and characteristics of the AEM, including its ion exchange capacity, selectivity, and stability.
In electrochemical processes, AEMs are typically used to separate anions and cations in a flow field, allowing for the regulation of ionic flow. This regulation can result in improved performance and efficiency, particularly in applications such as fuel cells and batteries, where the exchange of anions is critical.
AEMs can also be customized to meet the specific needs of different applications. For example, the type and concentration of functional groups can be adjusted to improve the selectivity of the membrane, and the thickness and structure of the membrane can be optimized to improve its stability and durability.
AEMION+® Anion Exchange Membranes Enable Large-scale Commercial Development
Alkaline water electrolysis (AWE) is the most mature technology that has been used extensively over the past decades. In this configuration, a liquid caustic electrolyte solution, most commonly NaOH and KOH, is pumped into the system composed of electrodes separated by a porous diaphragm. While AWE is a low-cost technology owing to its propensity for cheap catalysts, it suffers from large internal resistance between the diaphragm and liquid electrolyte. It typically operates under low current densities, which consequently requires bulky stack configurations at larger scales.
To make the electrolyzer design more compact, proton exchange membranes are used instead of the liquid electrolyte in AWE. Instead of OH– ions in AWE, H+ ions are the mobile carriers in proton exchange membrane water electrolysis (PEMWE). H+ ions exhibit significantly better ionic conductivity than OH–, which makes the achieved efficiency of PEMWE higher than that of AWE. On top of that, the more compact design of PEMWE makes it able to operate even under high current densities. The caveat? Since PEMWE operates under highly acidic conditions, the catalysts that can be used are often limited to platinum group metals, increasing the CAPEX and OPEX of PEMWEs.
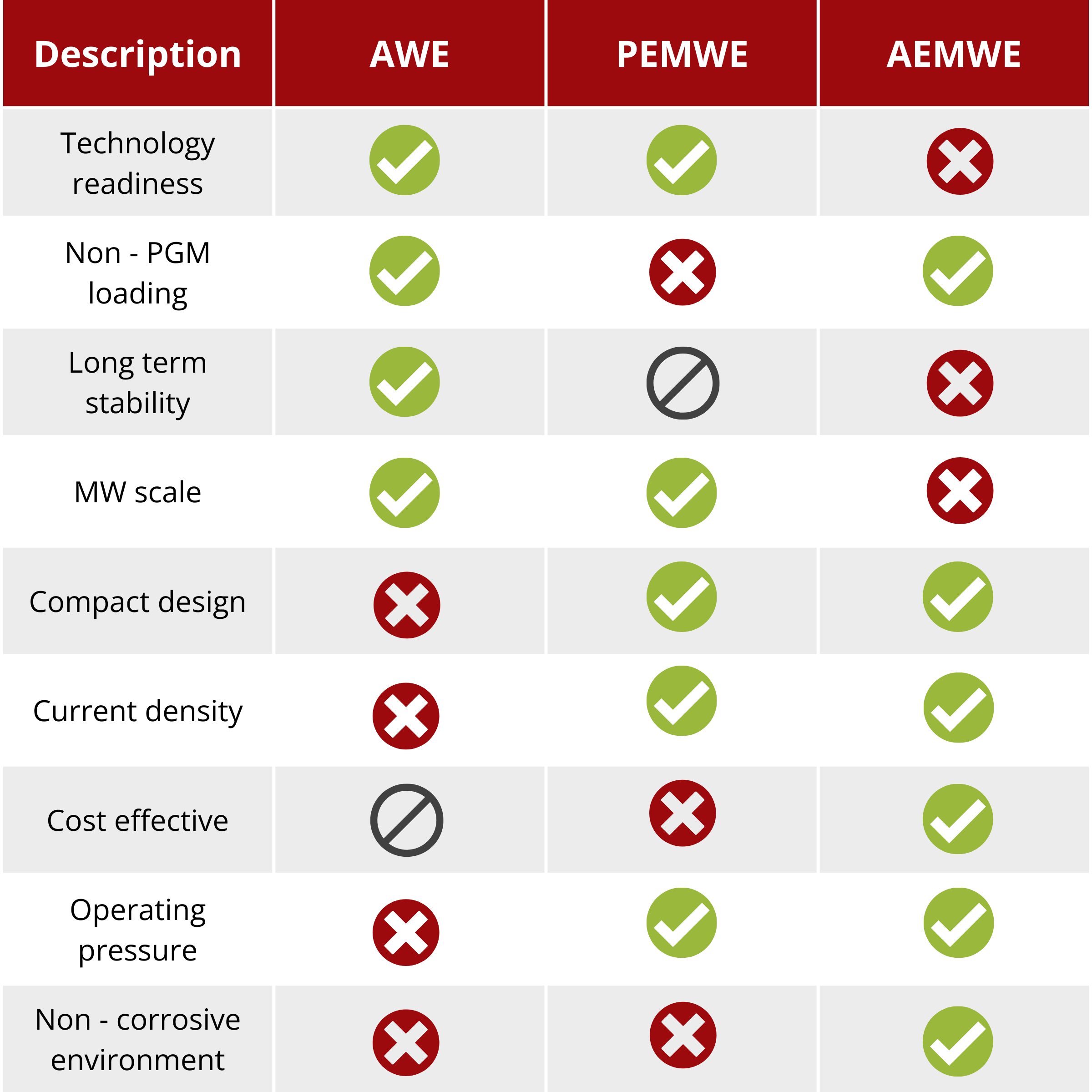
At their current scale, the CAPEX of AWE and PEMWE are way above the targets set by the US Department of Energy. Low CAPEX water electrolysis systems like AAEMWE makes it possible for green hydrogen production technologies to become more competitive against the traditional steam reforming process. Following this thought, developing high-performance and stable alkaline anion exchange membranes facilitates the growth of a sustainable hydrogen economy.
In the white paper, “Hydrogen Production Cost by AEMION+®,” the investment costs of AEMWE systems at scales comparable to those of the most recent industrial-scale AWE and PEMWE deployments. The investment costs of five water electrolyzer configurations were compared.
Without a doubt, the pathway towards low cost and sustainable water electrolysis is possible with further developments in AEMWE technologies. Using Ionomr Innovations' Aemion+TM membrane, AEM stability has increased to the point where large-scale commercial development is possible, and performance may be improved based on a stable platform to approach PEMWE. Ionomr is partnering with industry players and research institutes throughout the world to scale up this technology and thoroughly evaluate its durability and performance in order to demonstrate AEMWE's value proposition for the provision of energy-efficient and low-cost green hydrogen.
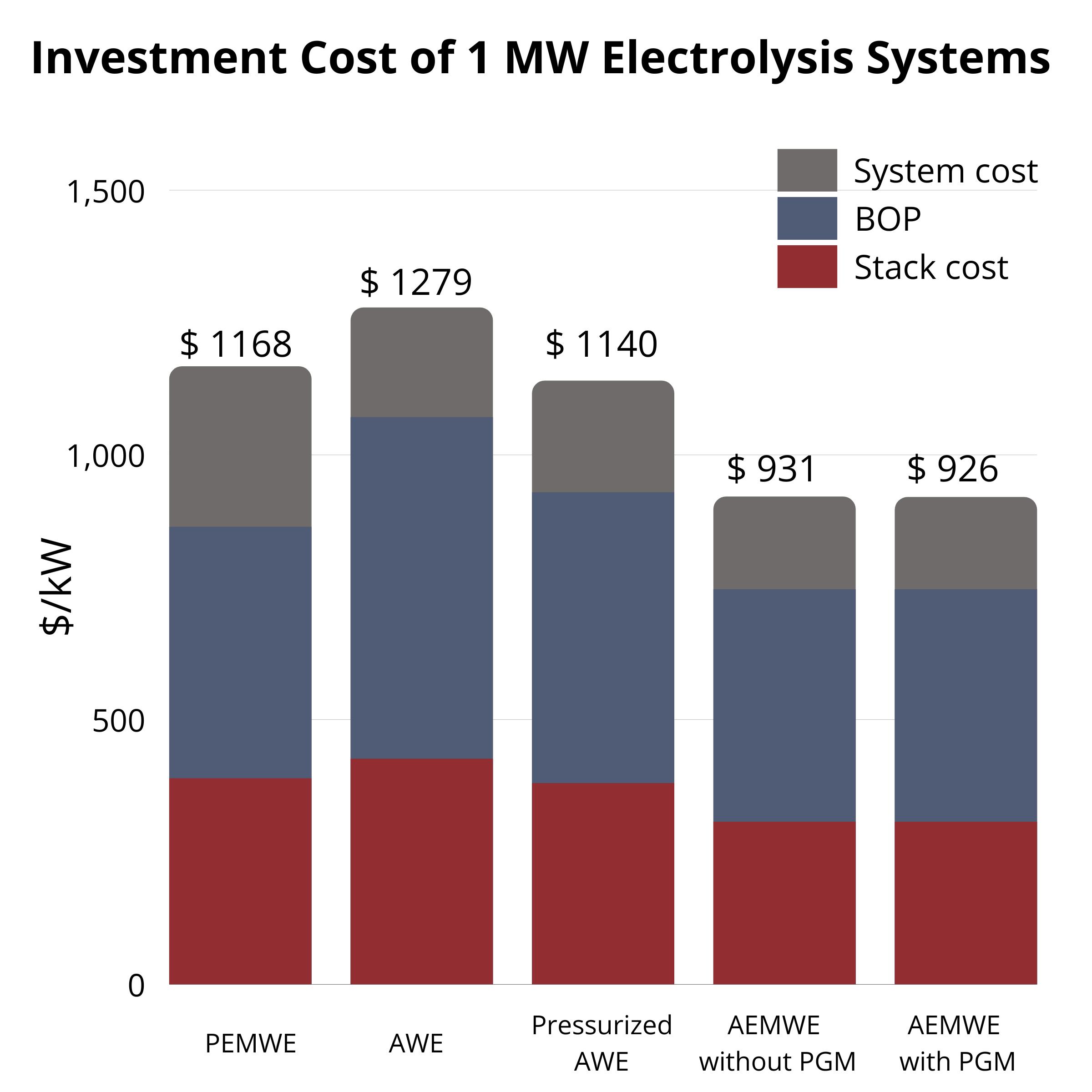
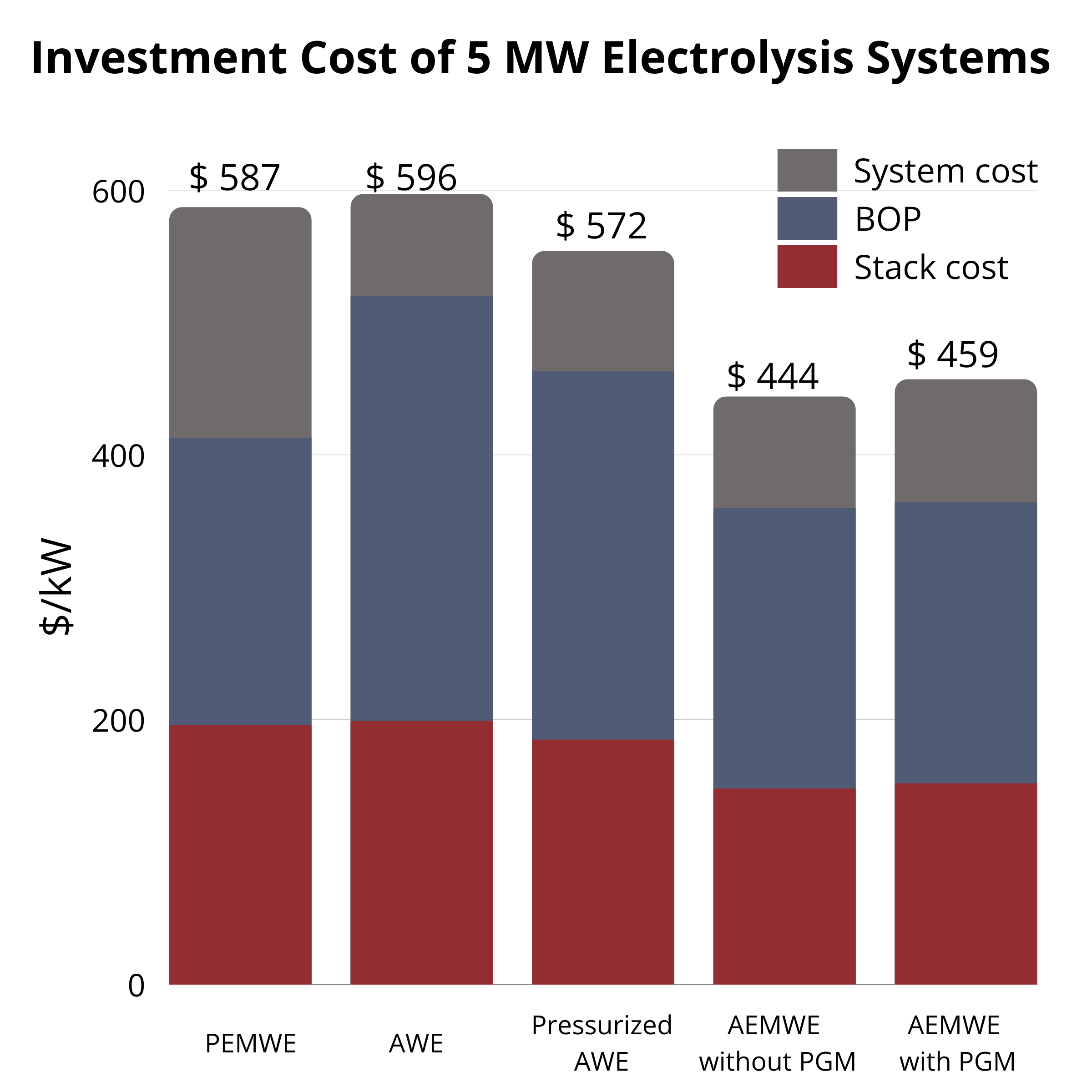
Durable Anion Exchange Membranes
Aemion™ anion exchange membranes are the most durable and high-performance anion exchange products on the market. They are stable in both highly basic and strongly acidic environments, providing a marked improvement in product life cycle, even in the harshest operating conditions. This unique stability unlocks a broad range of applications, from fuel cells, chemical generation, recovery and long-life energy storage to electrolysis and hydrogen production.
These membranes are based on the breakthrough discovery that weak sites in polymer structures are the root cause of AEM instability, and they can be effectively protected to prevent alkaline and oxidizing species from breaking down the polymers. The resulting hydrocarbon backbone provides a platform that enables simultaneous performance and life cycle improvements across the industry in energy and water, while reducing your product’s environmental impact.
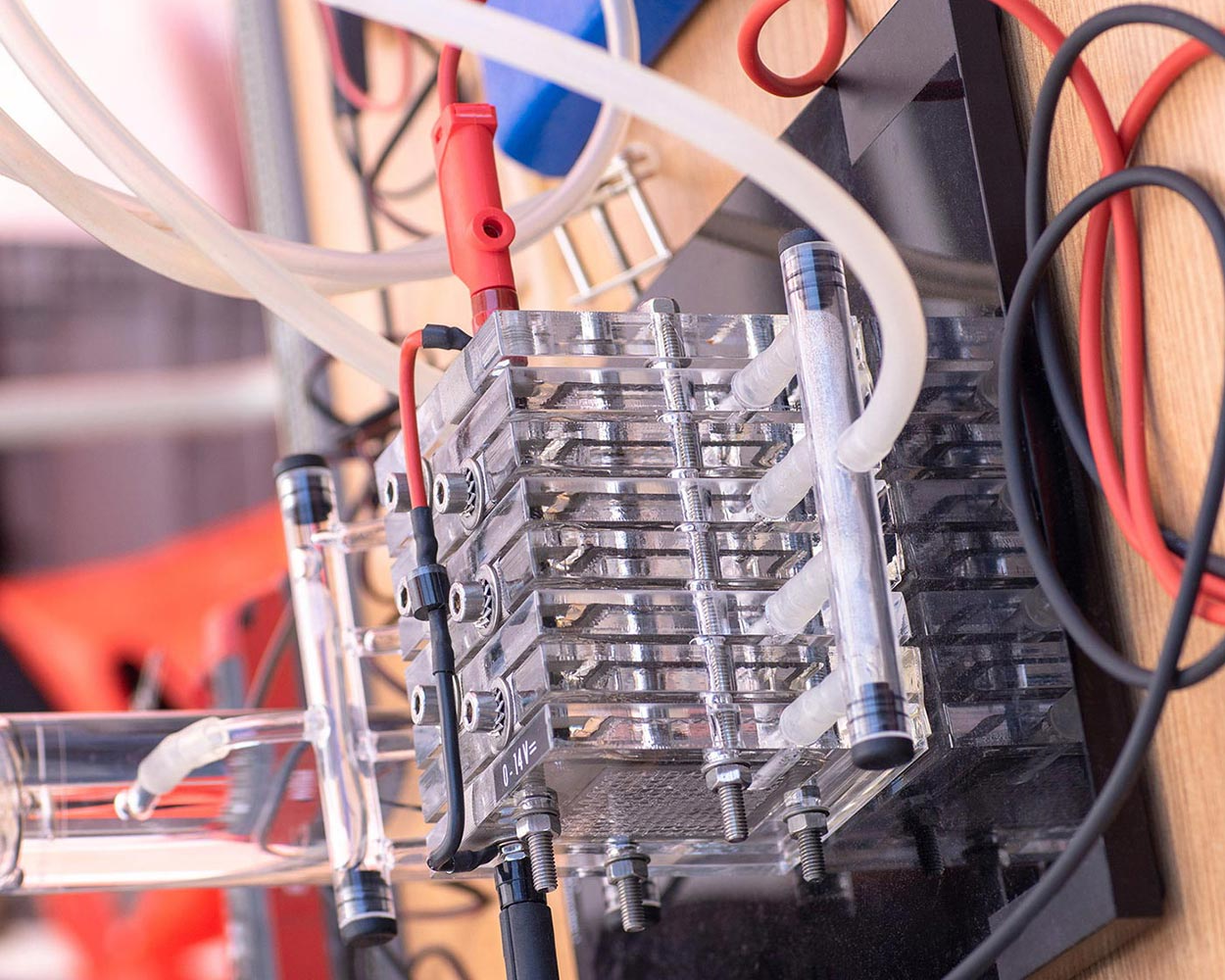
Zero Degradation Found in Latest Test of Aemion+® Alkaline Membrane, Exceeds 2024 Targets
Background
A large-format electrolyzer with an active area of 50 cm2 was assembled using Aemion+® membranes and high-quality alkaline electrodes that have an extended lifespan of up to 20 years. Using these high-quality electrodes allows the assessment of membrane durability without being influenced by the catalyst layer.
The current trial has been ongoing for 2500 hours at the 2024 EU target current density (0.6 A/cm2). The current testing phase builds upon previous durability assessments conducted on Aemion+® membranes. These membranes have successfully operated for over 7500 hours, experiencing minimal system degradation of less than 0.6% per 1000 hours after the initial break-in period, and a total degradation rate of 1.2% per 1000 hours. Furthermore, they have maintained membrane integrity with less than 0.05% measurable degradation per 1000 hours.
Results
The test results revealed remarkably low degradation rates for the electrolyzer, setting a new standard for anion exchange membrane (AEM) technology. This marks the first successful demonstration of stability for anion exchange membrane water electrolyzers (AEMWE) under real-world conditions crucial for large-scale hydrogen production. The cells exhibited no detectable membrane degradation (less than 0.05%), with total system degradation rates (including membrane, catalyst, and flow field) of less than 0.4% per 1000 hours. These results significantly surpass the target set by the EU’s Clean Hydrogen Joint Undertaking Work Programme 2022, which aimed for a measurable system degradation rate of 0.9% per 1000 hours by 2024.
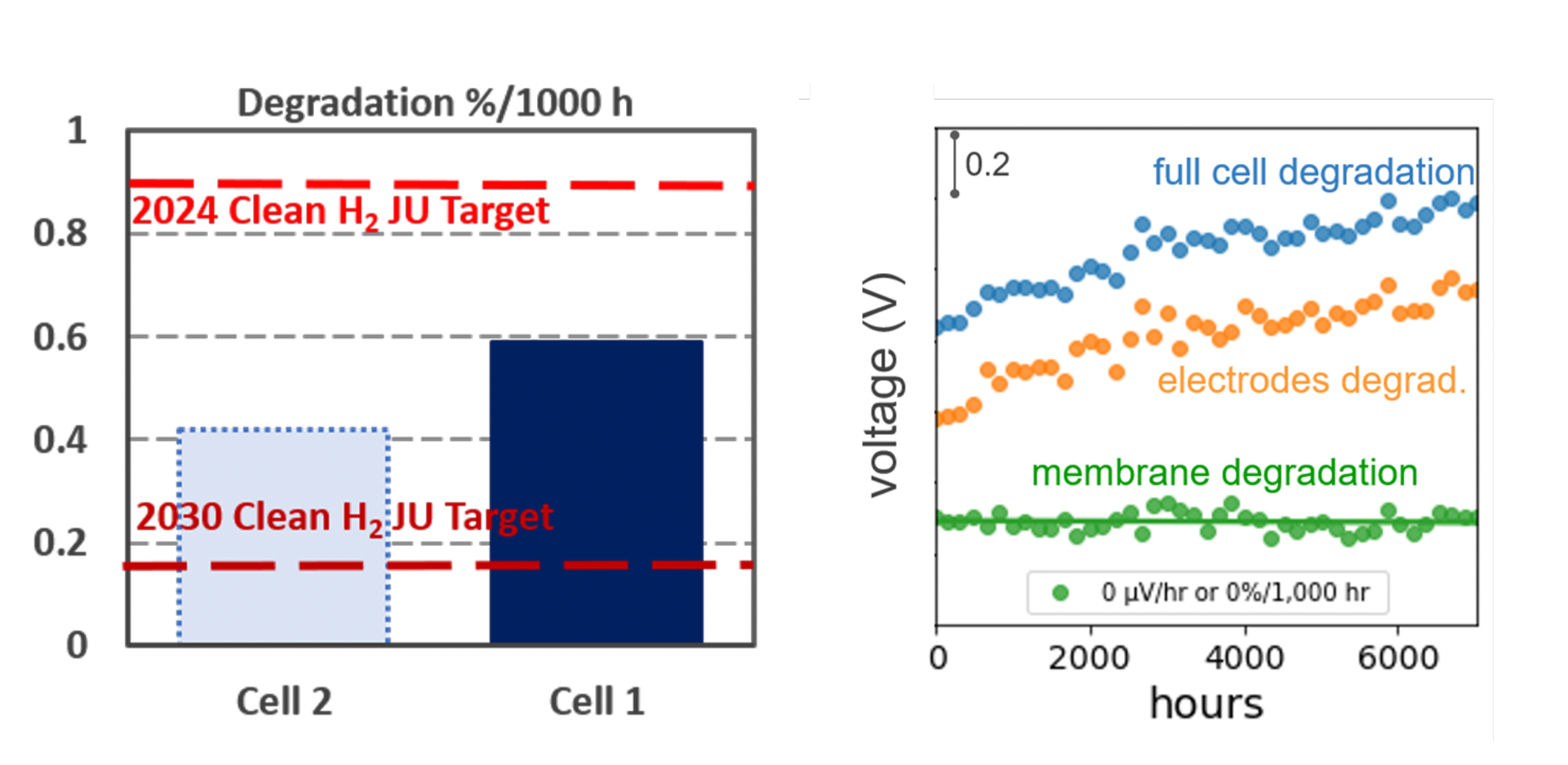
Additionally, most of the system degradation stemmed from the electrodes or the porous metal components responsible for gas and liquid transport. To address this, the porous metal element was removed in the current test, resulting in improved outcomes. Ionomr continues its optimization efforts in collaboration with the National Renewable Energy Laboratory (NREL) as part of the Shell GCxN program. According to Shaun Alia, a staff scientist at NREL, Ionomr membrane electrode assemblies achieved over 1 A/cm2 at 2 V in a hydroxide electrolyte, eliminating the need for iridium with a nonprecious metal anode. These assemblies maintained performance without losses after over 500 hours of operation. This recent durability data builds upon Ionomr's prior success in demonstrating Aemion+® stability in concentrated potassium hydroxide solutions.
For more details, check the latest press release of IONOMR on the stability of AEMION® membranes here.
AEMION+ ® Reinforced Membranes Thickness and Reinforcement Properties
AEMION+ ® Reinforced Membranes Handling, Storage, and Pre-treatment Instructions
Delivery and Initial Condition
Membranes are delivered in the dry, chloride/iodide form. Depending on specific applications and cell designs, assembly may be possible in either the dry form (without pre-treatment) or the wet form (with pre-treatment). The membrane should be exchanged into the ionic form it will operate in while assembled into the cell.
Pretreatment when used in Water Electrolyzers
For optimal results in water electrolysis, prior to use, AF3-HWK9-75 membranes should be removed from the backer and be subjected to a two-step exchange process.
Activation Step 1: Iodide to Chloride Form
Protocol | Temperature [°C] | Electrolyte | Volume Ratio [mL electrolyte/cm2 AEM] | Recirculation | Duration [h] |
Standard (RT) | RT | 3 M KCl | 5.6 | No | 4 |
Reduced Volume | RT | 1 M KCl | 2.2 | Yes, 100 rpm | 6 |
Accelerated | 50 | 3 M KCl | 1.5 | Yes, 100 rpm | 6 |
Activation Step 2: Chloride to Hydroxide Form
Protocol | Temperature [°C] | Electrolyte | Volume Ratio [mL electrolyte/cm2 AEM] | Recirculation | Duration [h] |
Standard (RT) | RT | 1 M KOH | 2.2 | No | 4–6 |
Pretreatment when used in Fuel Cells
For fuel cell applications, soaking for at least 24 hours and 36-48 hours is recommended. Exchange into KOH first may be beneficial for other ion-exchanges such as into the sulfate form.
Checking Conversion after Pretreatment
Verify chemical composition using spectroscopic techniques, like X-ray Fluorescence (XRF) and Energy Dispersive Spectroscopy (EDS), to measure conversion efficiency. Post-conversion, the cell's beginning of life (BOL) high-frequency resistance (HFR) should be below 200 mΩ/cm² or so.
Mounting the Membrane
It is preferable that the membrane then be mounted wet, as differential stresses due to dimensional changes may occur upon drying.
Removal of the Membranes from the Backing Layer
- With clean gloved hands, hold the membrane on its backing layer.
- Take your thumb or a finger and rub against the corner edge of the membrane to produce separation from the backing layer.
- Once corner separation from the backing layer is achieved, carefully and gently, begin to pull the membrane from the backing layer whilst holding the membrane down on a clean dry surface.
- As the backing layer is released, support the membrane as you continuously remove it from the backing layer until all of the membrane has been removed.
- With clean gloves, wet a portion of the membrane/backing layer edge with deionized water; this should aid in separation of the membrane from the backing layer. Repeat the steps in the primary method.
- If the membrane does not separate upon initial wetting, spritz a small amount of water area close to the edge of the membrane and repeat the primary method.
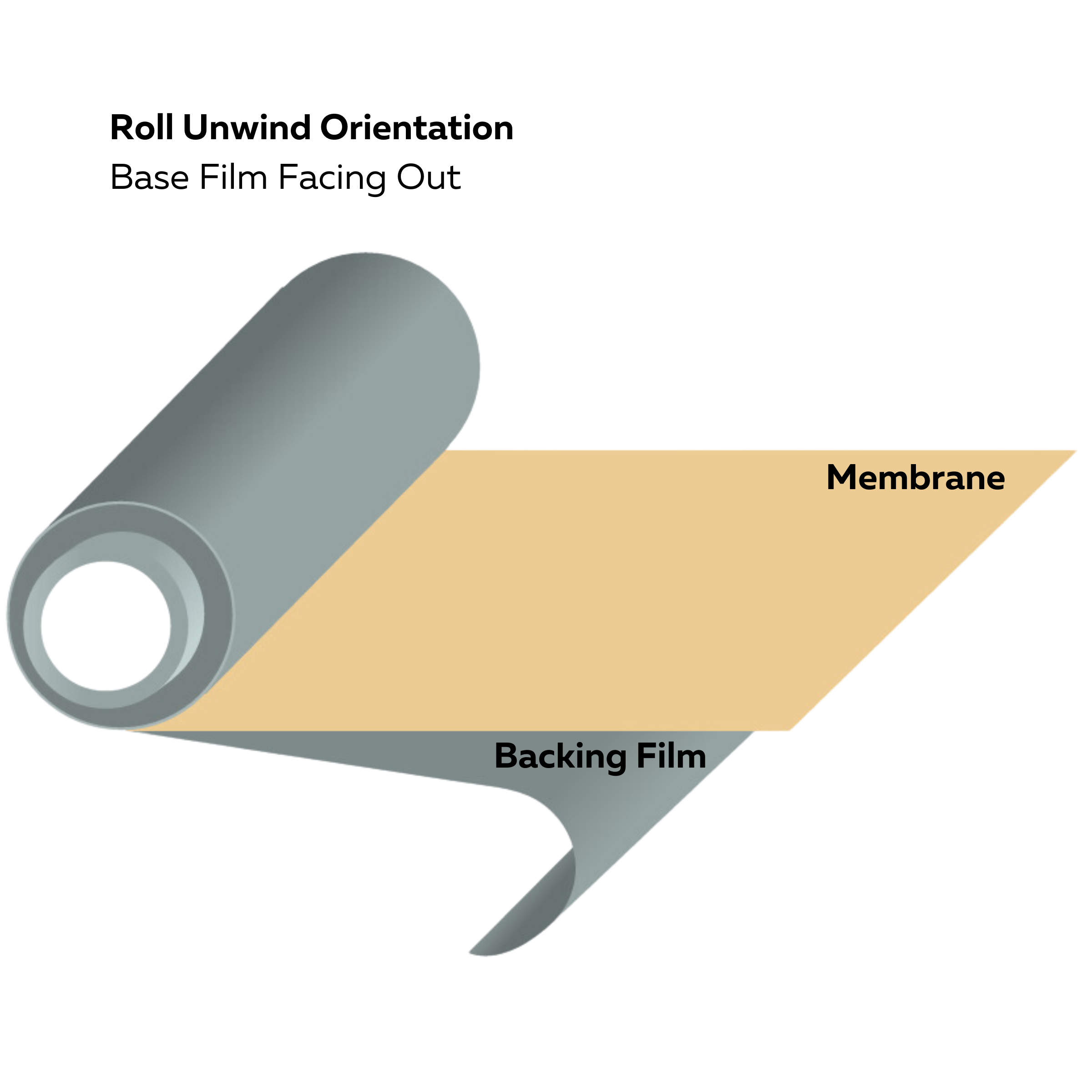